Comprehensive Maintenance Management Guide
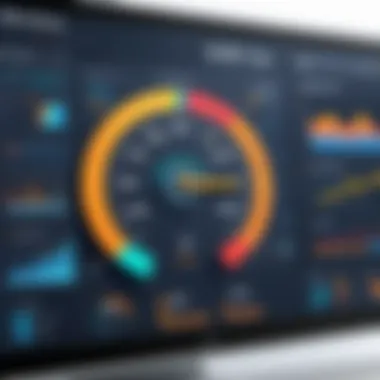
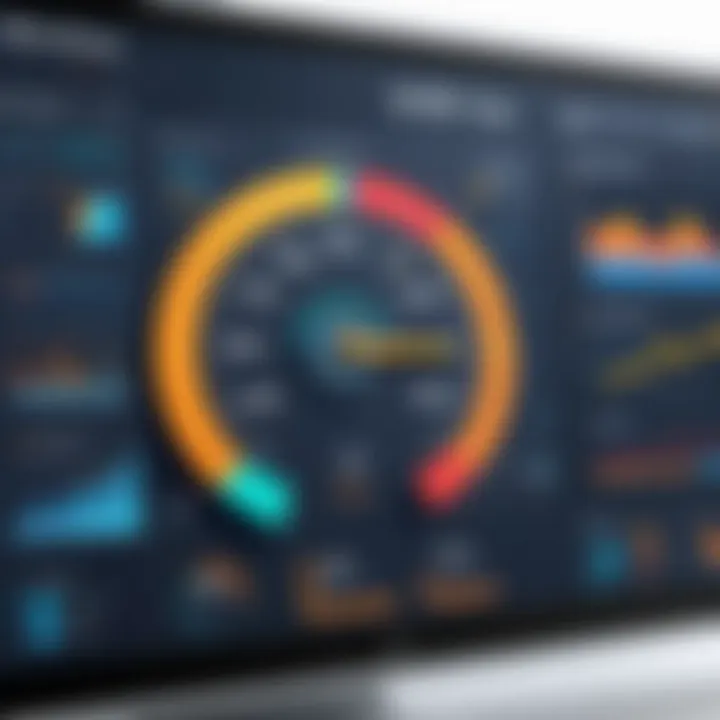
Intro
Maintenance management is a critical function in organizations, influencing operational continuity and overall productivity. It encompasses a range of strategies and activities aimed at ensuring that assets perform optimally over their lifespan. This guide offers a detailed exploration of maintenance management, catering specifically to B2B stakeholders who seek to enhance their practices.
The relevance of maintenance management cannot be overstated. In today’s competitive environment, organizations are increasingly embracing proactive approaches to manage their assets. By integrating effective maintenance strategies, companies can not only extend the life of their equipment but also improve productivity and reduce operational costs. The scope of maintenance management extends beyond basic upkeep; it incorporates advanced methodologies and technologies that underpin best practices.
In this guide, we will delve into various aspects of maintenance management:
- Overview of methodologies used in maintenance planning and execution.
- Technological advancements that facilitate maintenance tasks.
- Frameworks that organizations can adopt for better management.
- Best practices that ensure efficiency and reliability in operations.
Understanding these topics enables decision-makers to cultivate a proactive stance towards asset management. The ability to optimize maintenance processes can significantly impact an organization’s bottom line. Through thoughtful implementation of the insights provided here, businesses can look forward to a more resilient and efficient operational strategy.
Understanding Maintenance Management
Maintenance management is a critical function within any organization where assets play a key role in operational capabilities. Proper maintenance management ensures these assets operate efficiently, safely, and remain in service for as long as possible. It covers various practices that aim to optimize the performance of resources while minimizing operational disruptions. To grasp the essence of effective maintenance management is to understand its definition and importance across a variety of industries.
Definition of Maintenance Management
Maintenance management refers to the systematic process of maintaining assets to maximize their lifespan and efficiency. This process includes planning, scheduling, controlling, and monitoring maintenance activities. At its core, it ensures asset reliability while reducing downtime and costs associated with repairs and replacements. Several methodologies fall under this umbrella, such as preventive and predictive maintenance, which focus not only on reacting to failures but also proactively preventing them.
For organizations, the implementation of maintenance management can involve different approaches. Various software solutions exist, such as Computerized Maintenance Management Systems (CMMS), providing a framework for tracking, managing, and optimizing maintenance tasks. A clear definition allows organizations to establish their specific needs and optimize their asset management workflows effectively.
Importance in Various Industries
The impact of maintenance management stretches across different sectors, confirming its relevance and necessity. In manufacturing, for example, unplanned downtimes can lead to significant losses. Effective maintenance management helps in enhancing production efficiency and reducing waste. Similarly, in transportation systems, regular maintenance ensures safety, reliability, and adherence to regulations.
In healthcare, maintenance management plays a crucial role in maintaining medical equipment and facilities. Ensuring that all tools are in working order can directly affect patient care and outcomes. Finally, for utility services such as water and electricity, robust maintenance processes safeguard infrastructure integrity, ultimately ensuring continuous and reliable service.
Key benefits of understanding maintenance management include:
- Increased Asset Lifespan: Regular maintenance extends the life of equipment, leading to long-term cost savings.
- Enhanced Safety: Well-maintained tools prevent accidents and injuries, ensuring a safe working environment.
- Improved Efficiency: Proper management minimizes wastage of resources and maximizes productivity.
- Compliance and Regulation Adherence: Many industries face strict regulatory requirements; effective maintenance helps in meeting these standards.
"A well-executed maintenance management strategy not only preserves assets but also enhances an organization’s overall operational capability."
Understanding these elements creates a solid foundation for subsequent sections. These sections will unfold the various components essential to grasp the depth of maintenance management.
Key Concepts in Maintenance Management
Understanding the principal concepts in maintenance management is crucial for the success of any maintenance strategy. It provides a framework that organizations can use to ensure their assets operate at peak performance. Effectively managing maintenance ensures that equipment does not fail unexpectedly and that resources are allocated efficiently. By grasping these key concepts, organizations can streamline their processes, reduce costs, and enhance the reliability of their operations.
Types of Maintenance
Different approaches to maintenance serve unique needs within organizations. Each type has distinct characteristics, advantages, and considerations.
Preventive Maintenance
Preventive maintenance (PM) refers to scheduled actions aimed at maintaining equipment and preventing breakdowns before they happen. This can include regular inspections, lubrication, adjustments, and the replacement of worn parts. A key characteristic of PM is its proactive nature, which minimizes the likelihood of unexpected failures.
The unique feature of preventive maintenance is that it operates on a fixed schedule. This predictability makes it a popular choice for many industries, as it allows organizations to prioritize their workload and allocate resources effectively. However, one disadvantage is that it can sometimes result in unnecessary service on equipment that may not require immediate attention, leading to increased costs.
Corrective Maintenance
Corrective maintenance (CM) is reactive, occurring after a failure has happened. In this case, actions are taken to restore an asset to its operational state. The key characteristic of corrective maintenance is its direct response to physical breakdowns rather than planned schedules.
This approach can be beneficial, especially for equipment that operates under heavy conditions where regular maintenance may not be feasible. However, one drawback is that it can lead to longer downtimes and increased repair costs, ultimately affecting productivity.
Predictive Maintenance
Predictive maintenance (PdM) utilizes data analysis tools and techniques to predict when maintenance should be performed. By monitoring the condition of equipment in real-time, organizations can anticipate failures and perform maintenance just in time, minimizing disruption. Its key characteristic is its focus on analytics and condition monitoring.
The unique feature of predictive maintenance is its data-driven decision-making process. This approach can enhance reliability and prolong asset life. However, the initial investment in technology and training can be significant, which might not suit smaller organizations.
Condition-Based Maintenance
Condition-based maintenance (CBM) is closely related to predictive maintenance but focuses specifically on the actual condition of the equipment rather than on predictions based on data. This type of maintenance is performed only when certain indicators show signs of decreasing performance or upcoming failure.
The key characteristic of condition-based maintenance is its focus on real-time data, allowing organizations to optimize their maintenance actions precisely. One advantage is that it reduces unnecessary maintenance, saving time and resources. However, it requires a robust monitoring system, which might be complex to implement for some businesses.
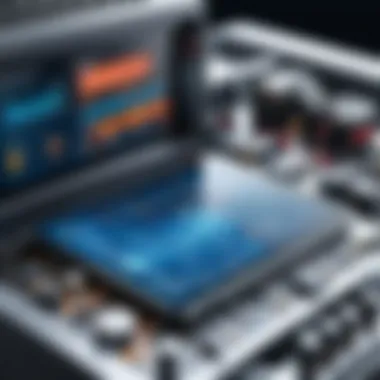
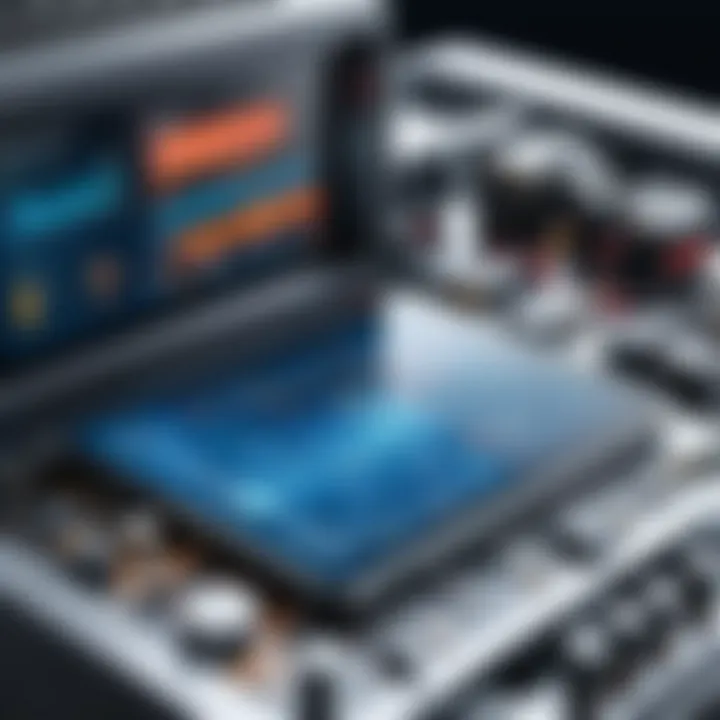
Life Cycle of Assets
The life cycle of assets encompasses the stages assets go through from acquisition to disposal. Understanding these stages is vital for maintenance management as it defines how maintenance strategies can evolve.
Typically, the life cycle includes the following stages: acquisition, utilization, maintenance, and disposal. Each phase presents unique challenges and opportunities for maintenance interventions. In the acquisition phase, decisions regarding appropriate maintenance plans can be initiated. Utilization outlines the demand on the asset and informs the frequency and type of maintenance required. The maintenance phase itself directly impacts the asset's longevity, while proper disposal ensures environmental compliance and maximizes residual value.
Managing these stages effectively can lead to significant increases in the total lifespan of assets and ultimately, improve organizational efficiency.
The Role of Technology in Maintenance Management
The integration of technology into maintenance management has fundamentally changed how organizations approach keeping their assets in optimal condition. With the continual evolution of tools and systems, businesses can now leverage advanced technologies to streamline their maintenance operations, ensure higher reliability, and extend the lifespan of their assets. Effectively utilizing technology not only reduces downtime but can also lead to significant cost savings. Therefore, understanding how these technologies function and their impact on maintenance management is essential for organizations aiming to remain competitive in today's fast-paced environment.
CMMS Overview
A Computerized Maintenance Management System, or CMMS, serves as the backbone of effective maintenance management. CMMS software automates many traditional maintenance tasks, such as work order management, inventory control, and preventive maintenance scheduling. This allows organizations to manage their assets more effectively.
The importance of a CMMS cannot be overstated. It provides a centralized platform for storing information about equipment, maintenance history, and scheduling needs. Some key features of CMMS include:
- Work Order Management: This enables the creation, tracking, and prioritization of work orders. It reduces response time and improves task accountability.
- Inventory Management: Companies can keep track of parts and supplies used for maintenance, ensuring they have the necessary materials on hand when required.
- Reporting and Analytics: CMMS systems offer insights into maintenance performance, which can lead to better decision-making and strategic planning.
A well-implemented CMMS can lead to fewer equipment failures and unplanned downtime, ultimately contributing to a more efficient and cost-effective operation.
IoT and Smart Maintenance Solutions
The Internet of Things (IoT) has introduced a new dimension to maintenance management, creating possibilities for what is termed smart maintenance. Devices and sensors can now be embedded in machinery and equipment to monitor their conditions in real-time. This connectivity allows organizations to collect vast amounts of data related to performance and maintenance needs.
Smart maintenance solutions offer numerous advantages:
- Predictive Maintenance: By analyzing data from IoT sensors, companies can predict when an asset is likely to fail. This allows maintenance to be performed just before a failure occurs, minimizing unexpected downtime.
- Real-Time Monitoring: Operators can receive alerts about equipment status, enabling swift corrective actions before minor issues turn into major problems.
- Data-Driven Decisions: The analytics derived from IoT data can provide deeper insights, helping organizations refine their maintenance strategies.
However, adopting these technologies requires careful consideration. Organizations need to ensure they have the appropriate infrastructure and skill sets to manage and interpret the data collected from IoT devices. Integrating new technologies with existing systems can sometimes present challenges; thus, a thoughtful approach is necessary for successful implementation.
"The advantage of technology in maintenance management is not merely in streamlining processes but also in empowering data-driven decisions that can significantly reshape business strategies."
Understanding the role of technology, particularly CMMS and IoT solutions, is crucial for organizations aiming to optimize their maintenance management practices. As the landscape evolves, those who adapt and harness these tools will find themselves better positioned to address both current and future maintenance challenges.
Best Practices for Effective Maintenance Management
Effective maintenance management is essential for optimizing operations and ensuring the longevity of assets. This section covers some of the best practices that organizations can adopt to establish a robust maintenance framework. By focusing on these practices, businesses can enhance productivity, minimize downtime, and ultimately achieve a higher return on their investments.
Establishing Maintenance Goals
Setting clear maintenance goals is a cornerstone of effective management. It helps align maintenance activities with the overall objectives of the organization. Goals should be Specific, Measurable, Achievable, Relevant, and Time-bound (SMART). For instance:
- Specific: Define what needs maintenance, e.g., "Reduce machine downtime by 10%.
- Measurable: Ensure that progress can be tracked with measurable indicators.
- Achievable: Set goals that are realistically attainable.
- Relevant: Goals should align with the organization's mission and strategic objectives.
- Time-bound: Establish a timeline for achieving the goals.
These goals can vary from increasing equipment efficiency to reducing maintenance costs. When the goals are clear, it enables the maintenance teams to prioritize tasks and allocate resources effectively.
Resource Allocation and Budgeting
Another critical aspect of effective maintenance management is resource allocation and budgeting. This involves determining the necessary resources—both financial and human—for implementing the maintenance plan. Proper allocation ensures that maintenance departments can operate without friction.
- Assess Needs: Evaluate what resources are necessary for maintenance tasks. This could include labor, materials, and equipment.
- Budget Wisely: It is crucial to prepare a budget that encompasses not just routine maintenance but also unexpected repairs.
- Prioritize Investments: Some assets may require more investment than others, depending on their criticality to operations. Prioritizing based on need can help in managing finances effectively.
- Monitor Expenditures: Regularly tracking maintenance spending can help identify areas of over-expenditure and ensure that resources are used efficiently.
Effective budgeting in maintenance management not only saves costs but also improves overall operational efficiency.
Implementing a Maintenance Management Strategy
Implementing a maintenance management strategy is crucial for organizations aiming to achieve optimal performance and resource utilization. This strategic approach lays the groundwork for designing, executing, and reviewing maintenance processes effectively. By having a structured strategy, businesses can ensure that resources—both human and material—are used as efficiently as possible while minimizing downtime and extending the lifespan of assets. A well-defined maintenance strategy can lead to reduced operational costs and improved safety in the workplace.
Assessment of Existing Processes
Before creating a new maintenance plan, organizations must conduct a thorough assessment of their existing processes. This step involves evaluating current maintenance strategies, systems, and workflows. Companies should gather data on equipment performance, maintenance history, and any issues that may have occurred in the past.
Some important aspects to consider in this assessment include:
- Identifying bottlenecks in the current process
- Evaluating the frequency of equipment failures
- Analyzing response times to maintenance requests
By understanding existing shortcomings, companies can recognize what works well and what does not. This facilitates a more informed decision-making process when developing a new maintenance plan.
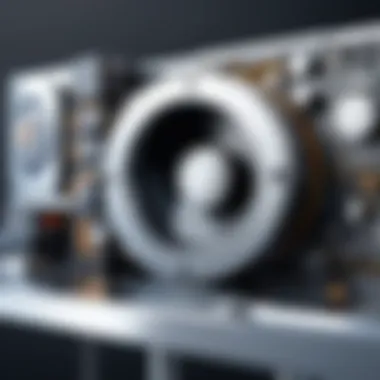
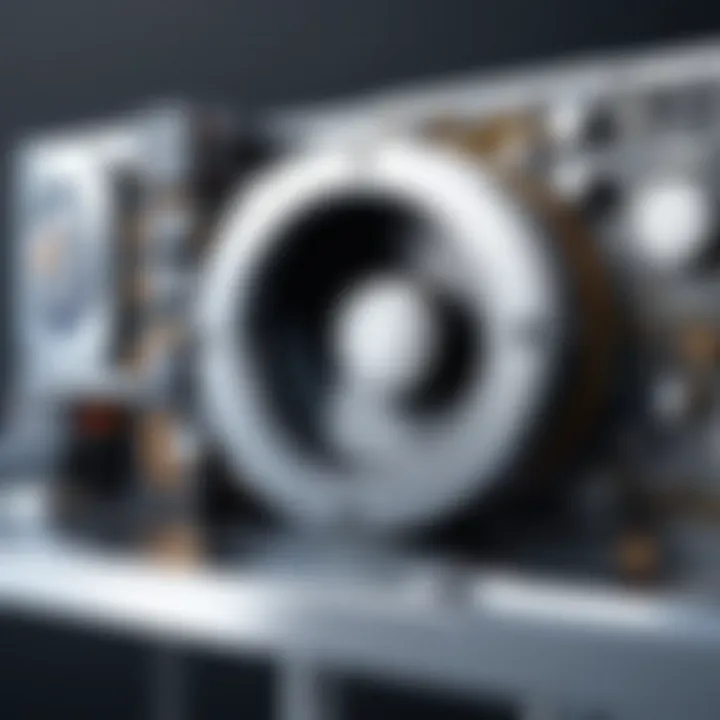
Creating a Maintenance Plan
Once the assessment is complete, the next step is to create a maintenance plan that aligns with organizational goals. A well-structured plan should include clear objectives and tasks that need to be accomplished. This plan will guide maintenance activities and ensure consistency in execution.
Key components of an effective maintenance plan can include:
- Scheduled Maintenance: Define regular maintenance intervals based on manufacturer recommendations or past performance data.
- Resource Allocation: Outline which personnel and tools are needed for maintenance tasks.
- Emergency Procedures: Establish protocols for unexpected equipment failure to minimize downtime.
An effective maintenance plan acts as a roadmap for maintenance managers, making it easier to track progress and address issues as they arise.
Training Personnel
The success of a maintenance management strategy heavily relies on the knowledge and skills of the personnel involved. Therefore, training is an essential aspect that should not be overlooked. By equipping staff with the right skills, organizations can enhance their maintenance capabilities and ensure tasks are performed effectively.
Key training areas to focus on include:
- Technical Skills: Ensure staff are trained on the equipment they will be working on.
- Safety Training: Teach personnel about safety protocols to minimize workplace accidents.
- Communication Skills: Enhance the ability of staff to report issues and collaborate on maintenance tasks efficiently.
Investing in personnel training not only fosters a competent workforce but also promotes a culture of continuous improvement within the organization. This ultimately supports the overall objectives of the maintenance management strategy.
A well-executed maintenance management strategy leads to lower operational costs and increased asset longevity.
By systematically assessing existing processes, creating a detailed maintenance plan, and investing in training, organizations can enhance their maintenance management practices significantly. This proactive approach positions businesses for sustainability and growth.
Maintenance Metrics and KPIs
In the realm of maintenance management, the identification and utilization of metrics and key performance indicators (KPIs) are paramount. These tools provide insights into operational efficiency, asset reliability, and overall process effectiveness. By establishing clear metrics, organizations can benchmark their performance, identify areas for improvement, and achieve strategic goals. The essence of maintenance metrics lies not only in measuring current performance but also in encouraging proactive maintenance practices.
Maintenance metrics can significantly impact decision-making processes. When organizations have access to relevant data, they can optimize resource utilization and prioritize tasks effectively. This leads to reduced downtime, increased productivity, and ultimately, enhanced profitability. Moreover, metrics encourage a culture of continuous improvement as teams strive to meet or exceed established targets.
Effective use of maintenance metrics supports a strategic framework that incorporates both short-term and long-term goals. Different industries may prioritize different metrics based on their unique challenges and objectives. Understanding which metrics best align with business goals is crucial for maximizing operational effectiveness.
"Performance metrics are not just numbers; they are insights that drive improvements in the maintenance process."
Common Maintenance Metrics
Several key metrics are often monitored in maintenance management:
- Mean Time Between Failures (MTBF): This metric indicates the average time between equipment failures. A higher MTBF suggests better reliability and fewer interruptions in production.
- Mean Time To Repair (MTTR): This reflects the average time taken to repair a failed asset. Shorter MTTR signifies efficient repair processes and quick recovery from potential losses.
- Overall Equipment Effectiveness (OEE): OEE is a comprehensive metric that considers availability, performance, and quality. It provides insight into how effectively manufacturing operations are running.
- Maintenance Cost as a Percentage of Replacement Asset Value (RAV): This metric helps organizations track maintenance spending relative to the total value of their assets, ensuring that maintenance investments align with asset value.
- Work Order Completion Rate: The percentage of work orders completed on time indicates the efficiency of the maintenance team and helps in workload management.
Each of these metrics serves a specific purpose, and creating a balanced mix is essential for gaining a holistic understanding of maintenance performance. Organizations should determine which metrics matter most in their context and utilize them accordingly.
Evaluating Maintenance Performance
Evaluating maintenance performance is a multifaceted process that extends beyond simply measuring metrics. It encompasses the analysis of data collected over time to make informed decisions. For a thorough assessment, organizations must consider both quantitative and qualitative aspects.
Performance evaluations should integrate the following:
- Trend Analysis: Tracking metrics over time allows organizations to identify trends and variances. An upward trend in MTTR might indicate potential issues in the repair process, while a decreasing MTBF may signal emerging problems with specific assets.
- Benchmarking: Comparing performance metrics with industry standards or competitors helps organizations gauge their relative performance and identify best practices. Understanding where one stands in relation to peers can provide vital insights for improvement.
- Root Cause Analysis: When metrics reveal discrepancies, a detailed investigation is crucial. Root cause analysis can uncover why certain maintenance tasks are underperforming and lead to effective corrective measures.
- Employee Feedback: Engaging the maintenance team in evaluations can yield valuable insights that data alone may not reveal. Employee experience often provides context for metrics and highlights areas needing improvement.
In summary, effective evaluation hinges on a combination of robust data analysis and the human element. Only by addressing both aspects can organizations fully comprehend their maintenance performance and set actionable goals for improvement.
Challenges in Maintenance Management
Maintenance management is central to asset reliability and efficiency in various industries. However, organizations encounter multiple challenges that can hinder effective maintenance practices. Understanding these challenges is essential for any organization aiming to optimize their maintenance strategy. These issues often stem from various internal and external factors that influence resource allocation, process implementation, and the acceptance of necessary changes. Addressing these challenges not only improves operational performance but also enhances asset longevity.
Resource Constraints
Resource constraints are perhaps one of the most glaring challenges in maintenance management. Limited budgets, inadequate manpower, and insufficient tools can severely affect maintenance activities. Often, organizations struggle to maintain an optimal balance between available resources and the demands placed on maintenance teams. When resources are stretched too thin, it can lead to rushed maintenance, resulting in poor quality work and ultimately more downtime.
Key factors regarding resource constraints include:
- Budget Limitations: Tight budgets can restrict investments in quality training, advanced tools, or new technologies.
- Workforce Shortage: A lack of skilled technicians can hinder the execution of maintenance tasks, which can lead to critical failures.
- Equipment Access: Limited availability of tools or vital spare parts can delay necessary maintenance.
To tackle resource constraints, organizations should carefully assess their maintenance priorities and allocate funds wisely. Organizations can also consider investing in training for existing staff, as this can significantly enhance workforce capabilities without the immediate need to hire additional personnel.
Resistance to Change
Resistance to change is another hurdle that organizations face in maintenance management. With the introduction of new technologies and methodologies, employees may feel uncertain or threatened. This resistance can prevent organizations from fully leveraging modern maintenance tools and strategies such as Computerized Maintenance Management Systems (CMMS) or predictive analytics.
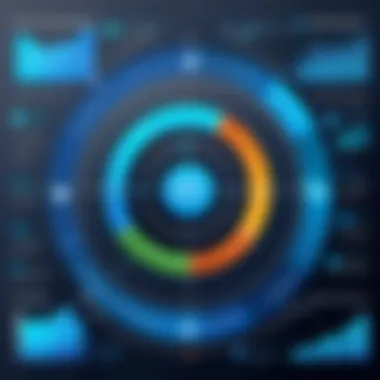
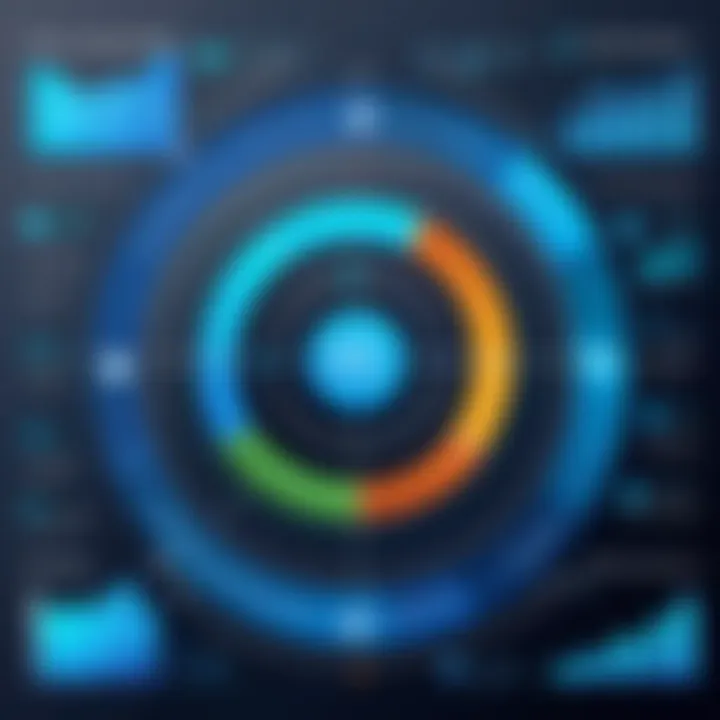
Factors contributing to resistance to change include:
- Fear of the Unknown: Employees might doubt the effectiveness of new systems and fear their job security.
- Lack of Training: Insufficient training on new tools makes personnel reluctant to adopt them.
- Cultural Factors: An ingrained culture of doing things a certain way can be hard to shift.
To overcome this resistance, organizations should prioritize clear communication about the benefits of change. Providing comprehensive training and involving staff in the decision-making processes can foster a more inclusive environment. Furthermore, organizations can identify ‘change champions’ within teams who can advocate and facilitate the adaptation process.
Successful change management is not only about implementing new systems but also about ensuring that staff feels supported and empowered throughout the transition.
Regulatory and Compliance Issues
Regulatory and compliance issues are critical components of maintenance management. These factors ensure that organizations adhere to laws, regulations, and industry standards that govern their operations. Non-compliance can result in significant penalties, damage to reputation, and operational inefficiencies. Therefore, understanding the implications of regulatory requirements is essential for effective maintenance management.
Industry Standards and Guidelines
Maintaining compliance with industry standards and guidelines is a fundamental aspect of managing maintenance effectively. Various industries have established regulations tailored to their specific operational risks. For instance, the Occupational Safety and Health Administration (OSHA) in the United States mandates safety practices in workplace environments. In the manufacturing sector, adhering to ISO 9001 ensures quality management in processes.
Organizations must implement regular audits and assessments to validate that their maintenance practices align with these regulations. This not only enhances safety but also improves service quality and operational reliability. Additionally, meeting these standards can enhance the organization’s credibility, attracting potential clients and partners. Organizations may also undergo certifications that demonstrate compliance, further solidifying their reputation in the marketplace.
The Impact of Non-Compliance
The repercussions of non-compliance can be severe. Organizations face financial penalties and legal challenges when they fail to adhere to established regulations. In extreme cases, non-compliance can result in operational shutdowns or revocation of licenses, directly affecting profitability. More than a financial burden, non-compliance can also damage an organization’s brand reputation.
Moreover, non-compliance often leads to increased scrutiny from regulatory bodies, making future inspections daunting. Employees may suffer as well, facing unsafe working conditions if proper maintenance standards are not upheld. To mitigate these risks, organizations must have robust compliance strategies in place, integrating them into their maintenance management systems.
Understanding the regulatory framework is essential for sustainable operational success.
In summary, compliance with industry standards is not merely a legal obligation but a strategic advantage. It fosters operational excellence, ensures employee safety, and protects organizational integrity. Organizations must prioritize regulatory and compliance issues within their maintenance management framework for long-term sustainability and success.
Future Trends in Maintenance Management
As industries evolve, so do the methodologies employed in maintenance management. Understanding future trends in this field is crucial for organizations aiming to stay competitive and efficient. With the advent of new technologies, maintenance strategies are shifting towards data-driven approaches. This section discusses two significant trends: predictive analytics and artificial intelligence applications.
Predictive Analytics
Predictive analytics leverages data, statistical algorithms, and machine learning techniques to identify the likelihood of future outcomes based on historical data. In maintenance management, this means foreseeing potential equipment failures before they occur. By analyzing patterns, organizations can make informed decisions, thereby reducing downtime and costs associated with unexpected breakdowns.
The benefits of predictive analytics are numerous:
- Increased uptime: By predicting failures, maintenance can be scheduled proactively.
- Resource optimization: Allows for better allocation of maintenance personnel and resources.
- Cost efficiency: Reduces emergency repair costs and extends equipment life.
Organizations must consider several factors when implementing predictive analytics:
- Data quality: Accurate and relevant data is essential for reliable predictions.
- Integration with existing systems: Ensuring compatibility with current maintenance management systems is vital.
- Skilled personnel: Having staff trained in analytics is key for effective implementation.
"Predictive analytics enhances decision-making by turning reactive maintenance into a proactive strategy."
Artificial Intelligence Applications
Artificial intelligence (AI) is transforming maintenance management by automating processes and providing deeper insights into asset performance. Through machine learning algorithms, AI can analyze vast amounts of data more quickly than humans, helping to streamline decision-making and improve efficiency.
Some applications of AI in maintenance management include:
- Automated reporting: AI can generate maintenance reports based on real-time data, saving time and improving accuracy.
- Anomaly detection: AI systems can identify unusual patterns indicating potential issues, allowing for timely interventions.
- Predictive maintenance: Similar to predictive analytics, AI can enhance prediction models, providing more precise forecasts.
Adopting AI technologies in maintenance management is not without challenges. Organizations need to address:
- Data security: Safeguarding sensitive data is critical in AI implementations.
- Change management: Employees need training and support to adapt to new technologies.
- Cost of implementation: Initial investments in AI systems can be substantial, though the long-term benefits often outweigh these costs.
Closure
In the realm of modern operational strategies, the conclusion serves as a vital summation of the insights gathered throughout this comprehensive exploration of maintenance management. It encapsulates the essential themes discussed, weaving together the importance of effective maintenance practices and their impact on an organization’s overall performance.
Effective maintenance management is not merely a backend function; it is a critical component that drives operational efficiency and ensures sustainability. By understanding the frameworks presented in this article, organizations can delve deeper into their maintenance methodologies, explore new technologies, and implement strategies that pave the way for longevity and enhanced productivity of their assets.
Summary of Key Takeaways
- Maintenance Strategies are Integral: Approaching maintenance from a strategic angle allows businesses to mitigate risks and reduce downtime, resulting in cost savings.
- Technology Enhances Maintenance: Utilizing tools such as Computerized Maintenance Management Systems (CMMS) and IoT sensors situates organizations at the forefront of predictive maintenance.
- Proactivity is Essential: Transitioning from reactive to proactive maintenance not only aids in reducing failures but also extends asset life and improves operational metrics.
- Training is Paramount: Ensuring staff is well-trained on new technologies and processes is critical for the successful implementation of any maintenance strategy.
- Metrics Drive Improvement: Establishing and tracking key performance indicators (KPIs) allows organizations to gauge their maintenance efficacy and make informed adjustments.
Call for Action in Organizations
Organizations need to recognize the urgency of refining their maintenance practices. This guide underscores that maintenance management must evolve continuously to meet the demands of rapidly changing technology and market conditions. Here are some actionable steps:
- Assess Your Current Practices: Take stock of existing maintenance processes to identify areas of improvement. This involves evaluating your current technology and methodologies.
- Invest in Technology: Explore investments in CMMS and smart technologies to streamline operations and enhance data analysis capabilities.
- Develop a Culture of Continuous Improvement: Encourage a mindset that values ongoing learning and adaptation in maintenance practices. Regular training sessions can facilitate this.
- Engage Stakeholders: Foster collaboration between maintenance teams, management, and IT departments to align objectives and resources effectively.
Adhering to these action points can fortify an organization’s maintenance strategy, ensuring longevity and maximizing efficiency in operations. Ultimately, the conclusion of this article is not an endpoint; rather, it is an invitation for organizations to embark on a transformative journey in maintenance management.