Maintenance Control Systems: An In-Depth Guide
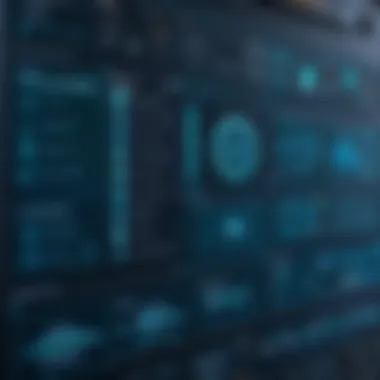
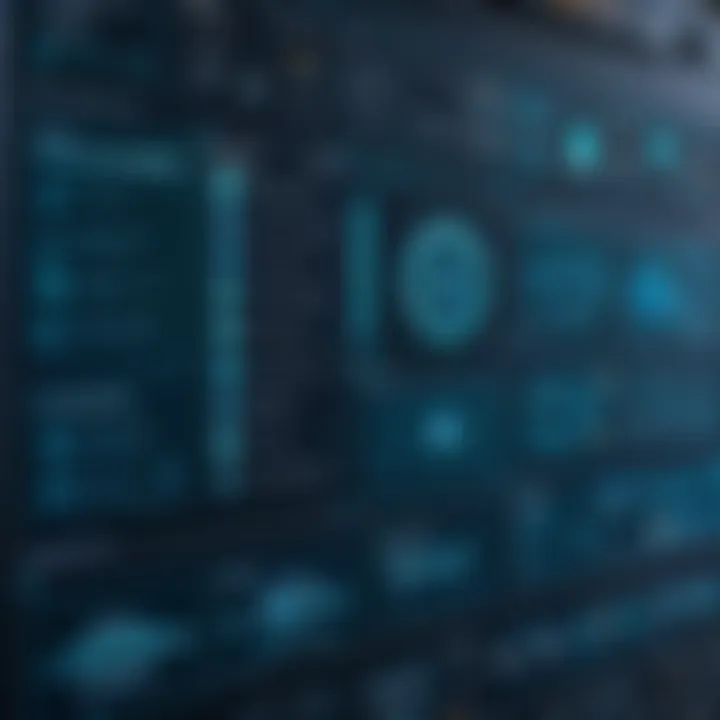
Intro
Understanding the mechanics behind maintenance control systems can sometimes feel like peeling an onion—layer after layer reveals insights that can be crucial for maximizing operational efficiency. Businesses today face the ongoing challenge of balancing cost-effectiveness with maintaining high performance. This is where robust maintenance control systems step in, offering a methodical approach that not only preserves assets but also enhances productivity across the board.
As we explore deeper into the subject, the discussion will circumnavigate the various types of maintenance strategies, from preventive to predictive. Each of these methodologies carries unique attributes that cater to specific operational needs, supporting the notion that there’s no one-size-fits-all solution in the realm of maintenance.
In a tech-heavy world, augmented by innovations like the Internet of Things (IoT) and big data analytics, understanding these systems is more crucial than ever for decision-makers in B2B contexts. Decision-makers armed with the right knowledge can make informed choices, ultimately contributing to a culture of proactive maintenance. This culture not only streamlines operations but fosters an environment where downtime becomes a relic of the past.
So, let’s embark on a voyage through the intricate world of maintenance control systems, picking apart their pivotal components, diving into operational methodologies, and pondering their broader impact on organizational efficiency. Whether you’re an IT professional, a business owner, or an executive looking to sharpen your competitive edge, there’s plenty here to chew on.
Key Features
Understanding the specific features of maintenance control systems can give organizations a significant leg up. They’re not just a collection of random tools but rather a cohesive set of elements designed to support and advance maintenance efforts.
Overview of Features
Common features that characterize these systems include:
- Asset Management: Keeping track of tools and equipment, their lifecycle, and performance metrics.
- Work Order Management: Streamlining requests for repairs or maintenance, creating a clear path from need to resolution.
- Inventory Control: Ensuring materials and parts are in stock when needed, minimizing delays.
- Reporting and Analytics: Offering insight into performance trends, usage, and repair histories.
- Integration Capabilities: Seamlessly working with other business software, improving overall efficiency.
These features can vary, tailored to the specific operational requirements of the organization, emphasizing the importance of customizing these systems to fit personal needs rather than trying to mold operations around a one-size-fits-all solution.
Unique Selling Points
At the core of successful maintenance control systems lie several distinct advantages:
- Increased Downtime Minimization: With smart scheduling and predictive analytics, disruptions can be anticipated and mitigated.
- Regulatory Compliance: Many sectors require adherence to strict maintenance guidelines; an effective system simplifies this process.
- Cost Savings: By optimizing resource allocation and extending asset longevity, these systems can pay for themselves over time.
These unique selling points culminate in a strong case for investing in dependable maintenance control systems.
Summary
As we dive deeper into the mechanics and applications of maintenance control systems in the following sections, we'll continue to peel back the layers, unveiling not just the nuts and bolts but also the broader implications for organizations. Your journey through this detailed exploration will equip you with the necessary insights to navigate and implement these systems more effectively in your organization.
Preface to Maintenance Control Systems
Understanding maintenance control systems is more than just academic curiosity; it's practically essential in today's fast-paced business environment. A maintenance control system lays the groundwork for how organizations ensure their operations run smoothly. It’s the backbone of reliability and efficiency, minimizing downtime while maximizing resource allocation. Whether you're managing a fleet, overseeing manufacturing equipment, or running a healthcare facility, maintenance control systems are your go-to framework for avoiding costly disruptions.
Definition and Purpose
At its core, a maintenance control system is a structured approach for managing maintenance tasks. It encompasses everything from scheduling routine checks to allocating resources effectively. The definition may be straightforward, but the impact is far-reaching. By using these systems, organizations can proactively address potential problems before they escalate into significant issues. Imagine a factory floor running like a well-oiled machine because machinery is regularly maintained without the operator even noticing; this is the very essence of effective maintenance management.
The purpose of these systems stretches beyond just keeping equipment operational. They foster a culture of accountability, ensuring that all necessary maintenance occurs on time. When employees know who’s responsible for what, it also boosts morale because everyone is on the same page. Furthermore, these systems provide crucial data that can be analyzed for trends, enabling informed decision-making. In essence, effective maintenance control systems serve as both preventative measures and strategic frameworks for organizational success.
Historical Development
The roots of maintenance control systems trace back decades, intertwining with various industrial revolutions as businesses sought efficiency. Initially, maintenance was reactive. Think of it as putting out fires instead of preventing them. The concept of scheduled maintenance, however, emerged as industries realized the cost associated with equipment downtime. From the manual logs of yesteryears, where workers scribbled down maintenance tasks, to today’s high-tech solutions powered by IoT sensors, the evolution is striking.
In the mid-20th century, companies began adopting more formalized maintenance processes. This transformation marked a shift toward preventive strategies, where maintenance tasks are scheduled based on time or usage rather than reacting to failure. Each subsequent decade saw technological improvements, such as computerized maintenance management systems, laying the foundation for today’s sophisticated tools. Organizations not only saved on costs but also improved safety, establishing maintenance as a critical function rather than a necessary evil.
The historical development highlights how essential these systems have become for operational integrity. Today's maintenance control systems can integrate seamlessly with other organizational processes, offering a holistic approach to resource management in various sectors, from manufacturing to healthcare.
As we delve into the types of maintenance control systems, we'll uncover their unique characteristics and what makes them suitable for different applications. The exploration into maintenance management is not merely an academic inquiry; it’s vital for fostering resilient and efficient operational environments.
Types of Maintenance Control Systems
Understanding the different types of maintenance control systems is essential for organizations looking to streamline their operations and boost efficiency. Each system comes with its unique methodology, strengths, and applications. Decision-makers need to recognize these distinctions to choose the most suitable approach based on their specific organizational needs. The right choice not only mitigates operational risks but also brings significant cost savings while enhancing overall productivity. This section delves into the three primary types of maintenance control systems: corrective, preventive, and predictive, each having its own role in the maintenance landscape.
Corrective Maintenance Systems
Corrective maintenance systems are fundamentally reactive. When a piece of equipment breaks down or shows signs of failure, these systems kick into action to address the problem. Think of it like waiting until your car makes a strange noise before you take it to the mechanic. While this approach may seem cost-effective in the short term, it can lead to more significant issues over time.
- Benefits:
- Considerations:
- Simplicity: Straightforward to implement, especially in smaller operations where resources are limited.
- Immediate Action: Responsive to crises, addressing failures as they occur.
- It can be a gamble; the resolve can be too late. Organizations risk incurring costly downtime and repairs if maintenance is only addressed after issues escalate. This inconsistency may also lead to a lack of trust in machinery performance, impacting employee morale.
Preventive Maintenance Systems
Preventive maintenance systems are the proactive approach to handling equipment care. Much like getting regular check-ups at the doctor, these systems allow for scheduled maintenance before issues arise. This method is about anticipating potential problems and addressing them before failures can disrupt operations.
- Benefits:
- Considerations:
- Reduced Downtime: Regular maintenance helps to minimize unexpected breakdowns. Organizations can plan maintenance during off-hours to avoid significant operational disruptions.
- Cost-Effectiveness: Better long-term savings can be achieved by addressing issues early, as it often prevents more extensive repairs.
- Requires a well-structured schedule and a dedicated team to manage this upkeep. If not monitored carefully, scheduled tasks may be skipped, leading to the same risks associated with corrective systems.
Predictive Maintenance Systems
Predictive maintenance systems represent the cutting edge of maintenance strategy. Incorporating data analysis and advanced technologies such as IoT sensors, these systems focus on predicting failures before they occur. Instead of relying on scheduled checks, predictive maintenance uses real-time data to assess the health of equipment continuously. Imagine having a weather app that alerts you to potential storms so you can prepare in advance.
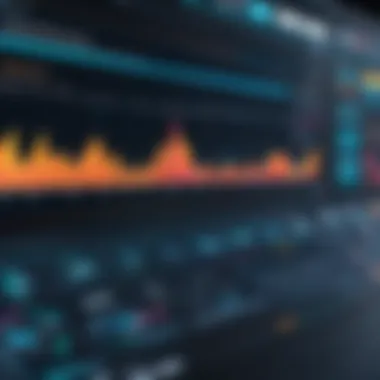
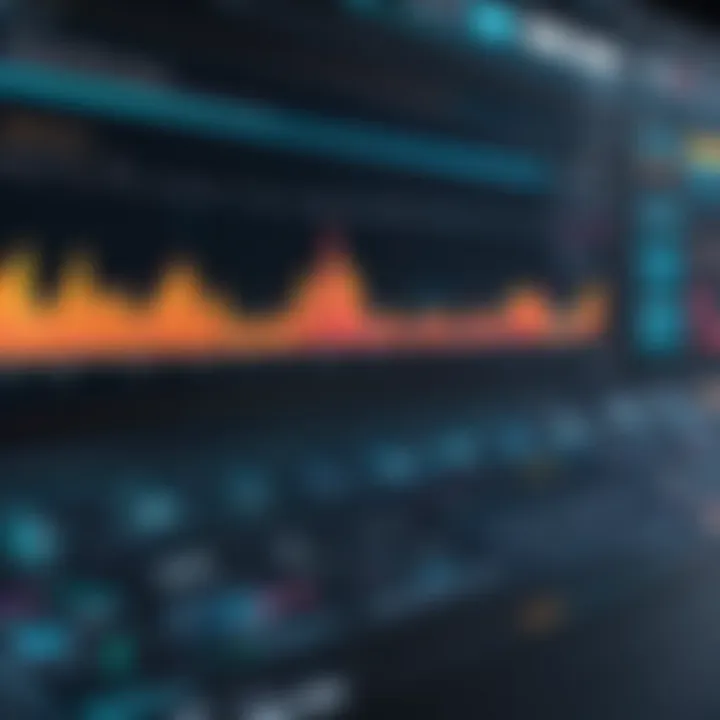
- Benefits:
- Considerations:
- Data-Driven: Insights from active monitoring allow for tailored maintenance strategies that consider the actual performance and conditions of each asset.
- Efficiency Gains: By reducing the frequency of unnecessary maintenance, businesses can allocate resources more effectively and even extend equipment lifespan.
- The initial investment in technology and training can be high. Organizations must be willing to adopt a culture aligned with data-driven decision making. Additionally, getting the right software should cater to the unique needs of the business operation.
In summary, choosing the right type of maintenance control system directly influences organizational efficiency and productivity. Careful consideration of each system's pros and cons helps business leaders to implement strategies that best match their operational goals, paving the way for improved maintenance management and overall performance.
Key Components of Maintenance Control Systems
Understanding the key components of maintenance control systems is like having the keys to a well-oiled machine. These elements are crucial in ensuring that maintenance operates smoothly and efficiently, playing a significant role in extending the life of assets and optimizing operational effectiveness. Each component, from asset management to work order management, serves its own function but ultimately contributes to a tapestry of reliability and efficiency.
Asset Management
Asset management is the backbone of any maintenance control system. This process encompasses the strategic and systematic management of assets throughout their lifecycle. It includes everything from acquisition to disposal while ensuring that assets perform at their optimal levels.
Using asset management tools allows organizations to track asset conditions, maintain records, and budget for repairs or replacements accordingly. Such proactive strategies reduce unexpected failures, ultimately saving time and costs in the long run. The right asset management practices foster informed decision-making, enabling organizations to concentrate on valuable assets and phase out underperforming ones.
In essence, good asset management translates to better allocation of resources and improved productivity. Technology plays a pivotal role here; many companies are leveraging platforms like IBM Maximo and SAP EAM to fine-tune their asset strategies.
Scheduling and Planning Tools
Scheduling and planning tools are critical in orchestrating maintenance tasks. A well-defined scheduling system can do wonders in streamlining operations. It keeps things organized and ensures that maintenance activities do not interfere with production demands.
The benefits of effective scheduling and planning tools are manifold:
- Resource Allocation: By understanding when and where maintenance resources are needed, organizations can minimize downtime and maximize equipment availability.
- Task Prioritization: Not all maintenance tasks have the same urgency; therefore, prioritizing tasks based on their impact is vital.
- Timely Updates: Real-time scheduling tools notify teams of upcoming maintenance tasks, allowing for adequate preparation and resource gathering.
In modern environments, tools such as Microsoft Project or more specialized solutions like preventative maintenance software provide company-wide insight into scheduling, tasks, and availability. These tools also simplify the complexities often associated with manual planning.
Work Order Management
Work order management can be viewed as the glue that holds maintenance control systems together. It oversees the entire process from issuing a work order, scheduling the work, to ensuring its completion. An efficient management system provides a clear outline of the work that needs to be done, who will do it, and how long it should take.
Effective work order management brings several key advantages:
- Traceability: Keeping records of past work orders allows organizations to trace issues back to their source, helping avoid future problems.
- Accountability: Defining responsibilities makes it easier to hold team members accountable, which ultimately leads to enhanced performance.
- Performance Metrics: Collecting data on work orders can provide insights into the workforce efficiency, helping to identify areas for improvement.
In practice, work order management solutions like Fiix or Hippo CMMS can automate many aspects of this process, creating a clear pathway from task initiation to completion.
In summary, the key components of maintenance control systems—asset management, scheduling and planning tools, and work order management—are not isolated elements. They work in tandem, creating a cohesive strategy which is foundational for any organization looking to optimize maintenance processes and enhance operational reliability.
This coherent framework not only maximizes efficiency but ultimately leads to a culture of proactive maintenance, where preventing issues takes precedence over merely reacting to them.
Technological Advances in Maintenance Control Systems
The landscape of maintenance control systems is rapidly evolving, notably driven by technological advances that significantly enhance efficiency and effectiveness. These developments allow organizations to transition from traditional methods of maintenance towards sophisticated systems that integrate multiple technologies. The ability to monitor assets in real-time, anticipate failures, and manage resources adeptly is no longer an aspiration but a tangible reality brought forth by the latest tools and methodologies.
IoT and Smart Sensors
Internet of Things (IoT) has revolutionized maintenance management. By embedding smart sensors in machinery, organizations can collect data continuously. This data can be utilized for predictive analysis, enabling maintenance teams to address potential issues before they escalate. Smart sensors monitor vibrations, temperature, operating hours, and more, providing real-time feedback that allows technicians to act swiftly.
- Benefits of IoT:
- Continuous monitoring helps pinpoint wear and tear.
- Reduces unplanned downtime through earlier detection of faults.
- Promotes data-driven decisions rather than reactive maintenance.
For example, if a manufacturing company implements vibration sensors on its motors, an alert can trigger maintenance personnel if the vibration exceeds the pre-assigned threshold. This proactive approach mitigates downtime and fosters efficient operations across the board.
Artificial Intelligence and Machine Learning Applications
Artificial Intelligence (AI) and Machine Learning (ML) are game-changers in maintenance control systems. These technologies help refine data analysis processes and improve maintenance strategies. AI algorithms are capable of learning from historical data, identifying patterns, and suggesting optimized maintenance schedules that can lead to significant cost savings.
- Key Applications of AI and ML:
- Predictive analytics for forecasting when maintenance should occur.
- Enhancing the accuracy of failure predictions, thus decreasing unnecessary maintenance actions.
- Continuous improving decision-making systems that adapt to new data inputs.
Consider an airline using AI for its fleet management. By analyzing historical maintenance records of its airplanes, AI can provide insights into when specific parts are likely to fail based on usage patterns, allowing for timely part replacements. This precise forecasting can result in lowered expenses and heightened safety standards.
Cloud Computing and Data Analytics
Cloud computing brings an entirely new dimension to maintenance control systems. By leveraging cloud technologies, organizations can centralize their data, allowing instant access to maintenance records and analytics from any location. This accessibility is vital for decision-makers who require real-time data to make informed choices.
- Advantages of Cloud Computing in Maintenance:
- Scalable data storage that grows with the organization.
- Enhanced collaboration among teams with centralized data accessibility.
- Cost efficiency, as organizations can minimize on-site infrastructure costs.
Moreover, when paired with powerful data analytics tools, organizations can filter and analyze vast amounts of maintenance data effortlessly. This combined ability can lead to uncovering insights previously obscured by data silos. An example is a transportation company utilizing cloud analytics to assess the performance of their fleet over time and make informed service adjustments.
"Implementing these technological advances not only optimizes resources but also lays the groundwork for future innovations in maintenance endeavors."
Implementing Maintenance Control Systems
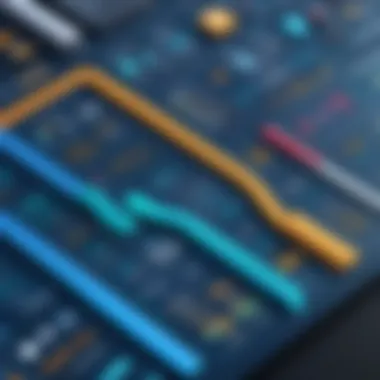
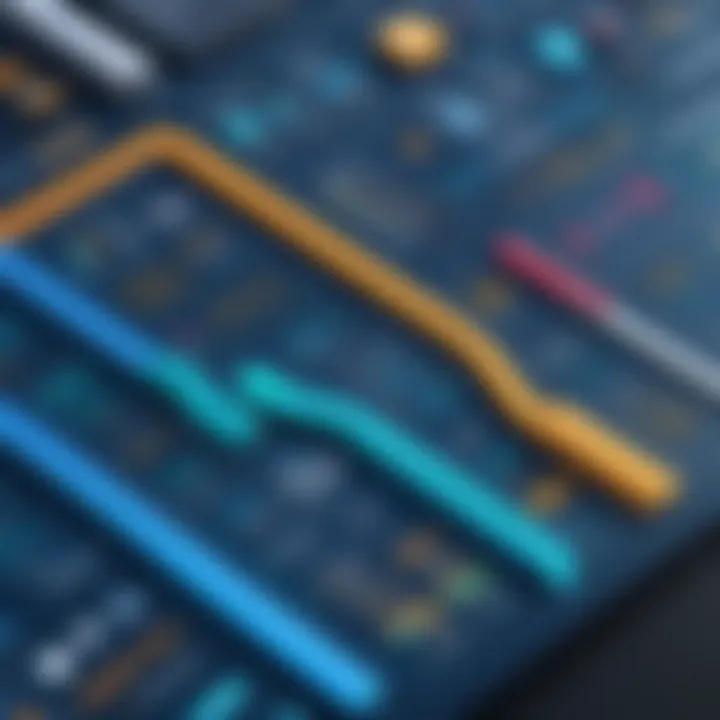
Implementing maintenance control systems is a crucial step for organizations seeking to enhance their operational efficiency and reduce equipment downtime. The importance of this topic cannot be overstated, as it encompasses various elements that, when addressed comprehensively, can lead to significant benefits.
These systems tailor maintenance strategies to specific organizational needs, ensuring that the right practices align with business goals. With a well-implemented maintenance control system, businesses not only streamline operations but also improve compliance with industry regulations. Understanding the nuances of implementation can significantly impact a company's ROI.
Assessing Organizational Needs
Identifying organizational needs is the starting point for implementing an effective maintenance control system. This involves conducting a thorough assessment of current practices, resources, and technological infrastructure.
Key elements to consider during this phase include:
- Current Maintenance Practices: Examine how maintenance tasks are currently performed and identify any gaps or inefficiencies.
- Asset Inventory: A detailed catalog of all assets is essential. This allows organizations to prioritize maintenance based on criticality and risk.
- Regulatory Compliance: Understanding industry-specific regulations helps organizations ensure that their maintenance practices are not only efficient but also compliant with laws and standards.
By engaging stakeholders across different departments, organizations can gather insights that highlight potential areas for improvement.
Choosing the Right Software Solutions
Selecting the appropriate software solution can make or break the implementation process. The market is populated with countless tools designed for maintenance management, making it imperative to do thorough research and matching software features with organizational needs.
Here are some factors to keep in mind when choosing software:
- Scalability: As the organization grows, the chosen software should be flexible enough to accommodate increased workload without necessitating a complete overhaul.
- Integration: Consider whether the software can seamlessly integrate with existing systems, ensuring a smooth data flow.
- User Interface: An intuitive interface reduces training time, leading to faster user adoption.
- Cost-effectiveness: Evaluate the total cost of ownership, not just upfront costs, to get a clear picture of financial impacts.
Careful consideration during the software selection phase aids in mitigating risks associated with poor system integration and user resistance.
Training and User Adoption
Once the software is in place, the focus shifts to training and ensuring acceptance among users. Skills development becomes paramount, as users must feel comfortable and capable of utilizing new systems effectively.
Here are some practical steps to facilitate user adoption:
- Comprehensive Training Programs: Develop training sessions tailored to different user groups, addressing their unique responsibilities and challenges.
- Ongoing Support: Establish channels for ongoing assistance—this could include dedicated help desks or online resources to troubleshoot common issues.
- Feedback Mechanisms: Encourage users to provide feedback about the new system, allowing for iterative improvements and fostering a sense of ownership.
Implementing maintenance control systems is a journey that necessitates careful planning and execution. By addressing organizational needs, selecting the right tools, and supporting users in their transition, businesses can set themselves on the path to enhanced operational performance and resilience in the face of challenges.
"A well-implemented maintenance control system is like a well-tuned engine; it runs smoothly and underlines operational success."
In the end, being proactive about the implementation process can yield long-lasting gains, positioning organizations for a future where maintenance is viewed not just as a function but as a strategic advantage.
Case Studies in Maintenance Control System Implementation
Case studies serve as critical learning tools within the realm of maintenance control systems. They illustrate real-world applications and outcomes, showcasing how businesses have navigated the complex waters of maintenance management. By diving into how various sectors have implemented these systems, decision-makers can glean valuable insights, assess methodologies, and strategize future actions. Importantly, case studies highlight what works well and what pitfalls to avoid, making them indispensable for organizations looking to adopt or enhance their maintenance strategies.
Manufacturing Sector
In the manufacturing sector, the implementation of maintenance control systems often makes the difference between seamless operations and costly downtime. A notable example is General Motors, which utilized a predictive maintenance program to monitor equipment through IoT sensors. When the sensors detected anomalies in equipment performance, maintenance personnel received alerts. This system allowed them to rectify issues before they escalated into costly breakdowns.
Benefits observed included:
- Higher equipment uptime
- Lower maintenance costs due to timely interventions
- Improved production schedules
- Better resource allocation as teams can focus on other priorities
Such case studies illustrate the advantages of marrying technology with human expertise in a sector where equipment reliability is paramount.
Healthcare Sector
In the healthcare industry, maintenance control systems play a pivotal role in ensuring that medical equipment operates without a hitch. A prime example can be seen in hospitals adopting advanced maintenance management systems to track essential medical devices. Take, for instance, the case of Mayo Clinic, which employed a comprehensive strategy integrating cloud-based software to manage equipment maintenance. The system enabled the healthcare facility to maintain compliance with regulations while keeping equipment functional and safe for patient use.
Key takeaways from their approach include:
- Enhanced patient safety through reliable medical devices
- Streamlined processes for maintaining compliance with health regulations
- Reduced costs by optimizing equipment lifespan and scheduling maintenance accordingly
This speaks volumes about the critical nature of maintenance in preserving not only operational efficiency but also patient outcomes.
Transportation Sector
The transportation sector has also seen transformative changes through maintenance control system implementation. A compelling case is that of Delta Air Lines, which adopted a predictive maintenance framework using data analytics. By continuously monitoring aircraft components, Delta’s maintenance team can proactively address potential malfunctions, which greatly reduces delays and increases flight safety.
Highlights from their findings emphasize:
- Greater flight schedule reliability
- Minimization of unexpected repair costs
- Enhanced safety protocols through rigorous, data-driven maintenance schedules
Understanding these advancements gives other businesses in the sector valuable perspectives on how best to leverage maintenance control systems for improved operational integrity.
"Learning from others’ experiences can often shortcut the path to effective solutions."
In summary, the examination of these case studies in diverse sectors demonstrates how varied approaches to maintenance control systems can yield different yet commendable results. Whether it’s for improving efficiency in a manufacturing setup, ensuring critical compliance in healthcare, or enhancing reliability in transportation, these examples provide a well-rounded view of the importance of managing maintenance effectively.
Challenges in Maintenance Control Systems
In the realm of maintenance control systems, several challenges can impede the smooth operation of these essential mechanisms. Understanding the nuances of these challenges is crucial for businesses seeking to optimize maintenance practices. By addressing these obstacles, organizations can unlock the true potential of their maintenance control systems, leading to enhanced operational efficiency and sustained productivity.
Resistance to Change
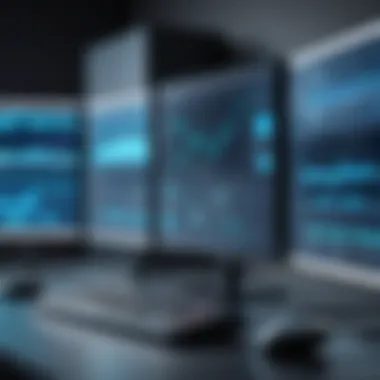
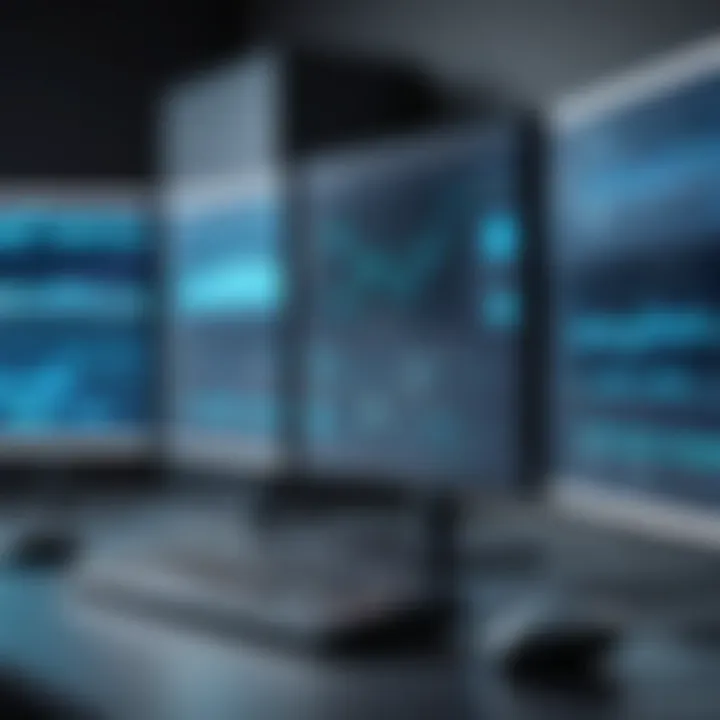
Resistance to change is a formidable barrier that many organizations face when implementing new maintenance control systems. Employees often grow accustomed to existing processes, and the prospect of change can be met with skepticism. This resistance can manifest in various ways, from passive non-compliance to outright opposition.
To combat this, organizations should focus on fostering an environment of open communication. Involving employees in the planning stages of the implementation can alleviate fears and misconceptions. Furthermore, highlighting the benefits of the new system—such as time savings, increased transparency, and fewer equipment failures—can help build buy-in. Training sessions can also play a pivotal role, as they not only impart necessary skills but also demonstrate the organization's commitment to supporting its staff through the transition.
Integration with Existing Systems
Integrating maintenance control systems with existing infrastructure is often a challenging endeavor. Many organizations operate on a patchwork of legacy systems, which may not readily connect with newer technologies. This can create data silos, obstructing information flow and creating inefficiencies.
For a seamless integration, it’s crucial to conduct a thorough assessment of the current systems. Identify which elements are critical to ongoing operations and determine how they can interface with the new system. A phased approach may be beneficial, allowing for gradual integration rather than an all-at-once overhaul. Additionally, working closely with software vendors to ensure compatibility is vital in creating a cohesive ecosystem that enhances data sharing and operational efficiency.
Cost Considerations
Cost is often at the forefront of discussions when it comes to maintenance control systems. The initial investment can be substantial, encompassing software licenses, hardware, and training expenses. However, it’s important to look beyond the upfront costs to appreciate the potential long-term savings.
Organizations can benefit from conducting a cost-benefit analysis that considers both direct and indirect savings. Reductions in downtime, enhanced asset life, and improved productivity can all contribute to a favorable return on investment. Additionally, adopting a flexible budgeting approach may allow organizations to allocate resources effectively without straining financial performance.
Consider this: "While the initial costs can be daunting, the long-term advantages of improved maintenance practices often outweigh the short-term financial impacts."
In summary, the challenges associated with maintenance control systems—resistance to change, integration difficulties, and cost concerns—are significant yet manageable obstacles. By adopting a strategic approach that includes communication, careful planning, and financial analysis, organizations can not only navigate these challenges but also leverage their maintenance systems to drive performance and efficiency.
Best Practices for Maintenance Management
In the realm of maintenance control systems, establishing best practices can be likened to laying the foundation of a sturdy house. A well-structured approach not only enhances operational efficiency but also cultivates a proactive mentality across the entire organization. Adopting these best practices signals to employees the significance of maintenance and prompts a collective commitment to preserving equipment and infrastructure.
Developing a Maintenance Culture
Fostering a robust maintenance culture is essential for the longevity of any organization. When an environment values maintenance, staff at all levels—from the floor workers to executive leadership—understands their role in ensuring equipment reliability. Furthermore, it encourages open communication about maintenance needs, leading to timelier interventions.
In practice, leaders can facilitate this culture development through:
- Regular training sessions: Offering workshops on techniques, best practices, and technologies keeps even experienced employees in the loop.
- Recognition programs: Acknowledging individuals or teams that excel in maintenance efforts can be a powerful motivator. When workers see that their contributions are noticed, it enhances their commitment.
- Transparent reporting mechanisms: Encouraging staff to report inefficiencies or equipment issues without fear of retribution fosters a culture of accountability.
Ultimately, when employees perceive maintenance as integral to their job instead of an afterthought, productivity can significantly increase. A proactive workforce promotes minimal downtime and enhanced performance across the board.
Utilizing Analytics for Decision Making
In today's data-driven world, relying on instinct is no longer viable for effective decision-making in maintenance management. Incorporating analytics allows organizations to glean insights from vast amounts of data collected over time. With the right analytical tools, decision-makers can forecast equipment failures, optimize maintenance schedules, and prolong asset life.
Some key aspects of analytics in maintenance include:
- Predictive Analysis: Using historical data to anticipate potential equipment failures, thus enabling timely adjustments to maintenance schedules.
- Performance Metrics Tracking: Identifying key performance indicators (KPIs) that reflect maintenance efficiency can help organizations pinpoint areas for improvement. Metrics like Mean Time Between Failures (MTBF) offer critical insights.
- Root Cause Analysis: By employing data analytics, organizations can investigate what caused a failure in the first place, thus preventing its recurrence.
"Data is like a guide that illuminates the path to informed decisions. Without it, you're merely wandering in the dark."
Future Trends in Maintenance Control Systems
Exploring the future trends in maintenance control systems is crucial for any organization aiming to remain competitive and efficient in today’s fast-paced business environment. The maintenance landscape is evolving rapidly, driven by advancements in technology and changing consumer expectations. Companies that stay ahead of these trends can expect not only to increase operational efficiency but also to boost overall productivity and sustainability.
In this section, we’ll delve into two primary emergent trends: remote monitoring and maintenance as well as sustainable maintenance practices. Both of these elements are crucial for optimizing resources and enhancing decision-making in maintenance management.
Remote Monitoring and Maintenance
Remote monitoring refers to the ability to oversee equipment and systems from a distance, leveraging technologies such as the Internet of Things (IoT) and smart sensors. This trend is becoming increasingly vital for organizations across various sectors, including manufacturing, healthcare, and transportation.
With remote monitoring, businesses can keep a keen eye on their assets, diagnosing potential problems before they escalate into full-blown failures. For instance, a factory outfitted with IoT sensors can track a machine’s operational data in real-time, catching anomalies and inefficiencies on the fly. Staff can receive alerts directly to their mobile devices, enabling immediate action without the need for a physical inspection.
Benefits of remote monitoring include:
- Reduced Downtime: Early detection of issues leads to faster resolution, minimizing production halts.
- Cost Savings: Preventative maintenance through monitoring can mitigate the costs associated with unplanned repairs.
- Informed Decision-Making: Data-driven insights can guide maintenance schedules more effectively.
Sustainable Maintenance Practices
As environmental considerations gain traction worldwide, sustainable maintenance practices are becoming a non-negotiable facet of maintenance control systems. Organizations are increasingly tasked with not only maintaining their assets effectively but also doing so in an environmentally conscious way.
Sustainable maintenance involves practices that reduce waste, lower emissions, and focus on longevity. For example, using recyclable materials in repairs, implementing energy-efficient processes, and adhering to eco-friendly standards can make a significant difference. Not only does this approach contribute to a healthier planet, but it can also yield financial benefits through energy savings and waste reduction.
Key considerations for sustainable maintenance include:
- Lifecycle Thinking: Recognizing the environmental impacts of equipment from acquisition through disposal encourages more prudent resource management.
- Regulatory Compliance: Staying compliant with environmental laws not only avoids penalties but bolsters corporate reputation.
- Workforce Engagement: Encouraging employees to adopt sustainable practices fosters a culture of responsibility and innovation.
"Sustainability is no longer just a buzzword; it's a business imperative. Organizations that embrace this shift are likely to thrive in the long term."
Culmination
The conclusion serves as a vital transition from the exploration of maintenance control systems to the practical applications of the insights gained. It summarizes the significant elements discussed throughout the article, helping readers synthesize the various components, benefits, and considerations brought forth. Understanding the value of maintenance control systems not only contributes to decision-making but also fosters a culture where proactive maintenance is prioritized.
Summary of Insights
Throughout this article, we have examined various aspects of maintenance control systems. Here is a summary of the key insights garnered:
- Types of Systems: Knowledge of corrective, preventive, and predictive maintenance systems allows organizations to tailor their approaches based on specific needs and contexts. Each type serves distinct purposes, making it critical to choose the correct model for effective maintenance.
- Technological Integration: The integration of IoT, AI, and cloud computing has revolutionized maintenance practices. These technologies drive efficiencies by providing real-time data and predictive capabilities, which transform how maintenance tasks are approached and executed.
- Implementation Challenges: The article highlighted common challenges such as resistance to change and cost considerations. Understanding these hurdles can prepare decision-makers to navigate the complexities associated with introducing new systems into existing workflows.
- Best Practices: Developing a strong maintenance culture and utilizing analytics for informed decisions were emphasized as essential strategies to enhance organizational productivity.
In summary, these insights lay the groundwork for organizations looking to optimize their maintenance strategies and make informed decisions about software solutions.
Final Thoughts
As we look to the future, maintenance control systems will continue to evolve. Companies that proactively engage with the latest developments in technology and management practices will have a competitive edge. It’s not just about keeping the machines running; it’s about understanding the data, reacting promptly to maintenance needs, and aligning with organizational goals for long-term efficiency. Organizations should be ready to adapt and innovate, fostering environments where change is welcomed rather than resisted.
In a rapidly changing business landscape, those who view maintenance control systems as strategic assets rather than mere operational tools will ultimately thrive. Investing in knowledge, technology, and culture will prove to be a significant catalyst for improved productivity and resource utilization.