Mastering the ABC System of Inventory Management
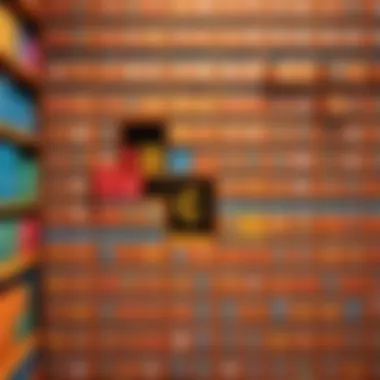

Intro
Inventory management remains a critical component of any business operation. Among the various systems available, the ABC inventory management system stands out due to its structured approach.
This method segments inventory into three distinct categoriesβA, B, and Cβbased on their importance to the business. Items classified as 'A' are the most valuable, 'B' items hold moderate value, and 'C' items are the least significant in terms of revenue or usage.
By categorizing inventory in this way, businesses can more effectively allocate resources and monitoring efforts to manage stock levels aligned with their financial performance and operational needs. This guide aims to provide an in-depth look at the ABC system, including its key features, implementation strategies, advantages and disadvantages, and best practices for its application in B2B settings.
Understanding the ABC System
The ABC system of inventory management is a pivotal approach that significantly enhances how businesses manage their inventory. It allows organizations to assess and categorize their inventory based on various factors, such as value and usage frequency. The significance of understanding this system lies in its potential to streamline operations, thereby promoting cost optimization and improved service delivery.
Definition and Key Principles
The ABC system divides inventory into three categories: Class A, Class B, and Class C. Class A items represent the most critical inventory, typically comprising a small percentage of total items but accounting for a substantial portion of inventory value. Class B items are of moderate importance, and Class C items are low-value items that require less stringent control.
This classification relies on the Pareto principle, often referred to as the 80/20 rule. According to this rule, approximately 80% of outcomes come from 20% of causes. In the context of inventory, this indicates that a small number of high-value items can represent the majority of overall inventory value. Recognizing these patterns helps businesses tailor their inventory management strategies effectively.
Historical Context
The ABC system of inventory management evolved in the early 20th century alongside the rise of manufacturing and business processes. Originally rooted in production control, it became increasingly relevant as businesses looked for efficient management strategies. As companies expanded, traditional methods of inventory management could not keep pace with the complexity and variety of inventory they handled.
The introduction of the ABC system offered a structured methodology to categorize inventory, leading to better decision-making and resource allocation. Over time, various industries adopted this approach, recognizing its value in enhancing inventory control. Today, modern logistics and inventory management software incorporate the ABC system, making it easier for businesses to manage their resources effectively.
"The ABC system offers an optimal strategy for inventory management by allowing organizations to focus on critical inventory items, leading to more effective resource utilization."
How the ABC Classification Works
Understanding how the ABC classification works is essential for optimizing inventory management. This method offers a systematic approach to prioritize inventory items based on their importance to overall business operations. The classification into three distinct categoriesβClass A, Class B, and Class Cβprovides insights into where to allocate resources and focus attention.
Criteria for Classification
The criteria used to classify inventory items into categories are fundamental to the success of the ABC system. Typically, the classification is based on factors like:
- Value: This includes both purchase cost and sales revenue associated with each item.
- Usage Frequency: How often an item is used or sold over a specific period.
- Lead Time: The time taken to replenish stock, which impacts how critical an item is to operations.
Items that contribute significantly to revenue, require frequent management attention, or are difficult to procure usually fall into the Class A category. Class B items are of moderate importance, while Class C items generally require less monitoring.
Categorization Process
The categorization process involves several steps to ensure an accurate classification of inventory items.
Class A Items
Class A items represent a small percentage of total inventory, but account for a large part of the total value. Typically, these items can be around 10-20% of the inventory but can contribute 70-80% of the value. The key characteristic of Class A items is their high significance, necessitating diligent control and frequent review.
- Unique Feature: They often require precise tracking, and businesses may perform regular audits to ensure they manage them effectively.
- Advantages: Proper management of Class A items can lead to substantial cost savings and performance improvements in inventory practices.
- Disadvantages: They may demand more time and resources for monitoring, which could strain operational efficiency if not handled correctly.
Class B Items
Class B items are moderate in both frequency and value. They typically comprise about 30% of inventory and contribute roughly 15-25% of overall value. Class B items require a balanced approach; they should not be overlooked but do not require the same level of attention as Class A items.
- Unique Feature: These items often have variable demand, which can make it challenging to manage them effectively.
- Advantages: Focusing on Class B items allows businesses to optimize resources without overwhelming their operations.
- Disadvantages: The potential for lost revenue exists if these items are not monitored adequately, as they can also impact customer satisfaction.
Class Items
Class C items represent the bulk of inventory but carry the least value, contributing approximately 5-10% of total inventory value. These items are typically low-cost items or items with infrequent sales. While they require less attention overall, that does not mean they can be neglected.
- Unique Feature: They are often managed with simplified methods, such as periodic audits instead of continuous monitoring.
- Advantages: This classification allows businesses to reduce resource allocation while ensuring that stock levels remain adequate for less critical items.
- Disadvantages: A lack of attention could result in stockouts or supply issues, impacting operations despite their lower value.
By comprehensively implementing the ABC classification process, businesses can realize significant improvements in inventory management. This optimization leads not only to precise control of stock but also enhances decision-making processes across the board.
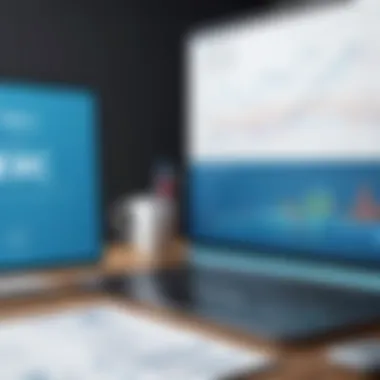

Benefits of the ABC System
The ABC system of inventory management plays a pivotal role in modern business practices. Its approach focuses on categorizing inventory items based on their value and criticality to the overall operation. By implementing this system, organizations can facilitate better resource allocation and enhance overall efficiency. Understanding these benefits is essential for businesses that aim to streamline their inventory processes while driving cost reductions and improving operational decisions.
Enhanced Inventory Control
One of the most significant advantages of the ABC system is its ability to enhance inventory control. By segmenting inventory into class A, class B, and class C items, businesses can prioritize resources and attention on the most impactful items. Class A items typically represent a small percentage of total inventory but account for a large portion of the value. Focusing on these critical items ensures optimal stock levels and minimizes the risk of stockouts.
The categorization allows for tailored management strategies for each class. For example, class A items might be monitored more closely using advanced tracking methods. In contrast, class C items can have a more relaxed approach. This targeted monitoring reduces wasted efforts and aligns resources with demand patterns.
Cost Efficiency
Cost efficiency is another key benefit of the ABC system. By identifying which items require more investment and which do not, organizations can optimize their purchasing strategy. Managing inventory costs is crucial, and this system helps minimize holding costs associated with excess inventory. In fact, companies may realize significant savings by reducing inventory levels for lower-value items.
Implementing the ABC system can also lead to smarter cash flow management. Funds that would have been tied up in low-demand inventory can be released for more critical needs or investments. This allocation of resources aids in improving the company's financial stability.
Improved Decision Making
The data-driven approach of the ABC system leads to improved decision-making capabilities. With clear insights into inventory dynamics, decision-makers can focus on areas that directly impact the bottom line. Such insights enable businesses to identify trends related to sales and inventory depletion more promptly.
Moreover, stakeholders can use this classification to assess risk better. For instance, they can evaluate the implications of stock shortages for class A items versus class C items, allowing for proactive strategies in supply chain management. This understanding fosters informed decisions not only about inventory management but also about procurement, production planning, and overall business strategy.
The ABC system equips businesses with structured insights, leading to prioritized actions based on real value, ultimately enhancing operational outcomes.
Challenges of Implementing the ABC System
Implementing the ABC system of inventory management is not without its obstacles. Organizations may experience a variety of challenges that can impede the adoption process. Understanding these challenges is crucial for successful execution. Addressing them head-on can foster a smoother transition and enhance the overall effectiveness of inventory management.
Resistance to Change
One of the most significant challenges in implementing the ABC system is resistance to change. Employees accustomed to existing processes may view new systems with skepticism. Such resistance can arise from various sources, including fear of the unknown, lack of understanding, or questioning the necessity of change. To mitigate this resistance, organizations should prioritize informative communication regarding the benefits of the ABC system. Staff involvement in the decision-making process is also crucial. By engaging employees early, management can promote a sense of ownership over the new system. This helps build a culture where change is not only accepted but embraced.
Data Accuracy Requirements
The ABC inventory management system relies heavily on accurate data to function effectively. Without precise and timely information, categorization and subsequent decision-making become flawed. Data accuracy issues can stem from different factors such as inconsistent data entry practices, lack of training, or outdated systems. To overcome these challenges, businesses must establish clear data management protocols and invest in reliable software tools for inventory tracking and analysis. Continuous staff training ensures that everyone involved is aware of the importance of data integrity. Thus, companies can ensure their ABC system operates on a strong foundation of accurate information.
"An effective implementation of the ABC system hinges on overcoming two primary challenges: resistance to change and data accuracy requirements. Tackling these issues is essential for maximizing the system's benefits."
Steps for Implementation
Implementing the ABC system of inventory management is a crucial step for businesses aiming to enhance their operational effectiveness. This segment will discuss the specific elements involved in successful implementation, along with the benefits and considerations that decision-makers should keep in mind. A systematic approach helps in aligning inventory management practices with organizational goals. It ensures the accuracy and reliability of the classifications, thus promoting better decision-making in inventory control.
Assessing Current Inventory Practices
Before adopting the ABC system, it is essential to evaluate existing inventory management practices. This assessment provides insights into current strengths and weaknesses. Companies should analyze how inventory is handled, stored, and tracked. Metrics such as turnover rates and carrying costs need closer examination. This can involve:
- Analyzing past sales data
- Identifying fast and slow-moving items
- Reviewing existing inventory turnover ratios
- Documenting current storage conditions and processes
By collecting this data, businesses can develop a clearer understanding of which items significantly impact their operations. This step is vital since it forms the foundation for effective categorization in the ABC system.
Choosing the Right Software Tools
Selecting adequate software tools is another critical step for implementation. An effective inventory management software should support the classification process and provide real-time visibility over inventory levels. Parameters to consider when choosing software include:
- User-friendly interface to ensure easy adoption by staff.
- Integration capabilities with existing systems, to avoid disruptions.
- Reporting features that can automate data analysis and inventory tracking.
- Scalability to accommodate future growth.
The right software can automate many of the time-consuming tasks associated with inventory management. This will free up resources for more strategic activities and enhance the overall effectiveness of the ABC inventory method.
Training Staff and Stakeholders
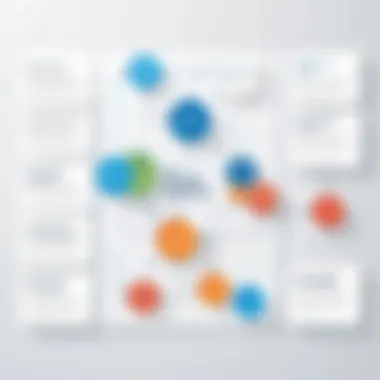

Training is often overlooked but is a vital element in implementing the ABC system effectively. Staff and other stakeholders should understand not only how to use the new system but also the rationale behind it. Training should cover:
- The principles of the ABC system: why categorization matters and its impact on the business.
- The usage of new software tools: hands-on practice and resource materials should be provided.
- Understanding classifications: ensuring everyone knows how to identify Class A, B, and C items maximizes effectiveness.
Regular follow-up training sessions can reinforce learning and help in addressing any issues that may arise during implementation. This commitment to staff education will significantly aid in minimizing resistance to change and ensure a smoother transition to the new system.
Proper implementation of the ABC system requires thorough planning and execution. A well-integrated strategy promotes efficiency and minimizes risks associated with inventory management.
Measuring Success of the ABC System
Measuring the success of the ABC system is crucial for determining the efficiency and effectiveness of inventory management practices within an organization. By evaluating specific performance indicators, businesses can gain insights into how well the ABC system is functioning and identify areas for improvement.
Quantifying success often depends on the data collected and analyzed through key performance indicators (KPIs). These metrics assist in understanding inventory flow, cost implications, and overall profitability. Recognizing and using these indicators also connects to strategic objectives and long-term efficiency goals.
KPIs for Inventory Management
Key Performance Indicators (KPIs) provide a clear and quantifiable means to monitor inventory management effectiveness, specifically in an ABC framework. Among the most essential are the Inventory Turnover Rate and Carrying Cost of Inventory, both pivotal in maintaining a healthy inventory.
Inventory Turnover Rate
The Inventory Turnover Rate measures how frequently inventory is sold or used over a specified period. A higher turnover rate signifies efficient inventory management and response to market demand. This metric is essential for identifying trends and can signal when to reorder stock to avoid shortages.
This rate has a clear characteristic: it reflects the agility of the supply chain and how well a company can adapt to changing consumer preferences. For businesses looking to optimize inventory, this is a beneficial metric to track, particularly in industries where demand can fluctuate significantly.
The unique feature of this rate lies in its benchmarking nature. By comparing the turnover rate against industry averages, a company can assess its performance relative to competitors. While a high turnover rate is advantageous, it can also carry disadvantages if it indicates insufficient stock levels, risking missed sales.
Carrying Cost of Inventory
The Carrying Cost of Inventory represents the total cost incurred by holding inventory over time. This cost includes storage fees, insurance, depreciation, and opportunity costs of cash tied up in unsold products. Understanding this cost is vital for controlling expenses and improving profitability.
A key characteristic of carrying cost is its ability to reveal inefficiencies in inventory management. High carrying costs can impact overall profitability, making it important for companies to minimize these expenses. This metric is beneficial as it encourages organizations to analyze their inventory levels and adjust procurement policies accordingly.
The unique aspect of carrying costs is that they can serve as a warning signal for overstock situations. If carrying costs are disproportionately high, it suggests that excess inventory may not be moving as expected, leading to wasted resources. Organizations must weigh the advantages of having a safety stock against the implications of increased carrying costs.
Continuous Improvement Strategies
Implementing continuous improvement strategies is essential for maintaining and enhancing the efficiency of the ABC system. Organizations should regularly review performance metrics and adapt strategies based on findings. This might involve reassessing classification criteria or technology upgrades to support inventory management. Regular staff training and process evaluations can ensure that the system evolves with changing market conditions. By embedding a culture of continuous improvement, organizations maximize their potential for success in inventory management.
Software Tools and Resources
The efficiency of the ABC system of inventory management greatly relies on the software tools and resources utilized in its implementation. The right software can enhance the classification, tracking, and reporting of inventory items, making the management process less labor-intensive and more accurate. Businesses must weigh various factors such as functionality, user-friendliness, and integration capabilities when selecting software.
Top Software Options for ABC Inventory Management
In the landscape of inventory management, several software options stand out for their features tailored to the ABC system. Understanding the nuances of each can help a company make an informed choice.
Here are some notable options:
- Fishbowl Inventory: This software provides robust features for inventory tracking and reporting. Its compatibility with various accounting packages makes it a preferred choice for many.
- TradeGecko: Known for its user-friendly interface, TradeGecko offers strong inventory management capabilities suitable for e-commerce businesses. It simplifies order management and has good reporting features.
- Zoho Inventory: As part of the Zoho suite, this tool is particularly attractive for small to medium enterprises. It allows businesses to manage inventory, orders, and shipping seamlessly.
- NetSuite: A more comprehensive ERP solution, NetSuite is powerful but may require a steeper learning curve. It is suitable for larger organizations looking for integrated tools.
Evaluating these options, a business should consider not just the features, but also whether the software can adapt to the unique needs of their ABC classification.
Integration with Existing Systems
Integrating ABC inventory management software with existing business systems is crucial to maximize efficiency. Successful integration can streamline operations, reduce data entry errors, and provide a unified view of inventory across different platforms.
Common considerations during this phase include:
- Compatibility: Ensure that the software selected can work alongside current systems. This may involve checking APIs and data exchange capabilities.
- Training: Staff may need training to adapt to the new system, particularly if it integrates advanced features not previously utilized.
- Cost Implications: Integration can incur additional costs. Companies should evaluate both immediate expenses and long-term savings.
Proper integration helps protect investments in technology and makes full use of the efficiencies that the ABC system can offer. Overall, the careful selection and integration of software tools not only enhances inventory management but also contributes to better operational health in a business.
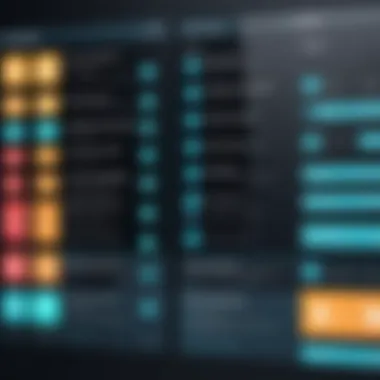

Case Studies of Successful Implementation
Understanding how various organizations apply the ABC system can provide valuable insights into its effectiveness. Case studies of successful implementation highlight practical applications and outcomes. By analyzing different sectors, we can identify best practices, challenges overcome, and how the ABC system enhances inventory management efficiency. These case studies serve as powerful examples, showcasing the adaptability and benefits of the ABC system in diverse contexts, thus encouraging other businesses to explore its potential.
Case Study: Manufacturing Industry
In the manufacturing sector, the ABC system has been a game-changer in managing complex inventories. A notable example is a leading automotive supplier that adopted the ABC classification to streamline its materials management process. The company faced challenges such as prolonged lead times and excess inventory costs, prompting its decision to implement the ABC system.
By categorizing components into Classes A, B, and C based on their value and usage frequency, the company focused on Class A items, which represented a small percentage of the inventory but were critical to production. This classification enabled the company to reduce stock levels, minimize storage costs, and improve order accuracy. Moreover, with detailed tracking of Class A items, they effectively managed reordering processes.
The results were significant. The automotive supplier reported a 30% reduction in carrying costs and a 40% decrease in stockouts, leading to improved production flow and enhanced customer satisfaction. Ultimately, the adoption of the ABC system transformed their operations, resulting in a more efficient inventory management process.
Case Study: Retail Sector
In the retail sector, a prominent fashion retailer illustrates how the ABC system can optimize inventory visibility and control. This company faced challenges with seasonality and fluctuating demand, leading to overstock situations and markdowns. To combat this, they implemented the ABC classification method.
Initially, the retailer categorized its product lines into Classes A, B, and C, focusing on high-turnover items in Class A. These items accounted for significant sales revenue and therefore required closer monitoring. The retailer employed a sophisticated software tool to regularly update classifications based on sales data. This dynamic approach ensured that inventory levels were adjusted in real time, based on market demand.
The successful application of the ABC system in both manufacturing and retail sectors emphasizes its versatility and effectiveness in inventory management.
Future Trends in Inventory Management
The landscape of inventory management is undergoing significant changes driven by technological advancements and evolving business practices. Understanding these future trends is crucial for organizations aiming to maintain a competitive edge. Businesses must adapt to these changes to streamline operations and improve their inventory management processes. Below, we explore technological advancements and shifts in business practices that are shaping the future of inventory management.
Technological Advancements
Technology plays a central role in modernizing inventory management. The rise of advanced tools and methods enhances accuracy and efficiency. Automation and artificial intelligence are at the forefront of these changes. Implementing automated systems allows businesses to reduce manual errors and save time. For instance, AI algorithms can analyze historical data to predict inventory levels more accurately, which reduces the chances of overstocking or stockouts.
Key advancements include:
- Internet of Things (IoT): This technology allows for real-time tracking of inventory items. Sensors can give locations and conditions of stored items, informing businesses about potential issues before they arise.
- Machine Learning: Algorithms can improve inventory forecasting, learning from patterns and trends to refine stock levels continuously.
- Cloud-Based Systems: These platforms offer centralized management of inventory data, promoting collaboration among teams and facilitating real-time updates.
These tools not only improve operational efficiency but also enable businesses to respond swiftly to market changes, enhancing overall agility. The implementation of these technologies does require an upfront investment and training, but the long-term benefits are undeniable.
Shifts in Business Practices
As businesses navigate the future, their inventory management practices are also evolving. Organizations are shifting towards more holistic approaches that prioritize sustainability and customer-centric strategies. Inventory management is no longer viewed in isolation; it's integrated into broader supply chain management and overall business strategy.
Important shifts include:
- Sustainability Focus: Businesses are becoming more aware of their environmental impact. Sustainable inventory practices may include minimizing waste, optimizing supply chains to reduce carbon footprints, and employing ethical sourcing.
- Lean Inventory Techniques: The adoption of lean practices helps businesses keep inventory levels aligned with actual demand. This not only cuts costs but also improves customer satisfaction by reducing lead times.
- Collaboration Across Departments: Increasingly, inventory management is a shared responsibility across departments. Sales, marketing, and logistics teams are working together to ensure that inventory decisions align with customer needs and business goals.
The integration of sustainable practices and departmental collaboration signifies a pivotal change in how businesses manage their inventory.
Organizations must remain adaptable and forward-thinking in the face of these trends. The future of inventory management will not just rely on technology but will also hinge on a companyβs ability to respond to shifting demands and concerns of its stakeholders.
Epilogue
The conclusion of this article emphasizes the significance of the ABC system in modern inventory management. Understanding the ABC classification is crucial for organizations looking to optimize their inventory practices. This system encourages businesses to prioritize their inventory items based on value and usage, making it more efficient than traditional methods.
Summary of Key Points
In this article, we have explored several key elements of the ABC system:
- Definition and Importance: The ABC classification groups inventory into three classes, allowing businesses to focus on high-value items.
- Implementation Steps: We discussed assessing current inventory practices and choosing suitable software tools to support the ABC system.
- Benefits: Enhancements in inventory control and cost efficiency can lead to better decision-making within organizations using this management system.
- Challenges: Resistance to change and the need for accurate data are obstacles that companies must navigate for successful implementation.
- Future Trends: The role of technology in enhancing inventory management practices is becoming increasingly vital.
The ABC system provides a structured approach to inventory management. It enables firms to allocate resources more effectively, thus contributing to operational success.
Final Thoughts on Implementing the ABC System
Implementing the ABC system requires careful planning, commitment, and an understanding of organizational needs. Businesses must recognize that each step in the process is critical for long-term success. Training staff effectively is important. Resistance from employees can hinder progress.
Furthermore, businesses should remain flexible, allowing room for adjustments as necessary. Collecting data continuously is encouraging for refining processes and improving efficiency.
Ultimately, by leveraging the ABC system, organizations can streamline their inventory management, adapt to changing market conditions, and ensure sustainability in their operations.