Comprehensive Guide to Equipment Inspection Software
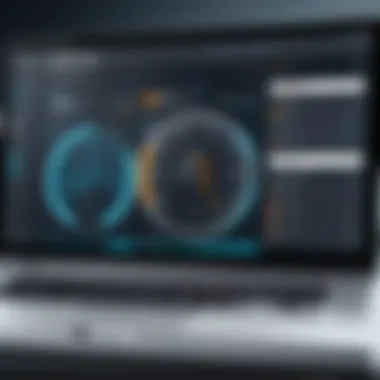
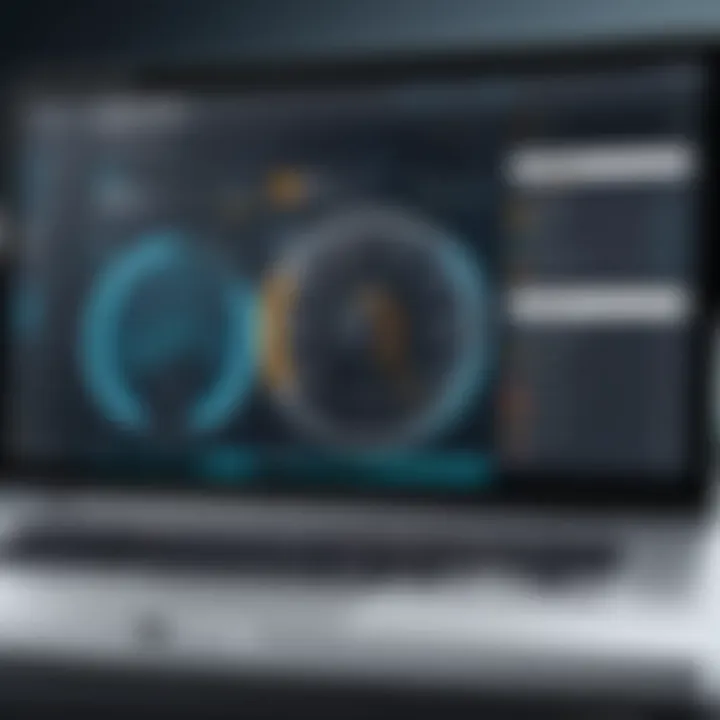
Intro
In today's business landscape, equipment inspection software is becoming essential. As organizations face increasing operational demands, compliance obligations, and safety regulations, this technology offers a pathway to streamlined processes. Gaining insights into equipment conditions can prevent failures, enhance productivity, and ultimately cut costs.
This article explores various facets of equipment inspection software. It will shed light on key features of these tools, their pricing structures, and their potential impacts on business operations. Whether you are a decision-maker, an IT professional, or a business owner, understanding the nuances of this software can significantly inform your choices and strategies.
As we navigate through this guide, the discussion will center on critical aspects necessary for making informed decisions. From assessing unique selling points to analyzing market options, the goal is to equip you with comprehensive knowledge in this domain.
"In the realm of equipment management, proactive inspection leads to enhanced reliability and performance."
Stay with us as we delve deeper into the mechanics and benefits of equipment inspection software, starting with the key features that define it.
Prolusion to Equipment Inspection Software
Equipment inspection software plays crucial role in operational efficiency and safety across various industries. As businesses seek to enhance their safety protocols and compliance measures, this software becomes more than a useful tool; it becomes a necessity for robust risk management and operational clarity. Implementing such software allows businesses to track, manage, and document equipment inspections effectively, thereby reducing the risks associated with machinery failures and non-compliance penalties.
The software typically aims to automate and simplify the inspection process. This includes the creation of inspection checklists, tracking of inspections in real-time, and generating detailed reports instantly. The advantages are significant. By digitalizing the inspection process, companies can decrease human error, ensure timely inspections, and create a historical record of all activities.
Key Elements of Equipment Inspection Software
- Data Accuracy: Digitally capturing inspection results helps minimize mistakes often seen in paper-based systems. Errors can lead to severe consequences, impacting safety and costs.
- Real-Time Monitoring: With mobile and web access, inspection data can be updated in real-time, allowing managers to make informed decisions instantly.
- Compliance Tracking: Ensuring that all equipment meets necessary regulations can be systematically monitored, saving time and resources.
Considerations for Implementation
Implementing equipment inspection software requires careful thought about organizational needs and existing processes. Challenges can arise from resistance to change within the organization. Training staff adequately and ensuring proper integration with existing systems are critical steps toward successful implementation. Additionally, cost implications need to be analyzed; the initial investment might be considerable, but the long-term savings and enhanced safety can provide substantial returns.
"Automation elevates inspection processes beyond traditional methods, ensuring thoroughness and compliance."
This narrative highlights that equipment inspection software is not merely a technological addition but a strategic enhancement to operational protocols. By embracing this change, businesses can not only safeguard their operations but also improve overall productivity.
Understanding Equipment Inspections
Understanding equipment inspections is crucial for organizations aiming to maintain operational integrity. It encompasses a systematic review of machinery and tools to ensure they function safely and effectively. This process not only prevents accidents but also protects assets and increases longevity of equipment. An effective inspection process is an integral part of any maintenance strategy, influencing both productivity and compliance with industry regulations.
Definition of Equipment Inspection
Equipment inspection refers to the methodical evaluation of tools, machinery, and systems. This evaluation assesses functionality, wear, and safety standards. Inspections can be routine, scheduled regularly, or unscheduled, often triggered by specific incidents or performance concerns. The focus is on identifying potential issues before they translate into costly failures or operational mishaps. Effectively, this acts as a proactive measure against downtime and accidents that could derail business operations.
Importance in Various Industries
The importance of equipment inspections spans across multiple sectors, each with unique requirements and implications.
- Manufacturing: In manufacturing plants, regular inspections minimize the risk of equipment breakdowns. They ensure production lines operate without interruption, which is vital for meeting delivery schedules.
- Construction: Construction sites require adherence to strict safety regulations. Routine inspections help prevent accidents, ensuring worker safety while maintaining compliance with OSHA standards.
- Healthcare: In healthcare settings, inspections guarantee the reliability of medical equipment. This is critical in providing safe patient care and avoiding liability issues.
- Transportation: In transportation, especially in logistics and shipping, well-maintained vehicles are essential for safety and efficiency. Equipment inspections ensure that all vehicles are roadworthy, reducing the likelihood of accidents.
Understanding the various facets and importance of these inspections leads to better strategic decisions surrounding equipment management. An informed approach can bolster an organization's operational effectiveness and legal compliance.
Key Features of Equipment Inspection Software
Key features of equipment inspection software play a critical role in determining its effectiveness and utility across various industries. These features not only enhance user experience but also ensure that businesses can meet compliance requirements efficiently. Understanding and leveraging these traits optimizes the inspection processes, leading to significant reductions in operational risks.
User Interface and Experience
A user-friendly interface is paramount in equipment inspection software. The interface serves as the primary point of interaction for users, whether they are field inspectors or administrative personnel. A clean and intuitive layout allows users to navigate the software with ease.
Incorporating straightforward menus and easily accessible functions fosters an environment in which users can focus on their inspections rather than struggling to understand the tool.
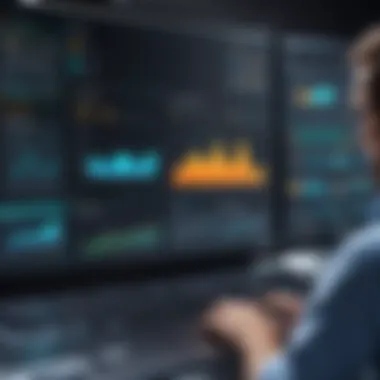
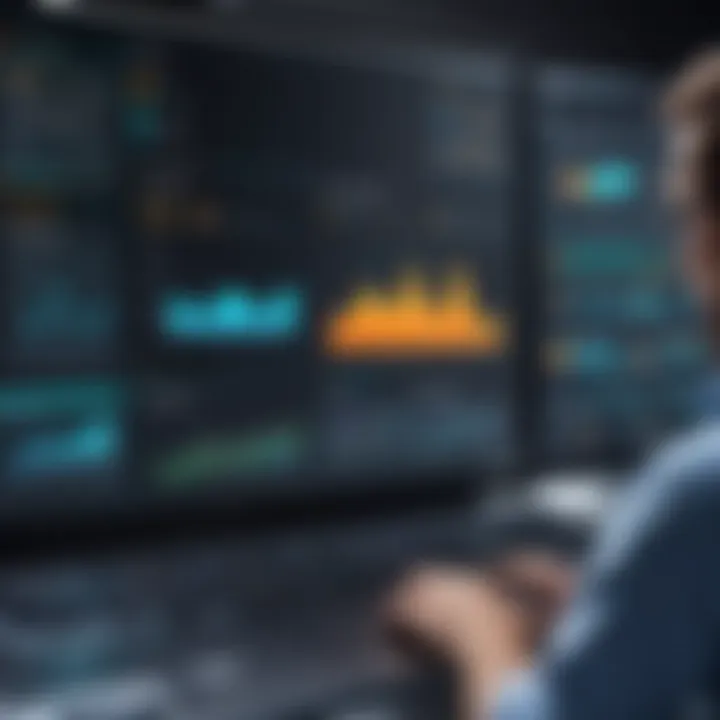
Moreover, a positive user experience directly correlates with productivity. Training new employees becomes less challenging when the software is easy to use. An engaging user interface can also facilitate quicker data entry, which is crucial during time-sensitive inspections.
Mobile Access and Functionality
In today’s mobile-centric world, access to equipment inspection software on various devices is vital. Mobile functionality allows inspectors to conduct assessments in real-time, capturing data as they move through an environment. This accessibility can significantly enhance the workflow, enabling seamless communication between field workers and the central management team.
Mobile access ensures that critical information is always at hand, reducing the delay in reporting and decision-making. For instance, applications like SafetyCulture's iAuditor enable users to create checklists, capture photos and videos, and share insights immediately after an inspection.
Data Collection and Reporting
Effective data collection methods are essential in equipment inspection software. This feature allows for the systematic gathering of important data during inspections. The software should permit customization of questions or fields based on the specific equipment or regulatory requirements.
Reporting functionalities are equally crucial. Users must be able to generate comprehensive reports effortlessly after inspections. Features that allow for automated report generation save significant time and ensure accuracy. These reports not only help in compliance checks but also serve as a valuable reference for future inspections.
Benefits of Implementing Equipment Inspection Software
Implementing equipment inspection software provides numerous advantages to businesses of different sizes and sectors. As organizations increasingly rely on precise monitoring and analysis, the software stands out as a catalyst for improvement in compliance, safety, and overall operational efficiency. Understanding these benefits can aid decision-makers in maximizing their resources and minimizing risks, which is crucial in today’s competitive environment.
Enhancing Compliance and Safety
Regulatory compliance is a significant factor for many industries, making it imperative for organizations to stay ahead of their legal obligations. Equipment inspection software streamlines this process by automating compliance-related tasks, ensuring all inspections follow set guidelines. The program generates reports that fulfill regulatory requirements more efficiently than manual documentation could.
Safety is equally crucial. With thorough inspections recorded digitally, organizations can easily track the performance history of their equipment. This capability allows them to identify recurring issues, thus fostering a proactive approach to maintenance and repair. Moreover, it strengthens accountability among team members, as inspection timelines and results are easy to monitor.
"The promptness of addressing safety issues can significantly reduce accidents in workplaces."
Streamlining Operations
Operating a business involves numerous processes that demand coordination and diligence. Equipment inspection software offers a central hub for managing these processes, allowing users to schedule inspections, monitor progress, and gather results in real time. This leads to better time management and resource allocation.
Automated notifications ensure that deadlines for inspections or maintenance are not missed. Staff can focus their attention on critical tasks instead of worrying about the scheduling of inspections. Having a clear picture of equipment status helps reduce delays in operational workflows.
Reducing Downtime and Costs
Equipment failures can result in substantial downtime, leading to financial losses. The use of inspection software facilitates proactive maintenance, helping predict potential failures before they occur. Doing so reduces unexpected breakdowns and associated costs.
Ultimately, organizations achieve significant cost savings by using such software. Predictive maintenance lowers the need for emergency repairs, avoids operational disruptions, and enhances efficiency. Additionally, the clarity in reporting allows for better budgeting and financial forecasting, aiding in strategic planning.
This approach not only keeps operations smooth but also contributes positively to the company's bottom line.
Choosing the Right Software for Your Organization
Choosing the right equipment inspection software is critical for organizations aiming to enhance their operational efficiency and compliance. This decision significantly impacts how effectively inspections are managed and reported. The correct software will cater to specific industry needs while also supporting the regulatory framework within which a business operates. In this section, we will delve into the essentials of recognizing business requirements, evaluating vendor options, and considering cost implications. Each of these elements is fundamental in determining how well a software solution aligns with organizational goals.
Identifying Business Needs
Before committing to any software, it is vital to carry out a comprehensive analysis of your organization’s unique needs. This process begins with an assessment of existing workflows and inspection protocols. Different industries have diverse regulatory requirements; thus, identifying these will aid in selecting a platform that is compliant.
Consider the following questions during this assessment:
- What types of equipment are commonly inspected within your organization?
- What are the specific regulations that need to be adhered to?
- How does your team currently manage inspections, and what are the inefficiencies?
Gathering input from various stakeholders within the company can provide a broader perspective on the needs. This may include technicians, safety officers, and IT personnel. The goal is to clearly outline the features that are non-negotiable for your operations and which aspects could be flexible.
Evaluating Vendor Options
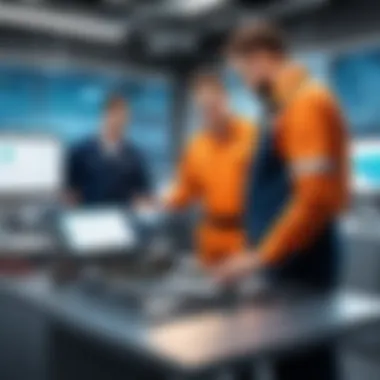
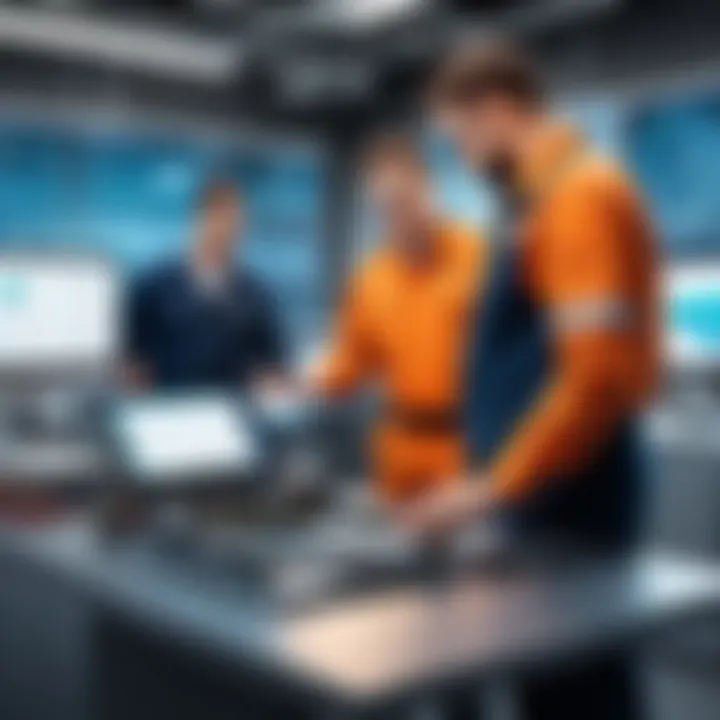
Once the business needs have been clearly defined, the next step is to evaluate potential vendors. It is essential to investigate the reputation and reliability of each vendor, which can significantly affect ongoing support and software updates. Key factors to consider include:
- User Reviews: Look at feedback from users in similar industries to see their experiences.
- Demo or Trial Options: Many vendors offer a trial period which can help in understanding usability and functionality.
- Integration Capabilities: Assess how well the software integrates with existing systems.
Vendor transparency around features, pricing, support, and training is crucial. A reliable vendor should provide detailed documentation and customer support. Establishing a good relationship with vendors can facilitate better service and quicker fixes when issues arise.
Cost Considerations
Cost is a significant factor in the decision-making process. It is not only about the initial purchase price but also includes ongoing operational expenses. While it may be tempting to opt for the cheapest solution, consider the long-term value.
Factors to account for include:
- Licensing Fees: Understand the cost structure, including subscription plans and any additional fees for upgrades.
- Training Costs: Factor in the budget for training staff on the new software, which can often require considerable time and resources.
- Maintenance and Support: Evaluate the costs associated with technical support and maintenance over time.
Integration with Existing Systems
In the realm of equipment inspection software, the capability to integrate seamlessly with existing systems is paramount. This not only facilitates a smoother transition for organizations adopting new software but also enhances overall efficiency and reduces the risk of operational disruption. Businesses depend on various tools to manage their operations, including inventory management, safety compliance, and maintenance scheduling. The ability for inspection software to synchronize with these platforms can lead to more accurate data and improved decision-making.
A strategic approach to assessing compatibility is critical. It is vital for businesses to evaluate how well the new inspection software can connect with their current systems. One should consider whether the software offers open APIs or customizable features, which can significantly influence integration capability. Additionally, ensuring that the data formats are compatible will prevent data loss or corruptions, leading to more trustworthy output.
Another area worth exploring is the benefits of such integrations. For example, when inspection software integrates with maintenance management systems, it enables automatic updates and alerts concerning equipment status. This proactive measure can help in planning maintenance activities before an issue arises, thereby reducing downtime.
Assessing Compatibility
Assessing compatibility involves a thorough analysis of both technical and functional aspects. Organizations should start by mapping out the software ecosystem currently in place. This includes identifying existing software solutions and the data workflows within those systems. Key considerations during this assessment should include:
- Data Structure: Understand the type of data your existing systems handle. Ensure that the new software can accommodate similar data formats.
- User Access Levels: Determine if the inspection software supports similar user roles and permissions to maintain security protocols.
- System Architecture: Evaluate whether the current infrastructure can support additional software without significant upgrades or investments.
A recommended practice is to conduct preliminary testing through sandbox environments. This allows for a practical understanding of interactions without affecting critical operations.
Implementation Strategies
Once the compatibility is assured, the next step involves strategic implementation. This phase should be methodically planned to reduce risks and improve the likelihood of successful adoption. A few vital strategies include:
- Phased Rollout: Introduce the software in phases rather than adopting it all at once. Start with a pilot program in one department to gather feedback and make necessary adjustments.
- Training and Support: Ensure that all team members are adequately trained on the new software. Provide ongoing support to address any concerns or technical difficulties that may arise.
- Iterative Feedback Loops: Establish channels for continuous feedback throughout the implementation phase. This engagement can help identify any integration issues early in the process.
"An effective integration not only enhances operational efficiency, it also empowers teams to focus on their core tasks rather than managing software compatibility issues."
Challenges in Equipment Inspection Software Adoption
The implementation of equipment inspection software can significantly improve operational efficiency and compliance. However, the adoption process is often fraught with challenges that organizations must navigate. Understanding these challenges is crucial for a successful transition. The most prominent issues typically arise from resistance to change and cost implications, both of which require careful consideration and strategic planning.
Resistance to Change
Organizations frequently face resistance to change when introducing new systems, including equipment inspection software. Employees may feel apprehensive about adapting to new technology, fearing that it will disrupt their established routines. This resistance can stem from a variety of factors such as:
- Lack of Training: Insufficient training can lead to discomfort with new software. Without proper guidance, employees may worry about their ability to use the tool effectively.
- Fear of Job Loss: Automation can trigger fears among workers regarding their job security. They might believe that implementing this technology could render their roles obsolete.
- Cultural Factors: Organizational culture plays a significant role in the acceptance of new technologies. A culture that values tradition over modern practices may struggle to embrace equipment inspection software.
Addressing these concerns is essential for fostering an environment that encourages acceptance of new technologies. Providing comprehensive training and communicating the benefits clearly can mitigate resistance. Explaining how the software enhances efficiency and accuracy can reassure employees that it is a tool for empowerment, not replacement.
Cost Implications
Cost considerations are another prominent hurdle in the adoption of equipment inspection software. Organizations must evaluate both the initial investment and ongoing costs. Key factors to consider include:
- Licensing Fees: Costs can vary widely based on the vendor and specific features provided. It's crucial to understand the pricing structure.
- Implementation Costs: Beyond the purchase of software, whether there are hidden costs such as integration with existing systems or infrastructure upgrades should be assessed.
- Training and Support: The long-term costs of training employees and ongoing support also need to be included in the budget. A lack of support can lead to additional costs as organizations spend time resolving issues.
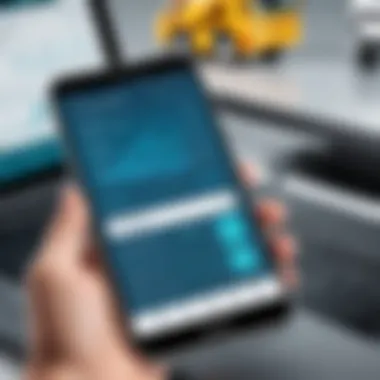
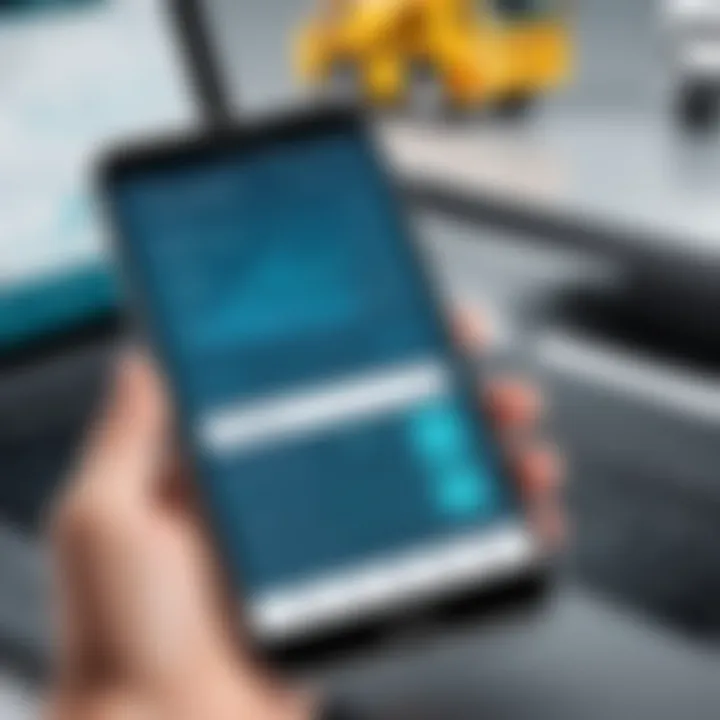
To effectively manage these costs, organizations should conduct a thorough cost-benefit analysis. This should take into account not just the financial expenditure but also the potential savings and efficiencies gained from the software.
"Investing in equipment inspection software can yield substantial returns over time, but organizations must navigate potential barriers to realize these benefits."
Future Trends in Equipment Inspection Software
The landscape of equipment inspection software is rapidly evolving. Staying abreast of future trends is crucial for organizations aiming to enhance their operational efficiency and compliance standards. Understanding these trends enables businesses to leverage new technologies and methodologies that improve the efficacy of their inspection processes. This section delves into two key areas poised to significantly influence the future of equipment inspection software: the integration of AI and automation, and the utilization of remote inspection technologies.
Integration of AI and Automation
Artificial intelligence (AI) is becoming increasingly integrated into equipment inspection software. AI technologies can analyze vast amounts of data quickly, allowing for more informed decisions regarding equipment health and maintenance. These systems can spot patterns and predict potential failures before they occur. This predictive maintenance is a game changer. It reduces downtime and lowers maintenance costs. Companies leveraging AI benefit from increased safety, as potential hazards can be identified and addressed in advance.
Automation also plays a pivotal role. By automating routine inspection tasks, organizations can free up personnel to focus on more complex issues requiring human judgment. Automated reporting and documentation enhance accuracy and compliance. Furthermore, AI-powered systems often utilize machine learning to improve over time, adapting to specific business workflows and regulatory requirements. Thus, companies that embrace AI and automation position themselves strategically for an efficient future.
"The integration of AI into equipment inspection software leads to unparalleled efficiency and foresight in maintenance processes."
Remote Inspection Technologies
Remote inspection technologies are redefining how inspections are conducted. These systems enable inspectors to examine equipment using drones, cameras, and other sensors from a distance. This capability is especially relevant for equipment located in hard-to-reach places. Remote inspections can enhance safety by reducing the need for personnel to enter hazardous environments.
Moreover, remote inspection technologies facilitate real-time data collection and analysis. This immediacy allows businesses to react promptly to any issues identified during the inspection. Remote technologies can also support collaboration among teams by enabling experts to participate in inspections from various locations without the need for physical presence.
As a result, organizations can save time and resources while ensuring that inspections meet necessary standards, ultimately leading to more compliant and efficient operations.
Case Studies and User Experiences
Understanding how equipment inspection software has been applied in real-world scenarios is essential for grasping its full potential. Case studies and user experiences provide concrete examples of the software in action, illustrating both the benefits and challenges faced by organizations that have implemented such solutions. These narrative-driven insights help prospective users envision how the software could be utilized in their specific contexts and the tangible impacts it might yield.
Through these detailed case studies, businesses can make informed decisions based on actual performance data, rather than theoretical promises. They reveal how various industries leverage this technology to enhance safety, compliance, and operational efficiency. Furthermore, user experiences detail the practical aspects of using different software options, from implementation challenges to ongoing benefits.
Success Stories
Success stories are pivotal in showcasing the effectiveness of equipment inspection software. One notable example comes from a manufacturing company that integrated iAuditor into their operations. This application allowed field inspectors to digitize their reports and develop a centralized database for inspection data. The immediate reduction in paperwork not only enhanced compliance with safety regulations but also empowered managers to access real-time data for decision-making.
Another compelling case is that of SafetyCulture. A construction firm using their software reported a significant decrease in on-site accidents due to better tracking of equipment safety checks. The visual tools and automated reminders embedded in the software ensured that all equipment was regularly inspected and properly maintained. As a result, the company enjoyed fewer disruptions, translating into reduced operational costs and increased productivity.
Lessons Learned
While many experiences highlight the advantages of using equipment inspection software, they also shed light on key lessons learned throughout the implementation process. A common lesson among different organizations is the necessity for comprehensive training. Employees who do not fully understand the features and capabilities of the software can underutilize it, negating potential benefits. For instance, an engineering firm that rushed its deployment faced issues in data accuracy due to lack of proper user training.
Moreover, balancing software capabilities with user needs is critical. Some companies discovered that selecting software with too many features often led to user frustration, as employees felt overwhelmed. This points to the importance of careful selection to align the software’s functionalities with the organization's specific requirements.
In summary, case studies and user experiences illustrate the practical implications of equipment inspection software. They offer invaluable lessons and successes that can guide organizations in their quest for improved safety and efficiency. By examining these narratives, stakeholders gain clarity on the capabilities of the software and understand how its effective use translates into meaningful operational improvements.
Finale
In the context of this article, the conclusion plays a crucial role in encapsulating the insights gleaned throughout the comprehensive examination of equipment inspection software. It serves to bring together the various threads of discussion into an understandable summary while underscoring the relevance of the topic to the audience. By reflecting on key points, stakeholders can re-evaluate their approach to equipment inspection and the technologies that support it.
The importance of equipment inspection software cannot be overstated, considering its potential to dramatically enhance operational efficiency. Stakeholders in various industries are increasingly relying on such tools to meet regulatory compliance and optimize risk management strategies. As the business landscape continues to evolve, understanding the capabilities and benefits of this software becomes necessary. Leveraging the right inspection software effectively transforms how organizations approach maintenance and ensures they remain competitive within their respective markets.
Summarizing Key Points
- Functionality and Benefits: Equipment inspection software improves efficiency, compliance, and risk management. These factors play a fundamental role in ensuring that an organization operates not only effectively but also safely.
- Critical Features: Key features such as user interface, mobile access, data collection, and reporting are essential for maximizing the utility of the software. Each element contributes to user experience and operational performance.
- Integration Challenges: Potential challenges faced by B2B stakeholders, including the resistance to change and cost implications, must be acknowledged. Addressing these challenges is pivotal for a smooth software adoption.
- Future Trends: Trends such as AI integration and remote inspection technologies highlight the growing intelligence of inspection tools. Recognizing these trends helps stakeholders plan for future advancements.
Final Recommendations
In concluding this guide, several final recommendations may enhance decision-making when adopting equipment inspection software.
- Thorough Needs Assessment: Organizations should perform a comprehensive analysis of their business needs prior to selecting software. Identifying specific requirements will help in choosing the most appropriate tool.
- Vendor Evaluation: Engaging in a rigorous evaluation process of potential vendors is instrumental. Factors to consider include reputation, existing client feedback, and support capabilities.
- Budget Considerations: Budgeting should reflect both short-term and long-term perspectives. While initial costs might be significant, the long-term savings associated with improved efficiency could warrant the investment.
"An informed choice about equipment inspection software is crucial for maximizing operational potential and enhancing compliance."
By staying informed on current offerings and market trends, organizations can make empowered decisions that greatly benefit their operations moving forward.