Manufacturing QMS Software: Key Insights and Trends
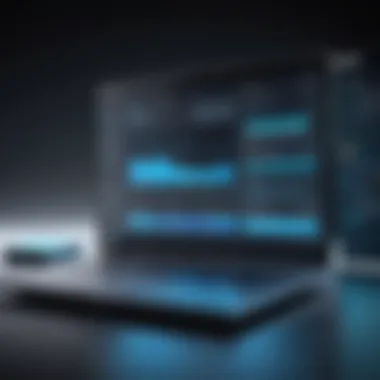
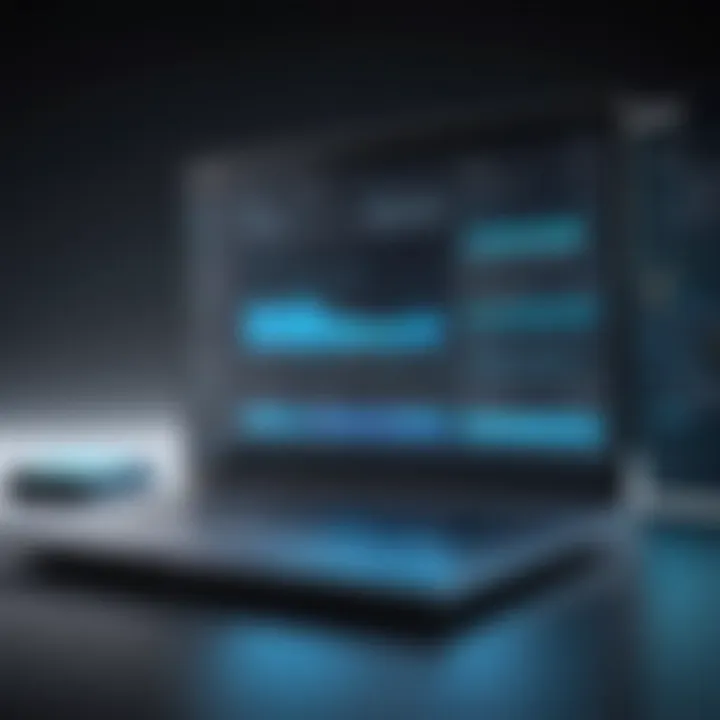
Intro
Quality Management System (QMS) software plays a critical role in enhancing the operational efficiency of manufacturing industries. It is designed to help organizations manage quality control processes effectively. In today's competitive environment, manufacturers must adhere to strict industry standards and regulations while simultaneously striving for excellence in their operations. This necessitates a structured approach to quality management, which is where QMS software comes into play.
This article delves into the key features of manufacturing QMS software, examining its functionalities and components that underpin quality objectives. It will provide insights into how these tools can support compliance with various industry regulations. Additionally, it aims to discuss the advantages of adopting QMS software, the criteria for selecting the right solutions, and future trends that may influence quality management practices. By exploring these aspects, the content seeks to equip decision-makers with the knowledge needed for informed decisions in the realm of manufacturing quality management.
Key Features
Overview of Features
Manufacturing QMS software comprises various features tailored to improve quality control processes. These include:
- Document Control: This allows for the management and storage of quality-related documents, ensuring that all employees reference the most current information.
- Non-Conformance Tracking: It enables organizations to document and track any deviations from established quality standards, aiding in root cause analysis and corrective action plans.
- Audit Management: The software simplifies the auditing process by providing tools for planning, executing, and reporting on audits.
- Training Management: This feature assists in tracking employee training and qualifications to ensure staff are knowledgeable about quality procedures.
Each of these functionalities streamlines workflows, reduces the likelihood of errors, and promotes a culture of continuous improvement within manufacturing operations.
Unique Selling Points
When considering QMS software, several unique selling points set certain solutions apart:
- Integration Capability: The ability to integrate with existing systems, such as ERP or MES, enhances data flow and contextual understanding.
- Real-Time Analytics: Advanced analytics features can provide insights into quality metrics, thereby facilitating quicker decision-making.
- Scalability: Many QMS solutions can scale according to the size and needs of the organization, allowing for adaptability as the business grows.
- User-Friendly Interface: An intuitive interface means reduced training time and higher adoption rates among staff.
These points highlight why specific QMS software might be a better fit for certain manufacturing operations compared to others.
Pricing Structure
Tiered Pricing Plans
The pricing for manufacturing QMS software can vary based on several factors, including the features included and the size of the organization. Commonly, vendors offer tiered pricing plans:
- Basic Plan: Often includes essential features like document control and non-conformance tracking. Suitable for small manufacturers.
- Standard Plan: Adds more features such as audit management and training functionalities. Aimed at medium-sized companies.
- Premium Plan: Provides access to advanced features like real-time analytics and integration capabilities, tailored for larger organizations.
Features by Plan
For those considering different plans, it's essential to align features with organizational needs:
- Basic Plan Features: Document control, Non-conformance tracking
- Standard Plan Features: All Basic features plus Audit management, Training management
- Premium Plan Features: All Standard features plus Real-time analytics, Custom integrations
Understanding the pricing structure helps in making informed decisions that align with both budgetary constraints and operational requirements.
"Effective quality management is not just about compliance; it is about fostering a culture of excellence."
As manufacturing industries continue to evolve, so too will the capabilities of QMS software, paving the way for improved practices and standards in quality management.
Understanding Manufacturing QMS Software
Quality Management System (QMS) software plays a critical role in the manufacturing sector. The importance of this topic lies in the transformation it brings to quality control processes within organizations. As manufacturers strive to meet increasingly high standards in product quality and compliance, understanding the functionalities and benefits of QMS software becomes essential.
Definition of QMS Software
Quality Management System software is a designed tool that helps manufacturing organizations manage their quality processes efficiently. Typically, it encompasses a range of functionalities aimed at ensuring that products meet required standards and specifications. QMS software can facilitate various tasks including documentation, reporting, tracking non-conformances, and managing audits.
In simple terms, it serves as a digital framework that assists companies in maintaining quality across all operations. The software offers a centralized platform where data is collected, analyzed, and utilized to enhance quality standards. Its attributes are particularly useful for complying with industry regulations, thus avoiding legal complications and ensuring customer trust.
Role in Manufacturing
The role of QMS software in manufacturing is multifaceted. Foremost, it helps to raise manufacturing standards by allowing organizations to identify and address quality issues proactively. Tools embedded in the software enable real-time monitoring of processes and performance. Consequently, this ensures that manufacturers can react quickly to any discrepancies.
Moreover, QMS software aids in driving process improvements through data analysis. By scrutinizing historical data, organizations can uncover patterns that might indicate areas for enhancement. This analytical capability encourages a culture of continuous improvement.
"Quality management is not just a task; it's a commitment that reverberates throughout the organization."
In addition to quality assurance, QMS software also simplifies compliance with various regulations. The software often includes built-in compliance checks aligned with international standards, such as ISO certifications. This alignment not only fosters trust among consumers but can also yield greater market opportunities.
To summarize, understanding Manufacturing QMS software is crucial for organizations aiming to enhance their operational efficiencies. It bridges the gap between compliance and quality, ultimately leading to improved product output and customer assurance.
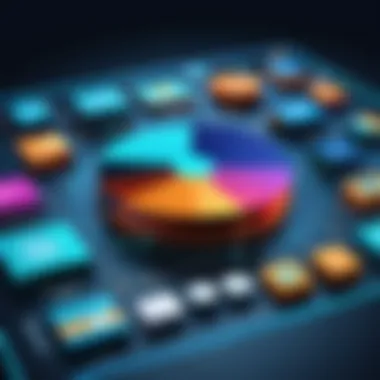
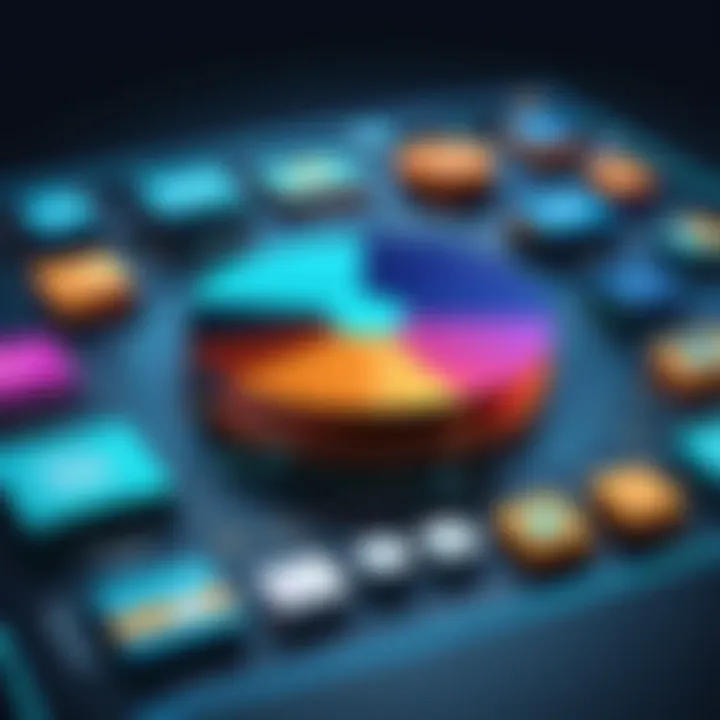
Key Features of QMS Software
Understanding the key features of Quality Management System (QMS) software is essential for manufacturing industries aiming to enhance operational efficiency and maintain rigorous quality control standards. These crucial elements not only streamline processes but also support compliance with established regulations. When selecting a QMS software solution, it is vital that organizations understand these features and how they align with their specific needs.
Document Management
Document management is a fundamental feature of QMS software. It encompasses the storage, retrieval, and control of documents related to quality processes. Effective document management ensures that all personnel have access to the current versions of critical documents such as procedures, work instructions, and policies. This minimizes confusion and reduces the risk of using outdated information. With QMS software, the automation of document revisions and approvals becomes possible, which saves time and enhances accountability. Security protocols embedded in these systems protect sensitive information and ensure only authorized users have access.
Audit Management
Audit management is another crucial component within QMS software. This feature allows organizations to plan, conduct, and report audits efficiently. A comprehensive audit management system aids in identifying non-compliance issues, assessing risks, and implementing corrective actions. It provides tools to create audit schedules, store findings, and track follow-up activities. By simplifying audit processes, organizations can ensure that they meet compliance standards and continuously improve their operational practices.
Non-Conformance Management
Non-conformance management is vital for identifying and addressing deviations from quality standards. This feature allows organizations to document non-conformance incidents, initiate investigations, and implement corrective actions. A robust non-conformance management system tracks the lifecycle of an issue from identification to resolution. By analyzing trends in non-conformance, organizations can pinpoint systemic issues, which helps in preventing future occurrences. This process supports the continuous improvement philosophy essential in manufacturing.
Change Management
Change management within QMS software enables organizations to handle modifications in processes, procedures, or materials systematically. This feature ensures that changes are carefully evaluated, approved, and documented. Effective change management helps minimize disruptions and ensures that stakeholders are informed of alterations impacting their work. It includes tracking changes, analyzing impact, and ensuring that training is provided where necessary. In a manufacturing context, fostering a controlled approach to change is critical for maintaining quality and compliance.
"QMS software provides a framework through which organizations can organize their quality processes, ensuring a continual focus on improvement and compliance."
Benefits of Implementing QMS Software
Implementing Quality Management System (QMS) software can lead to significant advantages for manufacturing organizations. In todayβs competitive landscape, it is vital for companies to ensure they adhere to high-quality standards while maintaining operational effectiveness. The focus here is on the specific benefits that QMS software can provide to manufacturers to enhance overall performance.
Improved Compliance
Compliance with regulations is a cornerstone of effective manufacturing operations. QMS software helps organizations meet industry standards such as ISO 9001, by providing a structured approach to compliance documentation and auditing. By using automated workflows, businesses can ensure that all procedures comply with relevant regulations. This software also allows for easy tracking of compliance metrics, making it simple to generate reports for regulatory bodies. As a result, the risk of non-compliance reduces significantly, which in turn minimizes potential legal liabilities and financial penalties.
Enhanced Operational Efficiency
Another compelling benefit of QMS software is its ability to enhance operational efficiency. By streamlining workflows, reducing manual effort, and enabling better resource allocation, manufacturers can optimize their processes. The software allows for real-time tracking of production activities, which can pinpoint inefficiencies and areas for improvement. In addition, the ability to automate repetitive tasks frees up human resources to focus on more strategic initiatives. Thus, by implementing QMS software, organizations can reduce waste, increase productivity, and ultimately lower operating costs.
Data-Driven Decision Making
QMS software facilitates data collection and analysis, promoting informed decision-making. With robust reporting tools, managers can access a wealth of insights regarding quality metrics, production trends, and compliance statuses. This data-driven approach allows manufacturers to identify patterns, anticipate issues, and make proactive adjustments to operations. Moreover, utilizing data analytics strengthens the foundation for continuous improvement initiatives, leading to better overall quality in products and processes.
Increased Customer Satisfaction
Customer satisfaction is vital for maintaining a competitive edge. QMS software supports an organizationβs efforts to consistently meet or exceed customer expectations. By tracking customer feedback through the software, manufacturers can identify specific areas where improvements are needed. The ability to enact corrective and preventive actions swiftly ensures that issues do not escalate, enhancing customer trust and loyalty. Additionally, consistent quality leads to fewer returns and complaints, further solidifying positive customer relationships.
"Implementation of QMS software can redefine an organization's approach to quality, compliance, and customer engagement."
Selecting the Right QMS Software
Choosing the appropriate Quality Management System (QMS) software is crucial for manufacturing organizations. This selection impacts not only compliance with industry standards but also overall operational efficiency. A well-suited QMS can streamline processes, foster collaboration, and enhance data management. It is essential to consider multiple factors to ensure that the selected software aligns with the specific needs of the organization.
Assessing Organizational Needs
Before diving into software options, it is vital to assess the unique needs of your organization. This means evaluating current systems and identifying gaps in performance.
- Understanding Objectives: Define what you aim to achieve with the QMS. Are you focusing on regulatory compliance, process optimization, or quality control?
- Identifying Pain Points: Gather feedback from teams involved in quality management processes. This can reveal inefficiencies or areas for improvement.
- Scalability Requirements: Consider future growth. Will the software be able to accommodate increased production demands or added functionalities?
Completing this assessment prepares the groundwork for a more informed decision during the selection process.
Evaluating Software Features
Once the organizational needs are clear, the next step is to evaluate potential software features that meet these requirements. Here are critical features to consider:
- User Interface: A simple and intuitive interface enhances user adoption and reduces training time.
- Integration Capabilities: Assess how well the software integrates with existing systems, including ERP or supply chain management solutions.
- Reporting and Analytics: Look for robust reporting capabilities that facilitate data analysis and support decision-making.
- Document Control: Effective document management is key in QMS to ensure that all records are up-to-date and compliant with regulations.
Understanding which features are non-negotiable for your organization adds clarity to the selection journey.
Understanding Implementation Costs
The costs associated with implementing QMS software can vary significantly. It is essential to evaluate all elements of costs to avoid unexpected expenses.
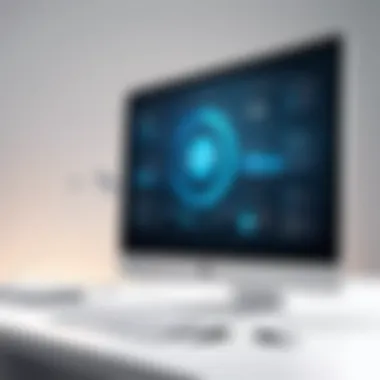
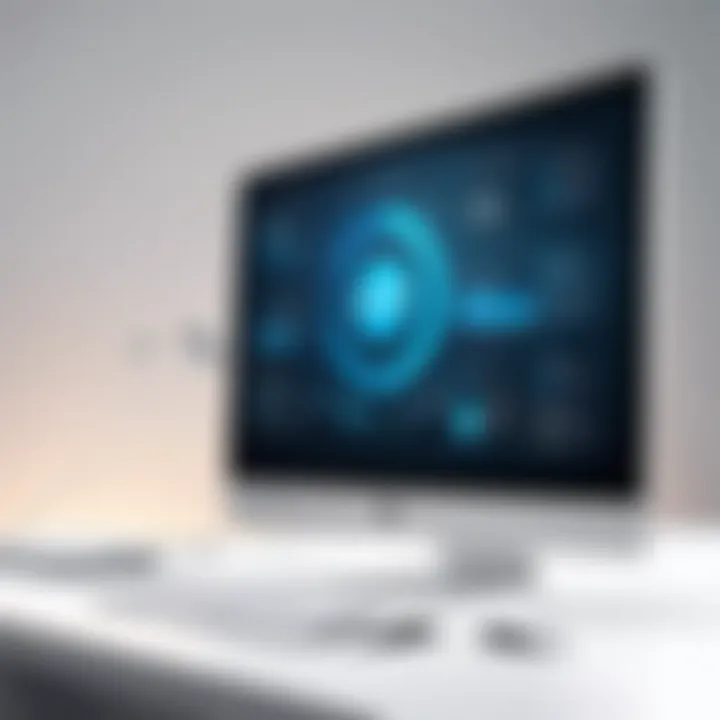
- Initial Licensing Fees: Most QMS software platforms have upfront costs associated with licensing. Ensure this aligns with your budget.
- Implementation Support: Determine if the vendor offers installation support or if additional training will be necessary for staff.
- Ongoing Maintenance: Consider long-term costs, including software updates and customer support.
A comprehensive understanding of costs facilitates a smooth selection and implementation process, avoiding pitfalls down the line.
Integrating QMS Software with Existing Systems
Integrating Quality Management System (QMS) software with the existing systems is critical for organizations aiming to streamline their processes. This integrative step ensures that the adoption of new technology does not disrupt the current workflows. Instead, it enhances the operational capabilities and maintains a seamless flow of information throughout different departments.
The importance lies in several factors. First, businesses often use various software solutions to manage different aspects of operations such as production planning, supply chain, and customer relationship management. Integrating QMS software within these frameworks allows for a unified approach to data management. This robust connection can significantly reduce data silos, ensuring that every department has access to the same information in real time.
Moreover, integration improves efficiency. It eliminates the need for manual data entry, which is not only time-consuming but also prone to errors. Automated data transfer between systems minimizes discrepancies, fostering accuracy in reporting and decision-making. Consequently, manufacturing firms can respond more swiftly to compliance requirements or operational challenges, enhancing their agility in a dynamic environment.
API Integrations
Application Programming Interfaces (APIs) play a crucial role in the integration of QMS software with existing systems. APIs allow different software applications to communicate and share data seamlessly. For manufacturing organizations, this means that their QMS can work alongside production scheduling tools, inventory management systems, and even enterprise resource planning (ERP) software.
This interactivity offers several benefits:
- Enhanced Data Sharing: APIs enable automatic updates of quality data across all systems, maintaining uniformity and promoting informed decision-making.
- Customizable Solutions: Organizations can select specific functionalities from various systems, tailoring their QMS integration to meet unique operational needs.
- Scalability: As businesses evolve, APIs make it easier to add new functionalities or connect new software solutions without major overhauls.
However, organizations should also consider the security associated with API integrations. Maintaining data integrity and protecting intellectual property should be a priority throughout the integration process.
Data Migration Considerations
Data migration is another significant aspect of integrating QMS software with existing systems. This process involves transitioning existing data from old systems to the new QMS. Although it may seem straightforward, careful planning is essential to prevent data loss or corruption.
Several key considerations include:
- Data Assessment: Evaluate the quality and relevance of existing data. Not all data may be suitable for migration, and organizations should discard unnecessary or outdated information.
- Mapping Data Fields: Ensure compatibility between data fields in existing systems and the new QMS. This step is vital to maintain accurate reporting and usability.
- Testing the Migration Process: Before full migration, conduct tests to identify potential issues. Performing pilot migrations can reveal discrepancies early on, allowing adjustments before the actual transition.
- Training Staff: Equip staff with training about the new system's functionalities. Proper understanding helps reduce resistance to new technologies and increases overall acceptance.
In summary, integrating QMS software with existing systems is not just beneficial but essential for thriving in a competitive manufacturing landscape. Through adequate API integrations and strategic data migration planning, companies can achieve substantial improvements in quality management and operational efficiency.
Regulatory Compliance and Standards
Understanding regulatory compliance and standards is essential in the realm of manufacturing QMS software. These regulations ensure that organizations meet certain quality and safety benchmarks crucial for operational success. Staying compliant mitigates risks, enhances reputation, and often leads to increased market opportunities. Organizations that neglect these requirements may face severe penalties, including fines or operational shutdowns.
ISO Standards Overview
ISO standards provide a framework for quality management at an international level. The ISO 9001 standard is particularly significant, as it sets the criteria for a quality management system that organizations can follow. This standard encourages companies to establish processes for consistent quality in their products and services.
Key points regarding ISO include:
- Customer focus: Every product or service should meet customer needs.
- Leadership: Strong leadership emphasizes the importance of a quality management system.
- Engagement of people: Involving staff at all levels leads to better performance.
- Process approach: Consistent results arise from managing activities as processes.
By adhering to ISO standards, manufacturers can enhance their credibility and marketability. Moreover, companies can utilize ISO-compliant QMS software to automate compliance and reporting processes, ultimately saving time and resources.
Industry-Specific Regulations
Industry-specific regulations differ based on the sector, impacting how QMS software is implemented. For instance, pharmaceuticals must comply with the FDA regulations, necessitating rigorous documentation and control of processes. In the automotive industry, manufacturers often adhere to IATF 16949 standards, which emphasize continuous improvement and defect prevention.
Understanding these industry-specific regulations is vital for the successful deployment of QMS software. This involvement may include:
- Adhering to labeling requirements: Certain industries need to follow specific labeling rules that the QMS software should facilitate.
- Conducting regular audits: Continuous assessment helps maintain a compliant environment.
- Training and certification of staff: Employees must be trained to understand regulatory standards relevant to their roles.
"In the complex landscape of manufacturing, regulatory compliance isn't just a requirement; it's a cornerstone for sustainable success."
By integrating these regulatory requirements into QMS software, organizations can streamline compliance efforts, reduce redundancies, and enhance overall effectiveness in quality management. Through vigilant adherence to these standards, manufacturers not only uphold their legal obligations but also gain a competitive advantage in their respective markets.
Future Trends in QMS Software
In today's fast-evolving manufacturing landscape, staying ahead requires more than just existing quality management systems. It necessitates an awareness of emerging trends that could redefine quality management. The importance of examining these trends lies in understanding how to improve operational efficiency and compliance. QMS software must adapt to new technologies to remain relevant. This section highlights key trends such as artificial intelligence, cloud-based solutions, and blockchain technology.
Artificial Intelligence and Machine Learning
Artificial intelligence (AI) and machine learning (ML) represent a paradigm shift in how quality management systems operate. By leveraging these technologies, manufacturers can analyze vast amounts of data more efficiently. AI can help in automating quality control processes by identifying patterns and anomalies that may be missed by human eyes. As a result, businesses can proactively address potential issues before they escalate.
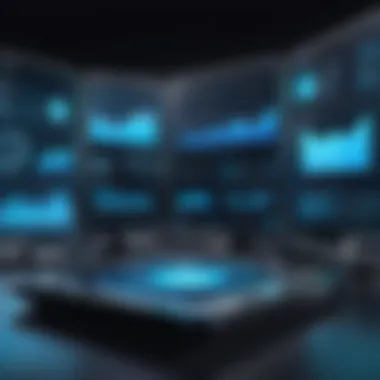
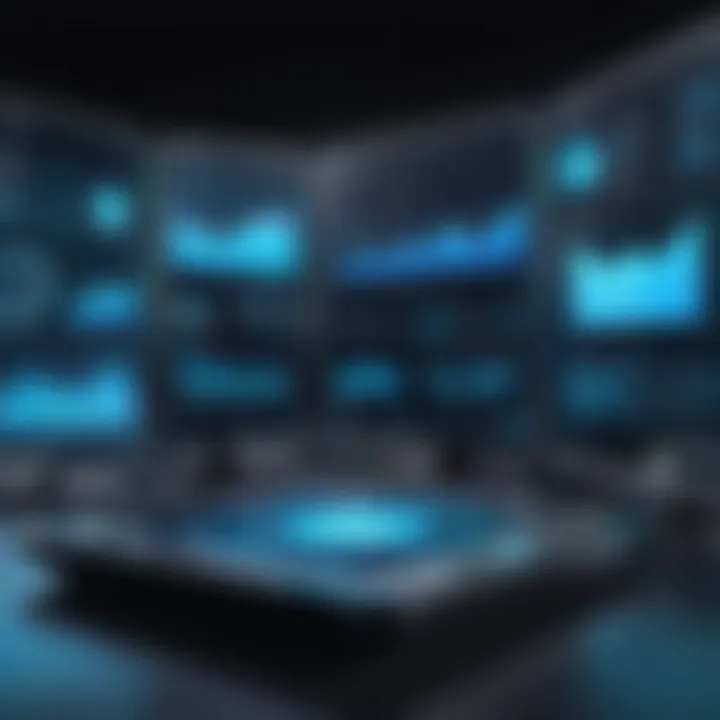
Key benefits of AI in QMS include:
- Predictive analytics: AI tools can forecast equipment failures or quality issues based on historical data.
- Automated reporting: Reporting processes become streamlined, allowing teams to focus on improvements rather than data gathering.
- Real-time monitoring: Continuous data analysis helps in making swift adjustments to processes, improving product quality.
As these technologies evolve, manufacturers that integrate AI and ML could see significant improvements in their quality outcomes.
Cloud-Based Solutions
The shift toward cloud-based solutions represents another trend that transforms quality management systems. These platforms offer numerous advantages over traditional on-premises software. Flexibility and accessibility stand at the forefront. Cloud-based QMS solutions can be accessed anytime, anywhere, enabling remote team collaboration and real-time updates.
Considerations for adopting cloud solutions:
- Cost-effectiveness: Cloud solutions often have lower upfront costs compared to traditional software.
- Scalability: Businesses can easily scale their QMS as they grow without significant investment in infrastructure.
- Data security: Many cloud providers offer robust security measures, though it is important to assess provider capabilities.
Organizations are increasingly seeking these solutions to enhance their operational efficiency and data management capabilities.
Blockchain Technology in Quality Management
Blockchain technology, while often associated with cryptocurrencies, has considerable potential in quality management systems. Its core feature, decentralized and immutable data recording, ensures that all transactions are traceable and verifiable. This can enhance transparency and accountability in quality processes.
Benefits of integrating blockchain include:
- Traceability: Complete visibility of the supply chain can help identify the source of quality issues quickly.
- Data integrity: Once recorded, data cannot be altered without consensus, ensuring authenticity.
- Enhanced collaboration: All stakeholders can access real-time data, promoting trust and collaboration in the quality management process.
As manufacturers seek to bolster their QMS frameworks, blockchain technology emerges as a promising avenue to enhance quality assurance practices.
In summary, the future of QMS software is intertwined with these emerging technologies. By embracing AI, cloud solutions, and blockchain, manufacturers can improve quality management processes and ensure they meet the evolving demands of the industry.
Real-World Case Studies
Real-world case studies offer enlightening insights into the application and effectiveness of Manufacturing Quality Management System (QMS) software. These examples illustrate how organizations navigate the complexities of quality management. By analyzing successes and failures, businesses can extract valuable lessons that inform their strategies for adopting QMS software.
Successful QMS Implementation
When implemented successfully, QMS software can transform a manufacturing operation. For instance, consider the case of XYZ Manufacturing Co. This company faced challenges such as inconsistent product quality and frequent regulatory audits. After adopting a comprehensive QMS solution, they streamlined their quality processes. The introduction of automated document management and audit tracking significantly reduced compliance errors.
The benefits of this software were clear:
- Enhanced Traceability: Quality records became more accessible, reducing time spent searching for documents.
- Regulatory Compliance: Consistent adherence to ISO standards led to improved audit outcomes.
- Efficiency Gains: Productivity increased as employees focused on value-added activities rather than manual processes.
These improvements allowed XYZ Manufacturing to restore customer confidence and boost sales. Their experience underscores the importance of selecting software that aligns with specific operational needs and regulatory requirements.
Lessons Learned from Software Failures
Not every QMS software implementation is without obstacles. Notably, ABC Electronics Inc. attempted to introduce a new QMS solution without proper planning. They rushed through the selection process, failing to assess user needs thoroughly. As a result, the software lacked essential features necessary for their operations.
This led to several challenges:
- Employee Resistance: Workers were hesitant to adopt the new system, leading to inconsistencies in quality checks.
- Data Overload: The tool generated excessive data that overwhelmed staff, causing them to miss crucial insights.
- Increased Costs: The company incurred additional expenses to rectify mistakes made during implementation.
The experience of ABC Electronics Inc. highlights critical lessons in the adoption of QMS software, including the need for a structured selection process and user training. Failure to engage employees early in the process can undermine the effectiveness of the software and lead to poor outcomes.
βSuccessful implementations are led by careful planning and understanding of user needs.β
Through these case studies, it becomes evident that QMS software can offer significant advantages when implemented thoughtfully. However, it also serves as a warning about the pitfalls of neglecting proper preparation and user engagement.
Culmination
The conclusion of this article on Manufacturing QMS Software is crucial for summarizing the essential insights derived from the discussions presented. It acts as a reflective point for decision-makers in manufacturing who consider the adoption of Quality Management Systems. A well-structured conclusion emphasizes the significance of incorporating QMS software into manufacturing processes. It underlines the benefits such as improved compliance, higher operational efficiency, and enhanced quality control.
Summary of Key Insights
Throughout this article, we explored various elements that shape the understanding of Manufacturing QMS Software. Key insights include:
- QMS Definition and Role: Quality Management Systems are tools that streamline processes while maintaining quality standards. They facilitate the documentation and management of compliance, providing a structured approach to quality assurance.
- Critical Features: Important functions such as Document Management, Audit Management, and Non-Conformance Management are integral to the success of these systems. Each feature contributes uniquely to enhancing product quality and operational performance.
- Benefits Realized: Implementing QMS Software can lead to substantial improvements in organizational processes. Benefits like data-driven decision-making and increased customer satisfaction are noted as major impacts realized by organizations utilizing such systems.
- Trends in Technology: The integration of AI, cloud solutions, and blockchain technology signify the future trajectory of QMS Software. Keeping pace with these trends is essential for companies aiming for sustained compliance and efficiency.
Final Thoughts on QMS Software
The examination of Manufacturing QMS Software reveals its transformative potential in the manufacturing landscape. It is more than a compliance tool; it is a strategic asset. For businesses looking to thrive in competitive markets, the implementation of QMS software is not merely advisable; it is essential.
In summary, the insights presented in this article serve as a roadmap for organizations considering the integration of Quality Management Systems. The path toward efficient, quality-driven manufacturing hinges on the right software selection tailored to specific needs and industry standards. Companies must remain vigilant about evolving technologies and regulatory demands to leverage the full potential of QMS solutions effectively.
"Quality is not an act, it is a habit." β This underscores the continuous commitment required to maintain excellence in manufacturing while utilizing QMS Software.