Understanding ShipStation Pick Lists: A Comprehensive Guide
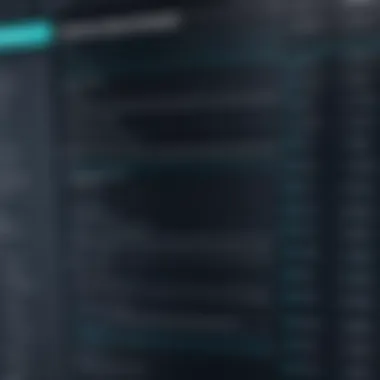
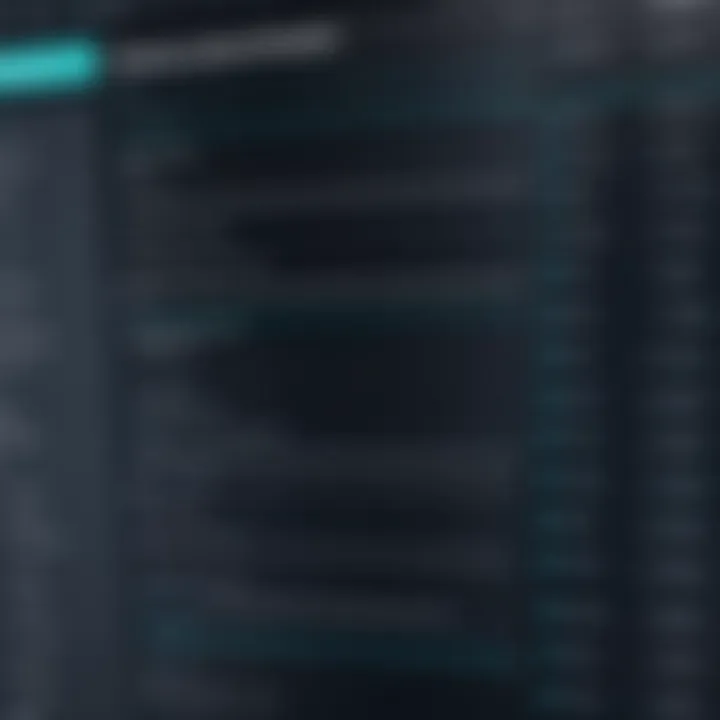
Intro
In the world of e-commerce, efficiency is paramount. Businesses are constantly seeking ways to optimize their order fulfillment processes. Here, ShipStation pick lists emerge as a significant solution to enhance productivity. They serve as an essential tool for managing inventory and streamlining operations, thereby helping businesses meet customer expectations more effectively.
This guide aims to delve into the mechanics of ShipStation pick lists, offering a comprehensive understanding of their functionality, implementation practices, and benefits. From traditional methods of picking to modern streamlined processes, we explore how ShipStation facilitates a transition that is both practical and beneficial for todayβs logistics demands.
Understanding the role of pick lists can transform the way teams operate. They provide clarity and organization in the fast-paced environment of inventory management. Decision-makers, business owners, and IT professionals can leverage this knowledge to inform their strategies and optimize order processing workflows.
As we navigate through this article, we will cover key features of ShipStation's pick lists, a pricing structure that informs fiscal considerations, and ultimately, the impact these tools have on operational success.
By the end, stakeholders will have a comprehensive view that enhances their understanding of ShipStation pick lists and their relevance in the current shipping landscape.
Preamble to ShipStation and Its Significance in Shipping
ShipStation has emerged as a cornerstone in the modern landscape of e-commerce and logistics. Understanding this platform's capabilities is essential for any business engaged in order fulfillment. The significance of ShipStation can be traced through its ability to streamline shipping processes, optimize workflows, and integrate seamlessly with various e-commerce platforms.
Overview of ShipStation
ShipStation is a robust shipping software solution designed to help businesses manage their shipping operations efficiently. It offers a suite of tools that facilitate label creation, order management, and inventory control. By connecting with multiple carriers, users can compare shipping rates, track shipments, and generate reports to analyze performance. The key advantage of ShipStation lies in its versatility. Whether a small online shop or a large retail operation, ShipStation can adapt to varying needs, providing tailored solutions that support growth and scalability.
The platform is user-friendly, allowing even those who are not tech-savvy to navigate through its features with relative ease. Furthermore, its cloud-based nature allows for real-time updates and accessibility from anywhere, promoting collaborative efforts among team members involved in shipping.
The Role of Pick Lists in Shipping Solutions
Pick lists are integral to the order fulfillment process, functioning as crucial tools that guide warehouse staff in efficiently gathering products for shipment. They provide clear instructions on the items that need to be picked for each order, reducing the likelihood of errors associated with manual picking methods.
The implementation of pick lists within ShipStation enhances operational efficiency in several ways:
- Organization: Pick lists help organize the picking process, enabling staff to complete tasks in a systematic manner.
- Time Efficiency: By clearly listing items, the time taken to locate products is significantly reduced, thus hastening the fulfillment process.
- Accuracy: The more structured approach to picking minimizes mistakes, which can lead to returns and customer dissatisfaction.
"In efficient shipping, time is not just money; it is a critical factor that can influence customer satisfaction."
In summary, understanding ShipStation and its functionality is vital for optimizing the shipping processes of businesses today. With tools like pick lists, organizations can enhance their operational efficiency, improve order accuracy, and ultimately provide a better experience for their customers.
Defining Pick Lists
Defining pick lists is essential to understand their role in enhancing order fulfillment processes, particularly when using ShipStation. Pick lists serve as structured guides for warehouse staff, outlining the items that need to be collected for each order. This improves accuracy and efficiency in shipping, a key factor for meeting customer expectations. As businesses move towards automated fulfillment, the definitions and types of pick lists enable stakeholders to choose the best approach for their specific needs.
What Is a Pick List?
A pick list is a detailed document that specifies which products must be gathered for shipment. It typically contains information like item names, quantities, and their respective locations within the warehouse. The primary purpose of a pick list is to streamline the picking process, allowing for orderly and efficient retrieval of items. For businesses utilizing ShipStation, generating pick lists means having accurate data that aligns with order requirements, significantly reducing the chances for errors.
Types of Pick Lists
There are several types of pick lists, each serving different purposes based on the operational needs of a business.
Single Order Pick List
A single order pick list is designed for processing an individual customer's request. It focuses on one order at a time, allowing staff to gather products without distraction from other tasks. This can be an effective method for smaller operations that process fewer orders. One key characteristic of single order pick lists is their simplicity; they ensure clarity and precision, minimizing confusion during the picking process. However, they may not be the most efficient option for high-volume environments, where gathering multiple orders simultaneously could save time.
Batch Pick List
Batch pick lists consolidate multiple orders into one list. This method allows warehouse staff to pick items for several orders at once, making it a popular choice for businesses with high order volumes. The major advantage of using batch pick lists is improved operational efficiency; staff can reduce travel time and process orders simultaneously. However, the downside is the potential for increased complexity, as staff must ensure that they correctly divide items among different orders. Mismanagement in this area could result in shipping errors.
Wave Pick List
Wave pick lists are a more advanced option, designed to optimize the work in a warehouse. They involve grouping orders based on specific criteria, such as shipping times or locations. This approach is useful for enhancing coordination among picking efforts. The key characteristic of wave pick lists is that they allow for strategic planning, making it easier for businesses to manage their workflow effectively. While they can increase productivity, wave pick lists also require a higher level of organization and could pose challenges in implementation if not managed properly.
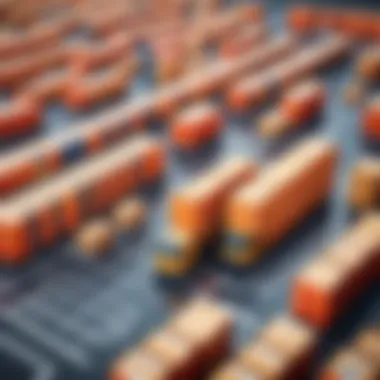
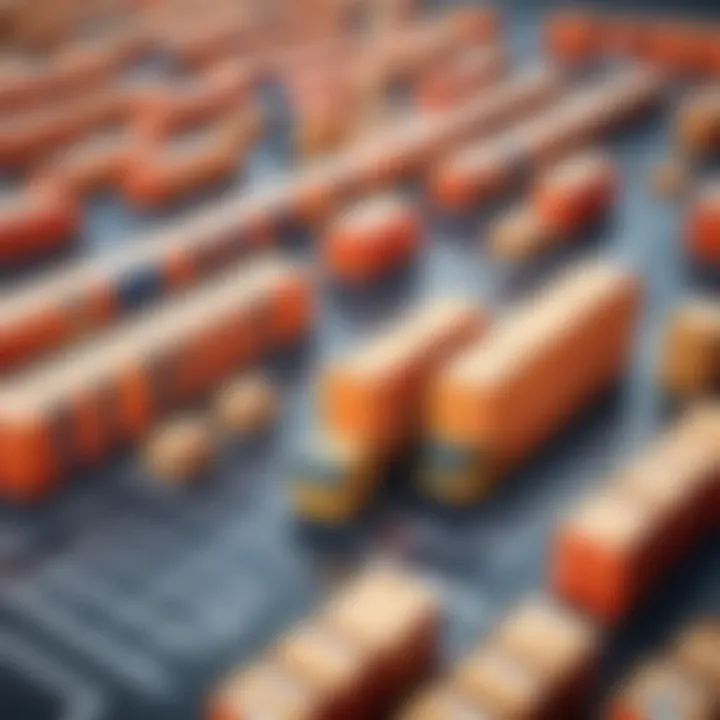
"Understanding the different types of pick lists enables businesses to refine their order fulfillment methods, leading to improved efficiency in shipping operations."
In summary, defining pick lists involves recognizing their importance within the context of modern order fulfillment strategies. Each type of pick list has unique features that can drastically affect a company's approach to shipping and logistics.
How ShipStation Generates Pick Lists
The process of generating pick lists within ShipStation is crucial for optimizing order fulfillment. It not only simplifies the picking process but also contributes to inventory management and overall operational efficiency. Understanding how ShipStation generates these lists provides valuable insights into leveraging the software for enhanced productivity.
Sources for Generating Pick Lists
ShipStation draws from various sources to create accurate pick lists. These sources primarily include:
- Incoming Orders: When customers place orders, ShipStation collects the relevant details such as item specifics, quantities, and shipping information. This initial data serves as a foundation for generating the pick list.
- Inventory Data: The software accesses current inventory levels in real-time, ensuring that the pick lists reflect what is available in stock. Accurate inventory information also helps in avoiding over-picking or backorders.
- Warehouse Locations: ShipStation takes into account the layout and organization of the warehouse. This includes the physical locations of items, allowing the generated pick list to optimize the order picking route, reducing time and effort.
- User Preferences: Users can customize their settings, adapting the pick list generation process to their workflow. This flexibility adds a layer of efficiency in how orders are handled.
These sources work together to produce a comprehensive and actionable pick list that aligns with a business's operational needs.
Automating Pick List Creation
Automation plays a significant role in the effectiveness of pick list creation within ShipStation. Here are some key aspects:
- Time Efficiency: Automating the generation of pick lists reduces the hours spent creating lists manually. This speeds up the process considerably, allowing staff to focus on order fulfillment rather than paperwork.
- Error Reduction: Manual processes are prone to human error. By automating pick list generation, ShipStation minimizes the risk of mistakes, ensuring that the correct items are picked every time. This capability enhances inventory accuracy and customer satisfaction.
- Integration with Other Systems: ShipStation can integrate with e-commerce platforms like Shopify or WooCommerce. This integration allows for seamless data transfer and automated updates, ensuring pick lists reflect the most current orders and inventory levels.
- Scalability: Automated systems can easily scale with business growth. As order volumes increase, automation allows for quicker adjustments and handling of larger datasets without compromising accuracy.
Navigating the ShipStation Interface
Navigating the ShipStation interface is a crucial aspect for users aiming to maximize their order fulfillment efficiency. The interface is designed to be user-friendly, allowing for quick access to essential features like pick lists. By understanding the layout and functionalities, users can significantly streamline their shipping processes.
User Dashboard Overview
The user dashboard in ShipStation serves as the central control panel for order management. Upon logging in, users are greeted with a layout that presents key metrics at a glance. This includes order volume, shipping status, and inventory levels. The dashboard can be customized to highlight specific data points relevant to user needs.
Several features stand out:
- Real-Time Updates: Orders are updated in real time, providing an accurate snapshot of current operations.
- Quick Links: Common tasks such as generating pick lists or accessing shipping reports are easily accessible from the dashboard.
- Notifications: Users can receive alerts about order status changes or shipping issues, ensuring timely responses to potential delays.
By making effective use of these dashboard features, users can enhance their operational productivity and reduce the time spent on routine tasks.
Accessing Pick List Features
Accessing pick list features is straightforward once users familiarize themselves with the interface. The pick list function is not only essential for optimizing picking processes but also enhances inventory management.
To access pick list features, follow these steps:
- Navigate to the Orders Tab: This section displays all orders ready for fulfillment.
- Select Pick Lists: Users can find the pick list option either on the sidebar or within the order management dropdown.
- Generate a Pick List: Users can create a pick list based on selected orders or filters such as shipping method or order priority.
Each pick list can be exported in various formats, allowing for smoother integration with existing workflows. By utilizing these features, businesses can minimize picking errors and improve overall efficiency in order processing.
Best Practices for Utilizing ShipStation Pick Lists
In the realm of order fulfillment, the effectiveness of pick lists can significantly dictate the speed and accuracy of operations. Best practices for utilizing ShipStation pick lists not only enhance workflow but also contribute to overall customer satisfaction. For businesses looking to streamline their shipping processes, understanding these practices is essential.
Organizing Inventory for Efficient Picking
Effective inventory organization serves as a cornerstone for optimizing the use of ShipStation pick lists. By systematically arranging products within the warehouse, companies can minimize the time and effort required during the picking process. Here are some key considerations for organizing inventory:
- Categorization: Group similar items together, whether by product type or order frequency. This prevents workers from searching through various sections for one item, thus saving valuable time.
- Labeling:Β Clear labels facilitate easier identification of products in the inventory. Utilize large, legible fonts and consider color coding to quickly direct staff to the appropriate locations.
- Inventory Location: Position high-demand items closer to packing areas. Items with lower turnover rates can be placed further away. This design choice can substantially reduce the distance staff must travel during order picking.
Ensuring that your inventory is organized not only aids in efficient picking, but it also enhances employee productivity.
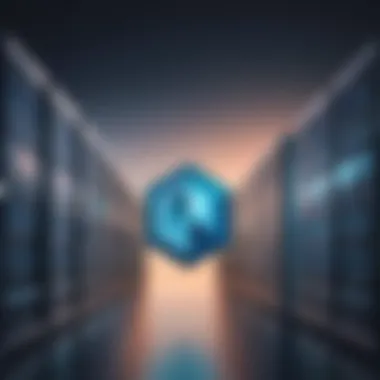
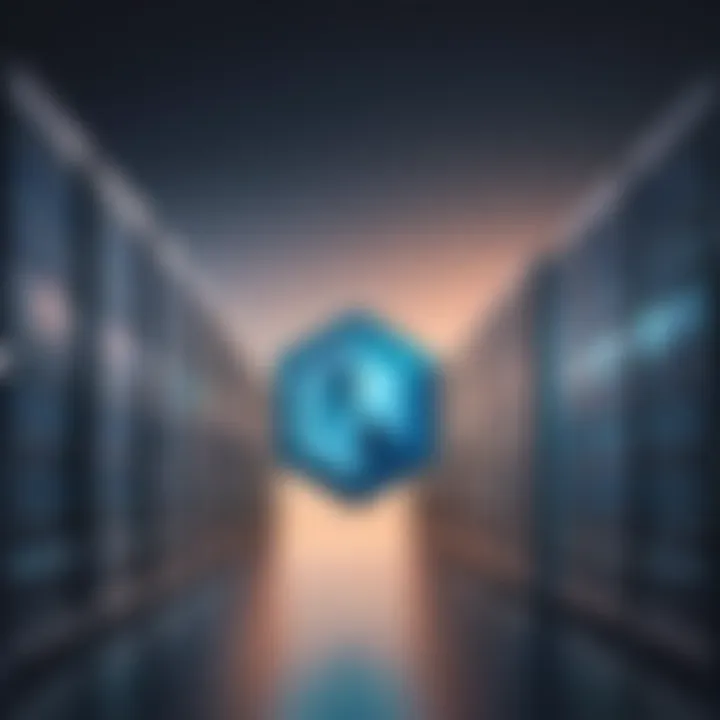
Using Barcodes for Accurate Picking
Leveraging barcodes is one of the most effective methods to increase picking accuracy. By integrating barcode technology with ShipStation, organizations can achieve near-perfect order fulfillment. Hereβs how barcodes contribute to this:
- Error Reduction: Scanning barcodes mitigates human error in picking. When an employee scans an item, the system verifies its accuracy against the pick list, prompting immediate corrective actions when discrepancies arise.
- Speed: Barcode scanners allow for rapid item verification, accelerating the picking process. Instead of manually checking items, employees can scan and move on, optimizing their workflows.
- Real-Time Updates: As items are picked, inventory levels can be updated instantly. This real-time data is invaluable for maintaining stock levels and informing future ordering decisions.
Implementing barcode systems is crucial for improving accuracy in order fulfillment. The combination of organized inventory with barcode technology creates an efficient picking environment, aligning with the goals of modern shipping logistics.
"Efficient fulfillment is not just about speedβit's about accuracy, organization, and leveraging technology to enhance performance."
Adopting these best practices can significantly elevate your operations on ShipStation, leading to greater customer satisfaction and better business outcomes.
The Benefits of ShipStation Pick Lists
ShipStation pick lists offer several important advantages in the realm of order fulfillment and inventory management. Their implementation can significantly streamline operations, reduce errors, and enhance overall productivity. Here, we will explore these benefits in detail, providing insights into how they can positively impact businesses.
Increased Operational Efficiency
Incorporating ShipStation pick lists into the workflow leads to a notable increase in operational efficiency. The automated generation of pick lists allows employees to quickly identify the items needed for each order, reducing the time it takes to locate products. This efficiency is crucial in fast-paced environments where meeting customer expectations is vital.
An organized pick list helps warehouse staff avoid unnecessary back-and-forth trips. Staff can follow a systematic route through the inventory, picking all items in a single pass. This minimization of movement saves time, allowing for faster order fulfillment. As a result, businesses can handle a larger volume of orders in the same timeframe, ultimately increasing throughput.
Reduction in Errors and Returns
Errors in order fulfillment can be costly. They lead to customer dissatisfaction and result in returns, which complicate logistics further. ShipStation pick lists help mitigate these issues by providing clear, structured information. Each list specifies which items to pick, including details like SKUs, quantities, and locations.
With visually organized and precise instructions, staff are less likely to make mistakes. The clarity of pick lists reduces the chances of selecting the wrong items. Moreover, utilizing barcodes during the picking process can enhance accuracy further. When items are scanned against the pick list, it acts as a confirmation step, helping to ensure that what is packed matches customer orders.
Enhanced Productivity Among Staff
Implementing ShipStation pick lists not only leads to efficiency and error reduction but also boosts staff productivity. When employees can follow a clear, digitized picking process, they can work more swiftly and confidently. This clarity promotes a satisfying work environment.
Additionally, with proper training on using pick lists and related tools, workers become more adept and skilled in their roles. The reduction in time spent looking for items and confirming orders allows staff to focus on value-added activities, such as quality control or customer service tasks. In essence, the structured approach provided by ShipStation fosters a more engaged and capable workforce.
"Leveraging pick lists is not just about organization; it's about creating a workflow that empowers your team to do their best work while satisfying customers reliably."
Comparing ShipStation Pick Lists to Traditional Methods
Understanding the contrasts between ShipStation pick lists and traditional picking methods is essential for businesses aiming to optimize their order fulfillment processes. While many companies have historically relied on manual methods of picking items for shipment, the recent advancements in technology have led to a paradigm shift in shipping logistics. This section delves into the conventional approaches and illustrates how modern pick lists provide numerous advantages that improve operational efficiency, reduce errors, and foster a more productive environment.
Traditional Picking Approach
Traditional picking methods usually involve the use of paper lists or spreadsheets. Employees physically navigate the warehouse, checking off items as they are gathered. This process can be inefficient for several reasons:
- Time Consumption: Staff members may waste significant time locating items, especially in larger warehouses. Each step can contribute to delays in fulfillment.
- Human Error: Since picking relies heavily on human accuracy, mistakes are common. An employee might misread an item or overlook it completely, leading to incorrect orders.
- Lack of Real-Time Data: When relying solely on manual processes, inventory counts can become outdated quickly. Subsequently, businesses may struggle to maintain accurate records.
The traditional approach may seem simple; however, it is often riddled with pitfalls that hinder productivity. As companies expand, these issues can compound, resulting in mounting frustration and inefficiencies.
Benefits of Modern Pick Lists
In contrast, ShipStationβs modern pick lists support a more systematic methodology. They leverage technology to enhance every aspect of the picking process:
- Increased Accuracy: Automated pick lists minimize the chances of human error. With digital confirmations, employees can quickly verify that they have selected the correct items before shipment.
- Faster Processing: ShipStation pick lists streamline workflows. Automated systems guide employees directly to items, reducing the time spent searching for products.
- Real-Time Tracking: Modern pick lists allow for instant updates to inventory systems. This means that stock levels are consistently accurate, enabling better decision-making in purchasing and inventory management.
- Data-Driven Insights: Businesses can analyze the efficiency of their picking processes. By collecting data on picking times and errors, organizations can make informed adjustments to further enhance productivity.
"The shift from traditional methods to modern solutions like ShipStation can profoundly impact operational efficiency, employee satisfaction, and customer fulfillment rates."
In combining the strengths of modern technology with established logistics frameworks, businesses can create an environment where efficiency thrives. Understanding these differences helps stakeholders appreciate the value that ShipStation pick lists bring to the fulfillment landscape. With the proper tools, companies can shift away from outdated practices, resulting in enhanced performance and a superior customer experience.
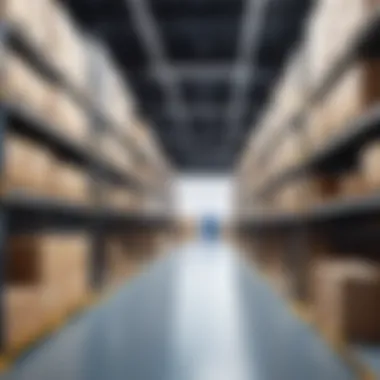
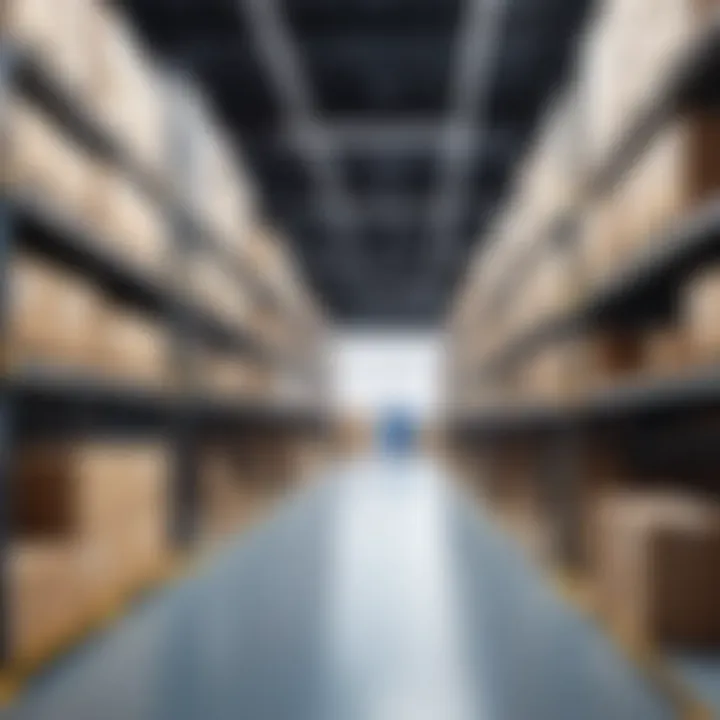
Common Challenges in Implementing Pick Lists
Implementing pick lists within ShipStation can enhance order fulfillment efficiency, but several challenges may arise during this process. Recognizing these challenges is crucial for businesses aiming to streamline their operations. This section explores common obstacles and provides insights into possible solutions, helping organizations make informed decisions against these barriers.
Technical Issues and Solutions
Technical problems can hinder the effective use of pick lists. Issues may arise during integration with existing systems or when using new software. Common challenges include API connection errors or unresponsive software. These can lead to frustrated staff and delays in order processing.
To mitigate these issues, companies can take multiple steps:
- Regular System Updates: Ensure that all software used is up-to-date, which can prevent bugs that arise from outdated technology.
- Dedicated IT Support: Having an IT team ready to troubleshoot problems can make a significant difference. They can quickly address technical issues and minimize downtime.
- Testing Before Full Launch: Conduct a pilot test of the pick list system before a full rollout to identify potential technical issues in real-time.
By proactively addressing technical issues, companies can improve the overall experience for users of ShipStation pick lists.
Employee Training and Adaptation
A significant challenge in implementing pick lists is ensuring that employees understand how to use the new system effectively. Resistance to change can stem from lack of familiarity with technology or fear of job security. Training is vital in alleviating these concerns and ensuring correct usage.
Key considerations include:
- Comprehensive Training Programs: Develop thorough training sessions that cover all different features of the ShipStation pick lists. Hands-on practice can deepen understanding and comfort.
- Ongoing Support: Offer continued support after the initial training. This can be in the form of Q&A sessions, helpdesk support, or refresher courses.
- Feedback Mechanisms: Create channels where employees can provide feedback about challenges they face while using the pick lists. This can provide insights into areas needing improvement.
The speed at which employees adapt to new pick list functionalities can heavily influence operational efficiency. Balancing technical functionality with effective training can lead to overall improvements in order fulfillment processes.
Future Trends in Shipping and Fulfillment
Understanding the future trends in shipping and fulfillment is crucial for businesses that want to stay competitive in the rapidly evolving e-commerce landscape. As customer demands continue to grow and technology advances, companies must adapt to these shifting dynamics. This section not only examines significant trends shaping the shipping and fulfillment sectors but also highlights their potential impact on systems like ShipStation pick lists.
One of the critical elements to consider is how advancements will redefine operational efficiencies. Greater automation means faster processing times and improved accuracy in handling orders. Businesses that embrace these trends can expect reductions in labor costs and error rates, leading to overall improved service levels.
Advancements in Automation
The narrative around automation is transforming. More companies are integrating automation tools in their warehouses and fulfillment centers to enhance productivity. Systems can now handle order picking, packing, and shipping with minimal human intervention. For instance, robotics used for picking items can navigate warehouses, retrieve products, and prepare them for shipment. This efficiency cannot be overstated as it dramatically reduces human error and accelerates order fulfillment cycles.
Moreover, ShipStation can integrate with these automated systems, allowing real-time updates and synchronization across platforms. Advanced automation can result in better inventory management, ensuring that stock levels are always accurate and available. The need for efficient pick lists becomes apparent as they are intricately linked to automated workflows.
The Growing Importance of Data Analytics
Data analytics is now at the forefront of determining shipping strategies. With vast streams of data now being generated by each aspect of the supply chain, companies that can harness this data will have a competitive advantage. Utilizing tools for data analysis, businesses can gain insights into customer behaviors, inventory turnover rates, and shipping times. These insights inform better decision-making processes and ensure that shipping practices align closely with consumer expectations.
Furthermore, improved data analytics within ShipStation allows for refining pick lists based on real-time inventory data. As trends develop, businesses can adjust their strategies proactively, ensuring they are aligned with emerging markets and demand fluctuations. Comprehensive understanding of consumer patterns will support companies in driving efficiencies while reducing waste.
"Incorporating advanced data analytics into shipping processes can ultimately lead to a more customer-centered fulfillment strategy."
To summarize, the future of shipping and fulfillment is undeniably linked to advancements in automation and the strategic use of data analytics. For businesses, particularly those utilizing systems like ShipStation, understanding these trends is essential. Leveraging these advancements not only enhances operational efficiency but also creates a more responsive and data-driven framework for meeting customer needs.
Closure
In this article, we reviewed various aspects of ShipStation and its pick list functionalities. The significance of these tools in modern shipping logistics cannot be overstated. As businesses face increasing pressure to improve operational efficiencies and reduce costs, understanding how to optimize picking processes becomes essential.
Recap of Key Points
The journey began with an overall introduction to ShipStation, highlighting its role as a transformative platform in shipping. We explored how pick lists serve as a backbone for effective order fulfillment, navigating the different types of lists such as single order, batch, and wave pick lists. The automation and interface features of ShipStation facilitate a smoother experience in generating and accessing these lists.
Moreover, best practices for inventory management and the advantages of employing pick lists were discussed. Enhanced productivity, efficiency, and a reduction in errors were underlined as prominent benefits of using ShipStation's features compared to traditional picking methods. We also addressed common challenges businesses might face during implementation and provided insights into future trends in the shipping industry.
Final Thoughts on ShipStation and Pick Lists
To summarize, ShipStation's pick lists are more than just a convenience; they are a critical element in achieving streamlined order fulfillment. The operational efficiency gained through their use can significantly impact a business's bottom line. Moreover, understanding the trends in automation and data analytics will arm decision-makers with knowledge to adapt strategies effectively.
As e-commerce continues to grow, the need for efficient shipping solutions like ShipStation is more pertinent than ever. Organizations that recognize the value of pick lists will not only improve their processes but also enhance customer satisfaction through timely and accurate deliveries.
"In a fast-paced market, precision in order fulfillment is key to maintaining competitiveness and customer loyalty."