Harnessing Process Maps for Organizational Excellence
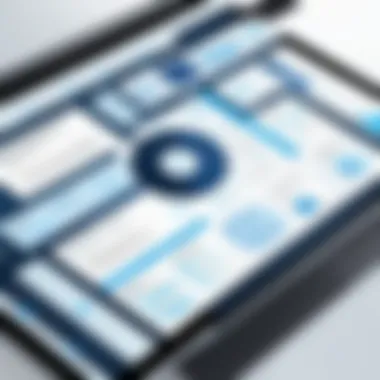
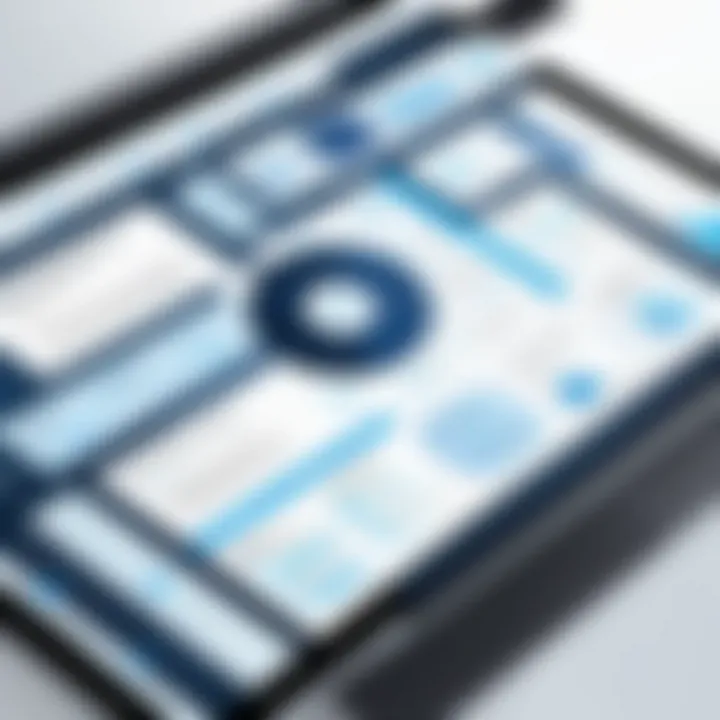
Intro
In today's complex business environment, companies strive for efficiency and agility. One of the essential tools that help organizations achieve these goals is the process map. Understanding what process maps are and how they can be utilized is crucial for improving operational workflows. A process map visually represents the steps involved in a specific process, highlighting the sequence of activities, decisions, and interactions among different stakeholders.
The increasing need for clarity in business operations necessitates an in-depth discussion about the role of process maps. They can serve as the backbone for process improvement, innovation, and decision-making. In this article, we will explore key features, methodologies for creating effective process maps, and the implications they hold for strategic planning. By leveraging these tools, businesses can unlock significant value and streamline their operations.
Key Features
Overview of Features
Process maps come with several defining characteristics that make them invaluable for companies:
- Clarity and Comprehension: They simplify complex processes into visual formats, making it easier for stakeholders to understand the flow of work.
- Identification of Inefficiencies: By laying out each step, companies can identify bottlenecks or redundant tasks that may hinder productivity.
- Standardization: Process maps promote consistency by standardizing how tasks are executed across various departments.
- Facilitating Communication: They provide a common reference point for discussions around process improvements, helping to align the team.
Unique Selling Points
The unique selling points of utilizing process maps in organizations include:
- Enhanced Collaboration: Process maps foster teamwork by integrating input from various departments, which leads to more informed decision-making.
- Continuous Improvement: Organizations can regularly update process maps to reflect changes, enabling an agile approach to process optimization.
- Documentation and Training Aid: They serve as valuable documentation for onboarding new employees or training existing staff on specific procedures.
"Process maps are not just diagrams; they are blueprints for transforming and optimizing organizational processes."
Methodologies for Creating Effective Process Maps
Creating a process map involves several steps that ensure clarity and alignment. Through collaborative sessions, teams should define objectives clearly, gather necessary data, and outline each step involved in the process.
- Define the Process Scope: Determine what process is to be mapped and identify key stakeholders.
- Collect Data: Gather information on each step, including inputs, outputs, and responsible parties.
- Draft the Map: Utilize software tools such as Microsoft Visio or Lucidchart to create a visual representation of the process.
- Validate the Map: Review the draft with stakeholders to ensure accuracy and completeness.
- Implement and Update: Once validated, the process map should be distributed and used as a living document for regular updates.
Process maps, when executed effectively, become more than just visualsβthey guide strategic planning and decision-making processes within organizations.
Understanding Process Maps
Process maps are critical tools for visualizing how various tasks and activities interrelate within an organization. Understanding process maps is essential in honing in on organizational efficiency. By mapping out processes, companies pinpoint inefficiencies and facilitate communication among teams. Clarity in mapping ensures that everyone involved grasps their roles, ultimately enhancing productivity.
Definition of Process Maps
A process map is a visual representation of a process, detailing the various steps involved to achieve a specific outcome. These maps illustrate how tasks flow from one to another and identify the sequence of activities. They can range from simple diagrams to more complex flowcharts that incorporate multiple variables and decision points. The primary purpose of a process map is to clarify processes so that stakeholders can understand the workflow and identify areas for improvement.
Importance in Organizational Context
In a competitive business landscape, the significance of process maps cannot be overstated. Here are a few key reasons why they play a vital role in organizations:
- Facilitate Better Communication: Everyone from executive teams to front-line employees can have a clearer understanding of processes. This shared knowledge reduces misunderstandings and increases cohesion among team members.
- Promote Continuous Improvement: By regularly reviewing process maps, organizations identify areas of waste and inefficiency, driving a culture of continuous improvement.
- Support Compliance: Documented processes assist in compliance audits. They provide clear evidence that companies follow required steps, which is essential for regulatory adherence.
- Improving Training and Onboarding: New employees benefit from process maps as visual aids. These tools aid in onboarding, making it easier for new hires to grasp their roles quickly.
Understanding process maps provides a foundation for examining deeper topics related to their practical application and benefits. They are not just diagrams, but instruments of strategic planning that pave the way for informed decision-making in organizations.
The Different Types of Process Maps
Process mapping is an essential practice for organizations aiming to improve their efficiency and transparency. The different types of process maps serve unique purposes and cater to various needs within a company. Understanding these distinctions is vital for selecting the appropriate map for specific projects or analyses. In this section, we will explore four primary types: flowcharts, swimlane diagrams, value stream maps, and process flow diagrams. Each type not only offers unique visual perspectives but also brings distinct benefits that facilitate decision-making and process optimization.
Flowcharts
Flowcharts are among the most common types of process maps. They visually represent workflows in a series of interconnected shapes and arrows, demonstrating how a process progresses from start to finish. Flowcharts are particularly valuable in breaking down complex processes into manageable steps, making it easier for teams to understand workflows.
Key characteristics of flowcharts include:
- Simplicity: They employ standardized symbols, making them easy to read.
- Flexibility: Flowcharts can adapt to various types of processes, from basic daily tasks to more intricate operational procedures.
- Comprehensibility: They are accessible to people at all levels, reducing barriers in communication.
Flowcharts can effectively highlight areas for improvement, such as redundant steps or bottlenecks. Furthermore, they support training by providing clear visuals of processes that new employees can familiarize themselves with swiftly.
Swimlane Diagrams
Swimlane diagrams offer a structured approach to process mapping by categorizing tasks by different participants or departments. They help clarify roles and responsibilities while showing how elements interact across lanes. This type of diagram is especially beneficial in environments where multiple stakeholders are involved.
Consider the following key aspects of swimlane diagrams:
- Role clarity: Lines (or lanes) represent different team members or processes, clearly defining who is responsible for each part of the workflow.
- Complexity management: They navigate through complicated processes in a linear manner, reducing confusion when multiple parties are engaged.
- Collaboration enhancement: Swimlane diagrams facilitate better coordination and communication among team members.
By illustrating how processes flow across various organizational boundaries, swimlane diagrams can be a critical tool for optimizing workflow and fostering accountability within teams.
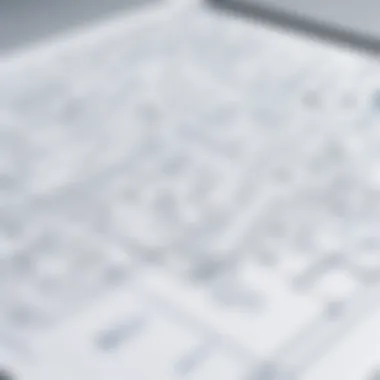
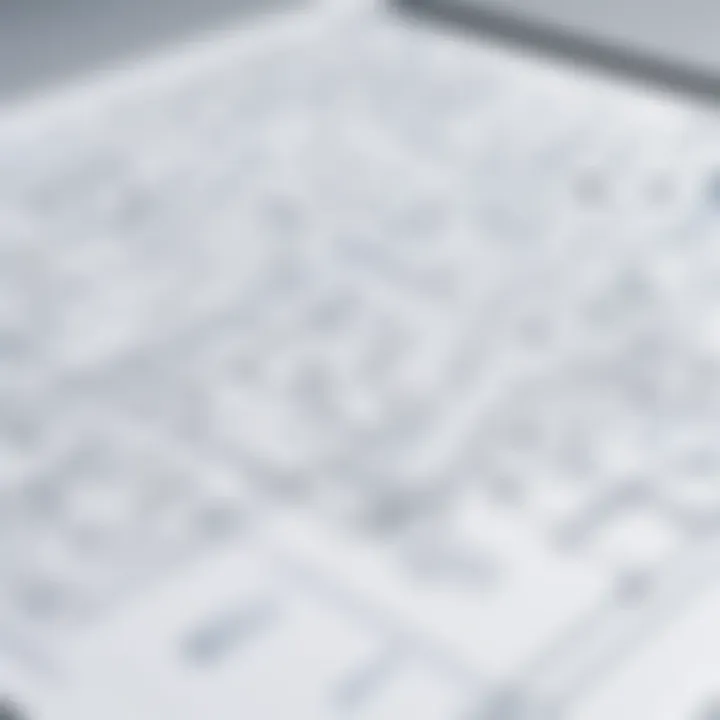
Value Stream Maps
Value stream maps focus on the flow of materials and information from the beginning to the end of a process. They aim to identify value-adding and non-value-adding activities, aiding organizations in enhancing their efficiency. This type of mapping is especially useful in manufacturing and service environments, where understanding the value chain is crucial.
The advantages of value stream maps include:
- Focus on efficiency: Organizations can pinpoint waste and redundancies within the process, directly affecting profitability and resource utilization.
- Holistic view: They provide a comprehensive perspective on how processes interconnect and contribute to overall efficiency.
- Lean practices: Value stream maps are integral to lean methodologies, guiding organizations toward optimized operations by emphasizing value creation.
Engaging with value stream maps allows companies to streamline processes, often leading to significant cost savings and better resource management.
Process Flow Diagrams
Process flow diagrams provide a high-level overview of a process and its components, using standardized symbols and connections. Unlike detailed flowcharts, process flow diagrams focus on major operations within a system rather than on minute details. These diagrams are especially beneficial in technical environments or production settings.
Essential features of process flow diagrams include:
- Simplicity: They reduce complexities, focusing on the core components of a process.
- Integration: These diagrams commonly integrate with technical designs and system specifications, which can be critical in engineering projects.
- Standardization: They follow defined rules for symbol usage, ensuring consistency across different processes and industries.
In summary, process flow diagrams help convey large amounts of information succinctly while remaining understandable to both specialized and general audiences.
"Choosing the right type of process map can significantly impact your organization's ability to streamline operations and communicate effectively."
By understanding and utilizing these different types of process mapsβflowcharts, swimlane diagrams, value stream maps, and process flow diagramsβcompanies can enhance their operational efficiencies and foster an environment of continuous improvement.
Use Cases of Process Mapping in Companies
Process maps serve as fundamental tools in organizations, playing a significant role across multiple functions. Understanding their use cases aids businesses in identifying areas for improvement and streamlining operations. This section discusses several key uses of process mapping, highlighting specific elements and benefits.
Workflow Optimization
Workflow optimization revolves around improving efficiency and productivity. Process maps facilitate this by providing a clear visual representation of tasks, sequences, and responsibilities. When workflows are mapped out, organizations can pinpoint bottlenecks and redundancies in their processes. By analyzing these diagrams, teams can initiate meaningful changes that result in faster completion cycles and reduced operational costs.
For instance, a manufacturing company may utilize process maps to chart the steps involved in assembly. This enables them to identify delays caused by resource waiting times. Consequently, they can adjust the workflow to ensure resources are available when needed, leading to a smoother operation. The ability to pinpoint these areas accurately is indispensable for any organization aiming for continuous improvement.
Compliance and Risk Management
Compliance and risk management are critical components of organizational health. Process maps help document compliance requirements and illustrate how existing processes align with these regulations. By mapping out processes, companies can systematically assess areas where compliance may be lacking. This reduces the risk of penalties and reinforces the importance of adhering to relevant standards.
Moreover, having a clear process map allows teams to anticipate risks effectively. They can visualize potential points of failure in their processes and devise mitigation strategies accordingly. For example, in the financial sector, process maps can depict the flow of data relevant to regulations such as the General Data Protection Regulation (GDPR). This not just aids in compliance, but strengthens the overall governance framework.
Training and Onboarding
Training and onboarding new employees can be time-consuming and complex. However, having process maps enhances the efficiency of these initiatives. By providing new hires with clear, graphical representations of their roles and workflows, organizations enable faster assimilation into the company culture and processes.
For instance, human resources may use process maps to illustrate the steps involved in employee onboarding. This serves not only as a guide for new employees but also as a reference for trainers. This clarity helps ensure that the training is effective and consistent across the board.
Process Documentation
Process documentation is often considered a corner stone of operational excellence. Process maps provide a valuable means of documenting workflows in a structured manner. This is essential for performance reviews, audits, and future process improvements. Well-documented processes serve as a knowledge base that can be referred to at any time.
Additionally, process maps aid in community knowledge sharing within organizations. When employees leave, their knowledge doesn't have to be lost. A comprehensive library of process maps allows for smooth transitions and continuity in operations.
"Effective process documentation through process mapping can foster an environment of learning and adaptation, crucial for any organization in todayβs fast-paced ecosystem."
In summary, the use cases for process mapping in companies are diverse and impactful. Workflow optimization, compliance and risk management, training and onboarding, and process documentation are essential facets where process maps immensely contribute to organizational success. As businesses seek to improve their operations, leveraging process mapping becomes indispensable.
Methodologies for Creating Process Maps
Creating effective process maps involves a structured approach that encompasses various methodologies. These methodologies provide the framework necessary to analyze and visualize processes systematically. Understanding how to create process maps is essential, as it can significantly influence organizational efficiency and clarity.
Identifying Objectives
Before starting the mapping process, it is critical to define clear objectives. What do you want to achieve with the process map? Clarity in objectives guides the entire mapping effort.
- Focus on specific outcomes: Determine if the goal is to optimize workflows, communicate processes effectively, or train new employees.
- Align with business needs: Ensure the objectives resonate with the broader organizational goals.
- Measure success: Establish metrics that will allow you to evaluate the effectiveness of the process map once developed.
By identifying objectives early, teams can create purpose-driven maps that yield valuable insights and actionable outcomes.
Gathering Input from Stakeholders
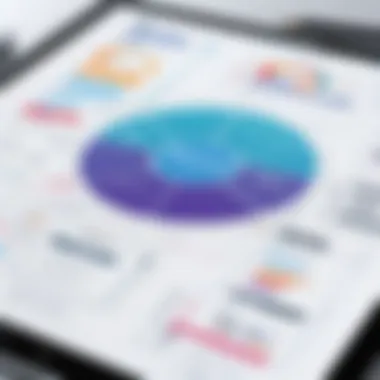
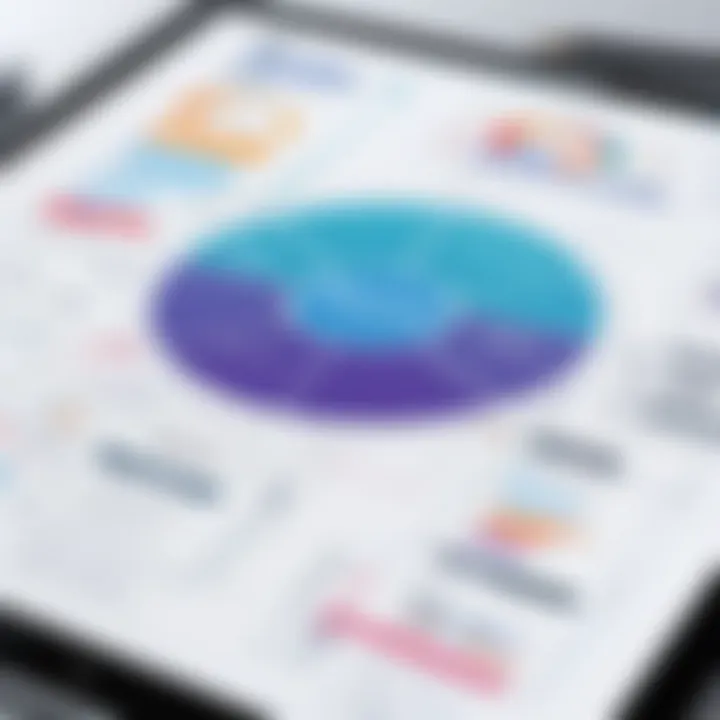
Success in process mapping relies heavily on stakeholder engagement. Input from those who are involved in or affected by the processes is indispensable.
- Conduct interviews: Talk to employees at different levels to gather diverse perspectives.
- Utilize workshops: Organize collaborative sessions where stakeholders can brainstorm and contribute to the mapping process.
- Anonymous surveys: Collect feedback in a less intimidating manner, which can glean honest insights.
This step ensures that the process maps are grounded in reality and reflect the actual practices within the organization.
Mapping Current Processes
Mapping existing processes requires a detailed and methodical approach. This often involves:
- Creating flow diagrams: Use tools like Lucidchart or Microsoft Visio to visually represent workflows.
- Documenting step-by-step actions: Note down each step, decision point, and stakeholder involvement.
- Reviewing existing documentation: Analyze any current documents related to the processes, as they can provide valuable information.
The goal is to capture the true essence of how processes operate within the organization. This mapping serves as the foundation for further analysis and optimization.
Analyzing and Improving Processes
Once the current processes are documented, the next step is analysis. This involves:
- Identifying bottlenecks: Look for steps that slow down the process or create redundancies.
- Assessing effectiveness: Evaluate whether each step adds value or can be modified for better performance.
- Involving team feedback: Discuss findings with stakeholders to refine the analysis and gain additional insights.
The improvement phase could lead to recommending changes that enhance efficiency, reduce costs, or improve service quality. This can be a continuous cycle, where mapping, analysis, and optimization reinforce each other.
Process maps are not just documentation tools; they are strategic instruments that provide insights into organizational dynamics.
By integrating these methodologies, organizations can harness the power of process mapping as a tool for improvement and excellence.
The Impact of Process Maps on Decision Making
Process maps serve as a vital link in the chain of decision-making within companies. By providing a visual representation of workflows, these maps enable decision-makers to understand processes holistically. This clarity not only improves the communication across departments but also enhances collaboration among teams. Effective decision-making hinges on accurate data and insights, and process maps facilitate this by illustrating workflows in a manner that reveals intricate connections and dependencies.
Enhanced Clarity and Communication
One of the core advantages of process maps is their ability to enhance clarity. When processes are complex, it is easy for miscommunication to occur. Process maps simplify the intricacies, presenting a straightforward visual that delineates responsibilities, timings, and outcomes. This improvement in clarity aids discussions among team members and stakeholders. Clear communication channels ensure that everyone involved has the same understanding of workflows and expectations. Furthermore, this visual nature supports different learning styles, enhancing comprehension across diverse teams.
Identifying Gaps and Redundancies
The utility of process maps extends to identifying areas where improvements are necessary. When reviewing a process map, decision-makers can easily spot inefficiencies such as bottlenecks or duplicated efforts. Understanding these gaps is critical for operational success. By examining flows from start to finish, organizations can highlight unnecessary steps or potential points of failure in their processes. Addressing these issues often results in streamlined operations, which can significantly improve productivity and reduce costs.
Facilitating Data-Driven Decisions
Process maps also play an important role in supporting data-driven decisions. In an era where information is abundant, being able to distill that data into actionable insights is essential. Process maps integrate data points with process flows, providing a context that makes the numbers meaningful. This integration enables leaders to make informed choices based on real information rather than intuition alone. By visualizing workflows alongside key performance indicators, organizations can direct their efforts toward strategies that drive results.
"Effective decision-making is not just about having data. Itβs about interpreting that data in the context of your processes. Process maps provide that context."
Implementing Technology in Process Mapping
Technology plays a crucial role in modernizing the approach to process mapping within organizations. With rapid advancements in software solutions and digital tools, process maps can now be created and maintained more efficiently. This efficiency directly translates into improved operational effectiveness. Technology enables better visualization, collaboration, and analysis of processes, making it easier for teams to communicate effectively and make informed decisions.
In today's business environment, leveraging technology in process mapping can offer significant benefits, such as:
- Increased Accuracy: Automated tools reduce human error, ensuring precise mapping of processes.
- Enhanced Collaboration: Cloud-based platforms allow multiple stakeholders to work on process maps in real-time, increasing synergy.
- Data Integration: Technology can link process maps with data analytics tools, enabling organizations to extract valuable insights instantaneously.
Implementing technology in this area requires careful consideration of tools and systems that align with organizational objectives and user needs.
Software Tools for Process Mapping
Choosing the right software tool is essential for creating effective process maps. Various tools provide different functionalities tailored to distinct needs. Some widely used software solutions include:
- Lucidchart: A popular web-based application for drawing diagrams and process maps, offering a user-friendly interface.
- Microsoft Visio: A comprehensive tool that allows for detailed flowchart development and integrates well with other Microsoft products.
- Bizagi: Specializes in business process modeling and includes automation capabilities to enhance workflow.
Each tool has its unique strengths, making it important for companies to evaluate their requirements before adopting a particular solution. Factors such as user-friendliness, integration capabilities, and customization options should be considered during selection.
Integrating with Existing Systems
Successful implementation of process mapping technology hinges on its ability to integrate seamlessly with existing systems. Organizations often use various software solutions for customer relationship management (CRM), enterprise resource planning (ERP), and other operational processes. Consequently, ensuring that the process mapping tools harmonize with these systems is vital for optimal performance.
When planning the integration, it helps to:
- Assess compatibility with current technologies to enable smooth data flow across platforms.
- Consider employee training to ensure that staff members can use both the mapping tools and integrate them with other systems effectively.
- Develop a clear roadmap to manage the transition, minimizing disruption while enhancing existing processes.
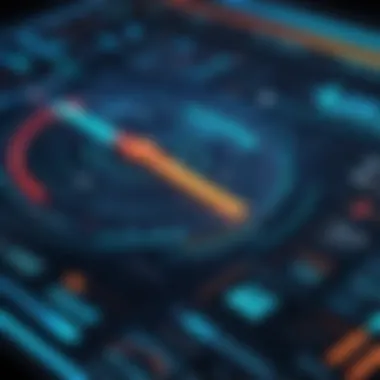
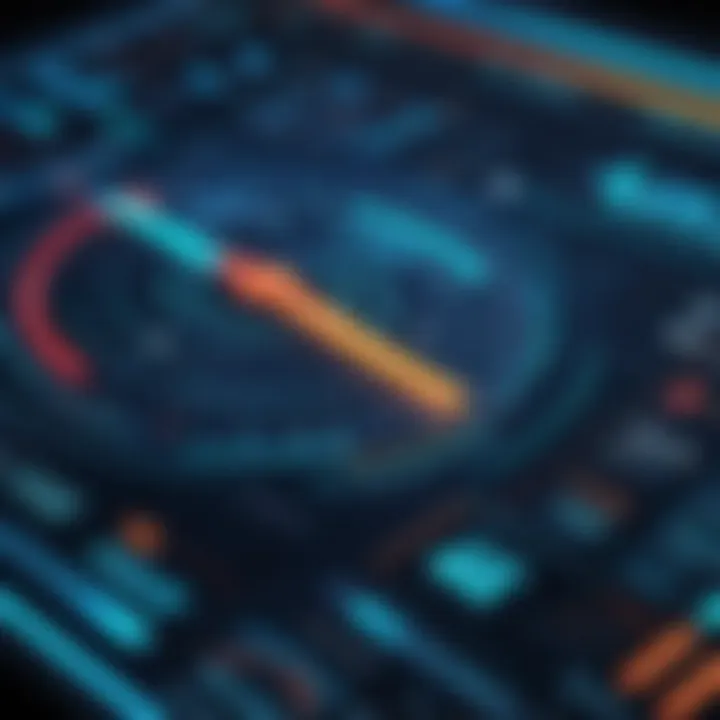
"The goal of technology is to make processes easier, faster, and more reliable. Process mapping tools must align with this vision to be effective."
In summary, implementing technology in process mapping is not just about choosing the right tools. It involves strategic integration with existing systems and ensuring that all stakeholders are equipped to utilize the technology effectively. This careful planning and execution will lay a solid foundation for improved organizational efficiency.
Challenges in Process Mapping
Process mapping is a valuable tool in enhancing organizational efficiency and decision-making. However, it is not without its challenges. Addressing these challenges is crucial. Understanding the potential obstacles can help organizations effectively implement process mapping and achieve desired outcomes.
Resistance to Change
Resistance to change is one of the most common hurdles organizations face when introducing process maps. Employees may be accustomed to their existing workflows, and any alteration can induce discomfort. It can lead to skepticism about the benefits of adopting new processes.
Organizations must actively manage this resistance. Communication is key. Clear explanations of how process maps can improve efficiency and reduce frustrations in the long run can help alleviate concerns. Involving team members in the mapping process can create a sense of ownership. This involvement can transform skepticism into enthusiasm. Training sessions should be organized to ensure all employees are comfortable with new systems.
Overall, creating a culture that encourages adaptability is essential for successfully implementing process maps.
Data Overload
Another challenge is data overload. When creating process maps, organizations may collect vast amounts of information. This can lead to confusion and overwhelm. It is important to distinguish between relevant and irrelevant data. Overloading the process map with excessive information can obscure its purpose.
To mitigate data overload, organizations should focus on simplicity and clarity. Use summary data and high-level insights when possible. Essential elements of the process should be prioritized, ensuring that the map remains functional and easily interpreted. Incorporating feedback loops during the mapping process can help refine and distill the information.
Case Studies of Successful Process Mapping
Examining case studies of successful process mapping provides a concrete understanding of how theoretical concepts translate into real-world applications. By looking at specific examples, we uncover essential elements, benefits, and considerations that can guide other organizations in adopting process mapping techniques. These case studies offer valuable insights into how various companies have harnessed process mapping to overcome challenges and streamline operations effectively.
As organizations face increasing complexities in their workflows, it becomes paramount to identify strategies that promote efficiency and compliance. Successful case studies reveal strategies that worked, mistakes made, and lessons learned. This depth of knowledge can significantly influence decision-making processes in similar businesses.
"The essence of understanding process maps lies not just in learning their theory but in recognizing their practical implications through real examples."
Company A: Streamlining Operations
Company A, a mid-sized manufacturing firm, faced significant challenges in meeting demand due to inefficient production processes. Tasks were often duplicated, and communication gaps between departments led to delays. To rectify this, the management decided to implement a comprehensive process mapping exercise.
In this case, various flowcharts were created to visualize the production process clearly from order entry to delivery. The maps outlined not just the individual tasks but also who was responsible for each. This clarity provided insight into the workflow, enabling the identification of bottlenecks. With the process maps in hand, the company made strategic adjustments:
- Reallocation of Resources: Shifting teams according to peak demand hours improved output rates.
- Enhanced Communication Tools: Integrating a centralized platform for all departments resulted in reduced response times.
- Standard Operating Procedures (SOPs): The documentation created by the process maps served as references for training new staff.
After implementing these changes, Company A observed marked improvement in productivity, with a 25% increase in output within three months, alongside improved employee morale and reduced burnout.
Company B: Improving Compliance
Company B operates within the highly regulated financial services sector. The complexity of regulatory compliance was a significant pain point, costing the firm not only time but also substantial fines for oversight. To ensure that compliance was embedded in operations, the company adopted process mapping as a proactive measure.
By utilizing swimlane diagrams, Company B was able to delineate responsibilities across various departments clearly. Each lane represented a different department's role in compliance, providing a visual map of the entire process. This layout helped identify steps that were frequently overlooked, such as document approvals and audits.
Key benefits realized from this initiative included:
- Increased Accountability: Employees were more aware of their roles in the compliance process.
- Streamlined Audits: The transparency in processes made it easier to prepare for audits, resulting in smoother inspections.
- Regular Training and Updates: The process maps facilitated regular training, helping staff stay up to date with regulatory changes.
As a result, Company B not only achieved a 40% reduction in compliance issues but also fostered a culture of accountability and continuous improvement.
In summary, these case studies underscore the critical role of process mapping in enhancing operational efficiency and compliance. Each example illustrates how, when applied thoughtfully, process maps can lead to substantial improvements, ultimately driving organizational success.
Future Trends in Process Mapping
Understanding the future trends in process mapping is crucial for any organization looking to maintain competitive advantage. As industries become increasingly dynamic, the methods used for process mapping are evolving. By recognizing these trends, companies can harness new opportunities and better align their strategies. Automation and advancements in artificial intelligence play pivotal roles in this transformation. These elements not only enhance efficiency but also provide substantial insights into operational effectiveness.
Automation in Process Mapping
Automation is reshaping the landscape of process mapping. This involves employing software tools and technologies that can design and update process maps with minimal human intervention. By automating repetitive tasks in the mapping process, organizations can save time and reduce the risk of human error. The benefits include:
- Increased speed: Automated tools can create process maps in lightning speed compared to manual efforts.
- Consistency: They ensure uniformity in representing processes, which simplifies understanding across departments.
- Real-time updates: With automated systems, any changes in a process can be reflected instantly in the corresponding maps, which keeps everyone informed.
The use of automation not only streamlines mapping processes but also allows companies to focus more on analyzing and refining their methodologies.
Artificial Intelligence and Process Mapping
Artificial Intelligence (AI) is another significant trend shaping the future of process mapping. AI technologies can analyze vast amounts of data to identify patterns and inefficiencies that might not be visible to human observers. Here are some important points about AI in process mapping:
- Predictive analysis: AI can predict outcomes based on historical data, helping organizations plan more effectively.
- Adaptive process improvement: AI can learn from ongoing process execution to recommend optimizations in real-time.
- Enhanced decision-making: By providing data-driven insights, AI facilitates informed decisions that align with business objectives.
AI's integration into process mapping is not just a trend; it is becoming a necessity for organizations aiming for operational excellence.
"As companies embrace AI, the potential to redefine how processes are visualized and optimized becomes remarkably attainable."
In summary, as the business environment continues to evolve, understanding and leveraging future trends in process mapping is imperative. Automation and AI are at the forefront, providing organizations with tools to not only enhance efficiency but also ensure continuous improvement in their operational strategies.