A Comprehensive Guide to Business Work Orders
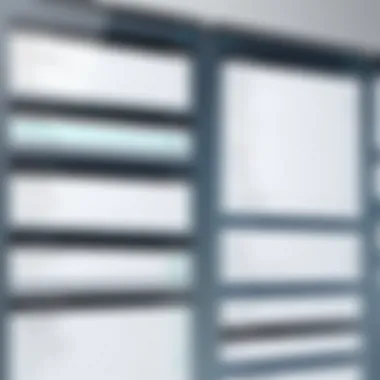
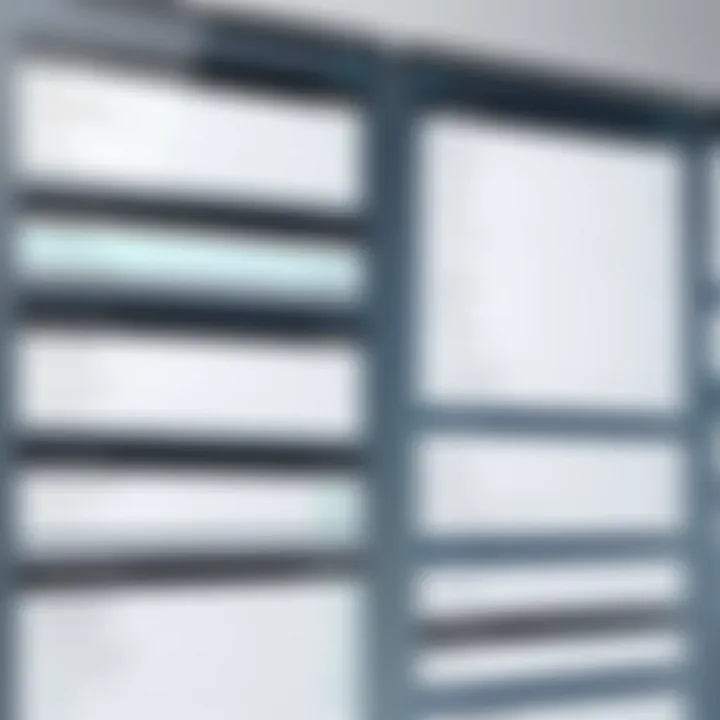
Intro
In todayโs fast-paced corporate landscape, the ability to manage tasks efficiently can make or break a business. One critical component of a smooth operational flow is the work order. These requests facilitate communication between departments, ensuring that tasks, repairs, or projects get done without a hitch. In essence, a work order serves as a bridge, connecting those who need something done with those who can do it.
While some might think of work orders as merely a bureaucratic necessity, they are, in fact, the lifeblood of many organizations. From maintenance requests in manufacturing plants to requests for software development, work orders are omnipresent.
This guide aims to peel back the layers of this intricate system to offer not just an understanding, but a comprehensive toolkit for implementing and optimizing work orders in your business.
Letโs dive into the Key Features of work orders and explore why they are so crucial in today's business configurations.
Prelims to Business Work Orders
In the contemporary workspace, business work orders serve as a linchpin for efficient operations. They often represent the foundation upon which tasks are planned, executed, and tracked across various departments. A work order can be viewed as a formal instruction for completing a specific task or jobโbe it a repair, maintenance, or service request.
Defining and understanding these work orders is crucial, as they not only organize the workload but also ensure accountability and clarity among team members. Work orders create a trail of documentation that can be referred back to, which is invaluable when evaluating performance or analyzing the efficiency of a given process.
One might liken work orders to a blueprint in construction: it provides direction, outlines specific tasks, and leads to the eventual completion of a project. As organizations grow, the complexity of operations can increase; this is where work orders shine. They simplify communication across teams, allowing every member to know their responsibilities and deadlines, which ultimately fosters a culture of productivity and collaboration.
When exploring the significance of work orders, the advantages are as clear as day. They streamline workflows, enhance transparency, and promote effective monitoring of resources and time. Ultimately, understanding work orders is not just about managing tasksโit's about optimizing the way a business operates.
"Every minute spent on mission-critical work orders is a minute well-invested; it turns chaos into order."
Defining Work Orders
A work order is essentially a document that details specific tasks assigned to an individual or team within a business. It typically includes essential information such as task descriptions, deadlines, necessary resources, and responsible personnel. Furthermore, the work order provides a reference point that can be used for future audits, both for accountability and for enhancing operational efficiency.
In many sectors, these documents can be generated manually or through digital systems, allowing for real-time updates on progress and modifications. The transition to digital work order systems has revolutionized how businesses manage their workloads, granting them the ability to track performance metrics and allocate resources efficiently.
The Importance of Work Orders in Business
The relevance of work orders goes beyond their basic function. They play a vital role in enhancing overall business efficiency, which can significantly affect profitability and customer satisfaction. Here are a few key points on why work orders are paramount:
- Accountability: Clear assignments lead to greater accountability. Team members know what is expected, which can minimize misunderstandings.
- Resource Management: Work orders help organizations effectively allocate resources, whether they be human, financial, or temporal. This can lead to decreased operational waste and increased productivity.
- Improved Communication: They promote clarity across teams. When everyone knows the current tasks and responsibilities, it creates a cohesive work environment.
- Performance Insights: With well-structured work orders, businesses can generate reports that reveal performance trends and help in making informed decisions.
In summary, business work orders are not just administrative formalities; they are a strategic tool for ensuring that every cog in the wheel is turning smoothly and directionally.
Types of Business Work Orders
Understanding the varieties of business work orders is crucial for any organization aiming to streamline its operations and boost productivity. Each type of work order serves a distinct purpose and caters to specific needs within a business. Knowing when and how to utilize them can make a mountain of difference in efficiency. Hereโs a pulled-back view of the different classifications of work orders that businesses typically rely on, which can help in sharpening operational focus and refining systematic processes.
Internal Work Orders
Internal work orders are essentially internal requests. They are generated within an organization to execute tasks or projects that don't require external assistance. The beauty of internal work orders lies in their ability to pinpoint accountability and ensure clarity of roles. When an employee raises an internal work order, they provide detailed instructions that guide the team in executing their tasks. Common examples include inventory requests between departments or maintenance tasks on in-house equipment.
Benefits of Internal Work Orders:
- Clarity & Accountability: Assigns responsibility to specific teams or individuals.
- Streamlined Communication: Reduces misunderstandings by providing precise instructions.
- Enhanced Tracking: Ensures that all tasks can be monitored for progress and efficiency.
External Work Orders
On the flip side, external work orders involve vendors or service providers outside the organization. These orders are used for procuring goods and services that the company doesnโt have in-house capabilities to fulfill. External work orders often require a more detailed approval process and clear definitions of deliverables and timelines. For instance, a contracting firm may issue work orders for specialized tasks like construction or IT services.
Considerations for External Work Orders:
- Detailed Specifications: Clear that expectations are well laid out to avoid confusion.
- Budget Concerns: Must stay within budget while achieving desired outcomes.
- Contractual Obligations: Careful monitoring is needed to ensure vendors fulfill their commitments.
Maintenance Work Orders
Maintenance work orders are designed specifically for upkeep and repair tasks targeting equipment or facilities. They serve as a proactive approach to prolonging the life of assets and minimizing downtime. A well-maintained asset translates to better overall productivity; hence, systematically managing these work orders is non-negotiable.
Key Aspects of Maintenance Work Orders:
- Preventive Measures: Can include routine checks and repairs that stop larger breakdowns from occurring.
- Scheduled Maintenance: Regularly scheduled tasks based on equipment usage or time intervals.
- Safety Compliance: Ensures that safety regulations are met, minimizing risks in the workplace.
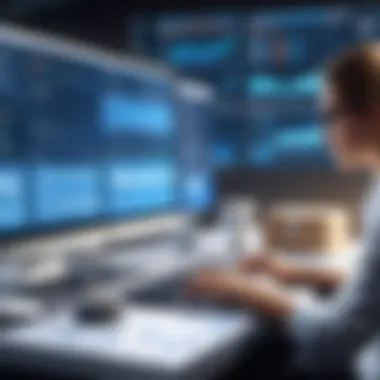
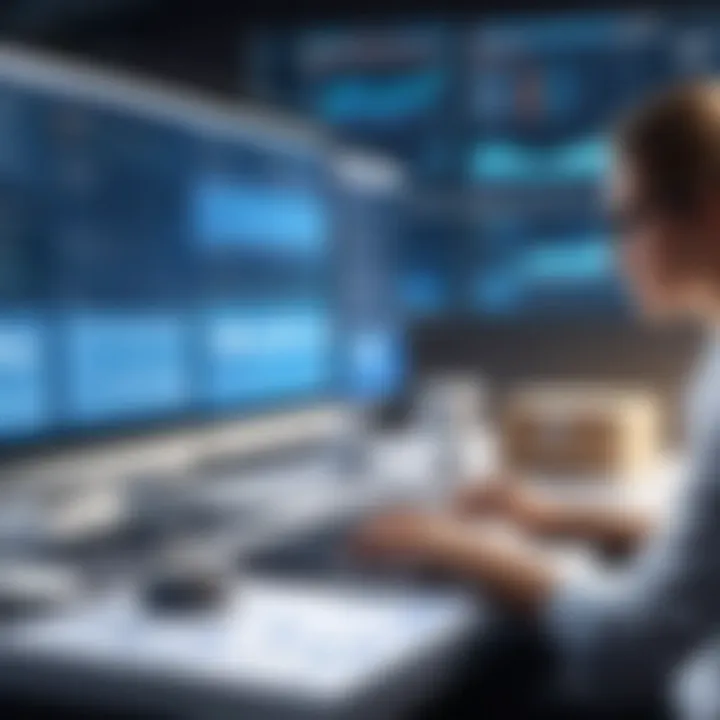
Service Work Orders
Service work orders differ from general maintenance requests, focusing instead on customer-facing tasks or internal services provided to employees, such as IT support or facility management. These work orders tend to have quick turnaround times and may sometimes operate under a looming deadline, especially in fast-paced environments.
Important Features of Service Work Orders:
- Timeliness: Must be handled promptly to avoid impacting service delivery.
- Customer Impact: Directly affects customer satisfaction and employee productivity.
- Documentation: Requires clear recording of the service completed, time taken, and customer feedback for future improvements.
Understanding the diverse functions of work orders helps organizations maximize their operational capabilities as well as strategically leverage their resources.
By recognizing and applying the appropriate type of work order for each task, businesses can realize substantive savings in time and costs, ultimately leading to better profitability. This differentiation is not just academic; itโs a pragmatic approach to refining workflow and achieving strategic objectives efficiently.
The Work Order Process
The work order process is a crucial backbone of efficient business operations, guiding teams through the multitude of tasks needed to keep projects on track. It serves as a roadmap that outlines the necessary actions needed to complete a job, ensuring each step is executed in a timely manner while adhering to company standards. A streamlined work order process not only enhances productivity but also minimizes mistakes and miscommunication, making it an integral part of an organizationโs workflow.
Understanding this process can make the difference between chaotic project management and smooth, productive execution.
Initiation of Work Orders
The initiation phase is where it all begins. This stage is vitally important because it sets the tone for everything that follows. When a work order is initiated, it lays down the foundational work for the tasks ahead.
Creating a work order often starts with identifying specific needs or issues within the organization. For example, if a manufacturing line is experiencing frequent downtimes, a work order for maintenance might be generated.
Some key aspects involve:
- Accurate data collection: Gathering the right information ensures the work order addresses the real problem.
- Clear descriptions: A straightforward description detailing the task minimizes confusion.
- Immediate delegation: Assigning tasks right from the start can enhance accountability and speed up the process.
By building a clear foundation right off the bat, businesses can ensure that everyone involved knows their responsibilities and timelines.
Approval Workflows
Once a work order is initiated, it often undergoes an approval workflow. Approval workflows are crucial for maintaining quality control and resource management. This step isn't just about rubber-stamping requests; itโs often rife with decisions that can impact project funding, timing, and resource utilization.
In a well-structured approval process, several elements come into play:
- Multi-level approval: Some requests may need input from various departments or higher management.
- Timeliness: Delays in approval can stall projects, making a defined approval timeline essential.
- Transparency: Using platforms that provide trackable records of approvals can help keep everyone informed about the status of work orders.
A meticulous approval workflow signifies a business's commitment to accountability and efficiency in its operations, helping to ensure that all projects are in alignment with organizational goals.
Execution and Tracking
With approvals in place and orders issued, the execution and tracking of work orders come into play. This phase is where the rubber meets the road. Tasks must be carried out according to the work order specifications.
Implementing effective tracking systems can dramatically enhance this phase. Consider:
- Real-time updates: Using digital tools that allow for instant updates keeps everyone on the same page.
- Task prioritization: Not every work order is of equal importance; some tasks might need to be completed sooner than others.
- Feedback loops: Creating systems for receiving feedback during execution allows for real-time adjustments and better end results.
These elements combined facilitate not just adherence to timelines but also quick adaptations to any changes that may arise in the course of execution.
Closing Work Orders
Closing out a work order may often feel like a formality, but it is a significant piece of the puzzle. This process holds value far beyond simply ticking off a checkbox. It is a point of reflection, a chance to analyze the completed tasks and their outcomes.
Some noteworthy considerations include:
- Documentation: Documenting the closure process and outcomes provides a record that can be reviewed in the future.
- Lessons learned: Reflecting on what worked and what didn't can be invaluable for process improvement.
- Feedback solicitation: Gathering insights from those involved can lead to richer understanding and subsequent enhancements in the workflow.
Closing a work order isn't merely about ending a task; it is about ensuring that the organization is set up for future successes, armed with the knowledge learned along the way.
Digital Solutions for Work Order Management
As businesses continue to evolve in the digital age, managing work orders has transitioned from traditional, paper-based systems to more sophisticated digital platforms. The significance of digital solutions for work order management is immenseโthey enhance accuracy, speed, and coordination throughout the workflow. When organizations adopt these systems, they open themselves up to a world of efficiency that not only streamlines operations but also saves valuable time and resources. Therefore, understanding their benefits and features is essential for any organization looking to refine their workflow processes.
Benefits of Digital Work Order Systems
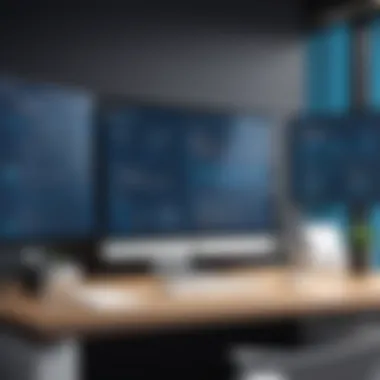
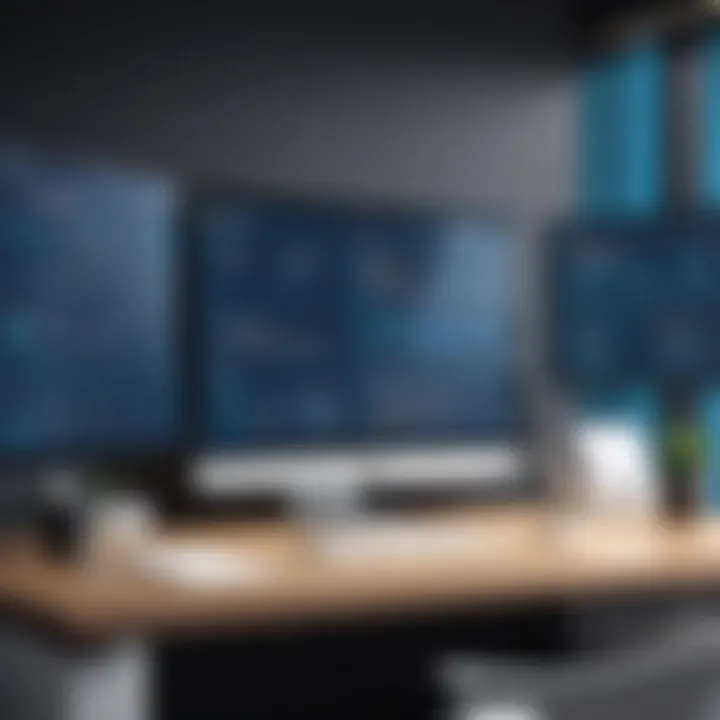
Digital work order systems offer several compelling advantages:
- Real-time Data Access: Immediate access to work order information ensures that all team members are on the same page. This helps in eliminating misunderstandings and errors that often arise from miscommunication.
- Increased Accountability: With digital systems, it's easier to track who is responsible for what tasks. Each stepโbe it initiation, approval, execution, or closureโis documented, making accountability clear and enhancing overall project management.
- Enhanced Tracking and Reporting: Digital platforms come equipped with robust reporting tools that allow businesses to analyze performance metrics effectively. Decision-makers can quickly assess productivity trends, monitor workflow efficiency, and identify bottlenecks.
- Improved Scheduling: Digital systems generally include calendaring features that help prioritize tasks based on urgency and resources available. This leads to better time management and utilization of personnel.
- Cost Efficiency: By streamlining processes and reducing manual errors, businesses can save on operational costs. Digital solutions also minimize the need for physical storage of paper documents, thus saving on space and supplies.
"Implementing digital work order systems is not just about going paperless; itโs about transforming how organizations operate."
Popular Work Order Management Software
Various software solutions stand out in the domain of work order management. Some of the most recognized include:
- ServiceNow: Known for its comprehensive range of IT service management capabilities, ServiceNow helps streamline work orders with an intuitive interface.
- UpKeep: This mobile-first platform allows users to manage and assign work orders on the go, making it ideal for maintenance teams.
- Smartsheet: Its collaborative features make Smartsheet a favored choice for teams looking to manage work orders collaboratively, in real-time.
- Monday.com: With customizable workflows and visual project management, Monday.com is designed for flexibility, adapting to various business needs.
- Trello: While primarily a project management tool, Trello's visual boards can efficiently handle simple work order processes, especially for smaller teams.
Features to Look for in Software Solutions
When selecting a work order management software, certain features should be a priority:
- User-Friendly Interface: A simple, intuitive interface is crucial for ensuring that all team members can quickly adopt the system without extensive training.
- Mobile Accessibility: Given that many field workers are on the go, having a mobile-friendly platform allows for work orders to be managed from anywhere, enhancing flexibility.
- Integration Capabilities: The ability to integrate with other business systemsโsuch as inventory management, finance, and CRM toolsโcan significantly enhance overall business efficiency.
- Customizable Templates: Each organization has unique workflows, so customizable templates can streamline the work order process specific to the team's needs.
- Robust Reporting Tools: As mentioned earlier, the ability to generate reports is essential for tracking performance, identifying trends, and making informed business decisions.
Best Practices for Managing Work Orders
Managing work orders effectively is akin to fine-tuning a well-oiled machine. It involves strategies that enhance workflow, improve accountability, and ultimately boost productivity within an organization. By adopting best practices, businesses can streamline their work order processes, ensuring tasks are completed efficiently and to the desired standard.
Standardizing Processes
One cornerstone of effective work order management is the standardization of processes. Establishing a consistent approach across the board minimizes confusion and errors, leading to smoother operations. This entails creating templates and clear protocols for every type of work orderโfrom internal requests to maintenance tasks.
- Clarity: When employees know what to expect and how to proceed, they can focus more on the work itself rather than navigating convoluted systems.
- Efficiency: Standard processes reduce the time spent on training new staff, as the system becomes more intuitive and manageable.
- Quality Control: A standardized approach allows for better monitoring of completed work, facilitating quality assurance and adherence to company policies.
Incorporating automation tools, such as workflow software or task management applications, can further enhance process standardization. This way, all employees follow the same pathways to completion, making it simpler to identify bottlenecks and rectify concerns.
Training and Communication
Another vital practice is the emphasis on training and communication. It's not enough to just set forth a set of procedures; teams must be well-equipped to navigate these systems and engage effectively with one another.
- Regular Training Sessions: Investing time in ongoing training keeps everyone updated on new systems and processes. This also reinforces the importance of adhering to work order protocols.
- Open Lines of Communication: Maintaining clear communication among team members ensures that issues are swiftly addressed. This can involve regular meetings or a dedicated communication platform where team members can raise concerns or provide updates on work order status.
Cultivating a culture where team members feel comfortable sharing feedback will also drive improvement in work order management.
Continual Improvement Strategies
Continual improvement is key for organizations seeking to adapt and thrive. The business landscape is always shifting, so regularly reviewing work order processes is crucial. Organizations should consider:
- Feedback Mechanisms: Surveys or feedback sessions with employees can unveil insights on what's working and what needs enhancement.
- Performance Metrics: Use specific KPIs to track performance over time; for instance, monitoring completion times, the accuracy of work orders, or employee satisfaction scores can provide actionable data.
- Periodic Reviews: Set intervals (e.g., quarterly or bi-annually) to assess work order strategies, making adjustment as warranted based on analysis and employee input.
Incorporating a mindset of continual improvement may require a shift in culture, but the benefitsโincreased efficiency, happier employees, and better overall outcomesโare well worth the effort.
Embracing best practices in managing work orders not only streamlines operations but also fosters a work environment that prioritizes effectiveness and employee satisfaction.
Impact of Work Orders on Business Efficiency
In todayโs fast-paced business landscape, understanding the impact of work orders on organizational efficiency is paramount. Work orders serve as a backbone for various operational activities. They clarify tasks, set timelines, and delineate responsibilities, enabling teams to coordinate effectively. When implemented properly, they not only streamline processes but also enhance communication among departments. This section delves into key areas that showcase the significance of work orders on business efficiency.
Work Orders and Project Management
Work orders play a pivotal role in project management. They establish a concrete framework for communication between project managers and team members. By detailing the scope of a project, work orders ensure that all contributors understand their roles. This clear delineation of tasks prevents overlaps and reduces confusion, allowing teams to function like a well-oiled machine.
- Task Clarity: Each member knows exactly what needs to be done and when.
- Resource Allocation: Enables efficient allocation of resources, ensuring that no one is left scrambling at the last minute.
- Progress Tracking: Managers can monitor progress against the outlined work orders, making it easier to identify bottlenecks or delays and adjust plans accordingly.
Moreover, integrating work orders with project management software can significantly enhance tracking capabilities. Teams can update progress in real time, allowing for quicker adjustments and collaboration when challenges arise.
"A well-defined work order can turn chaos into order, giving teams the clarity they need to meet project milestones."
Measuring Productivity Gains
To assess how work orders contribute to productivity, businesses can analyze specific metrics post-implementation. Metrics such as task completion time, resource utilization rates, and staff workload balance can provide insights on effectiveness. Here are some ways to quantify productivity gains:
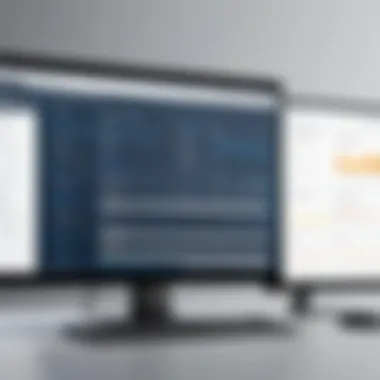
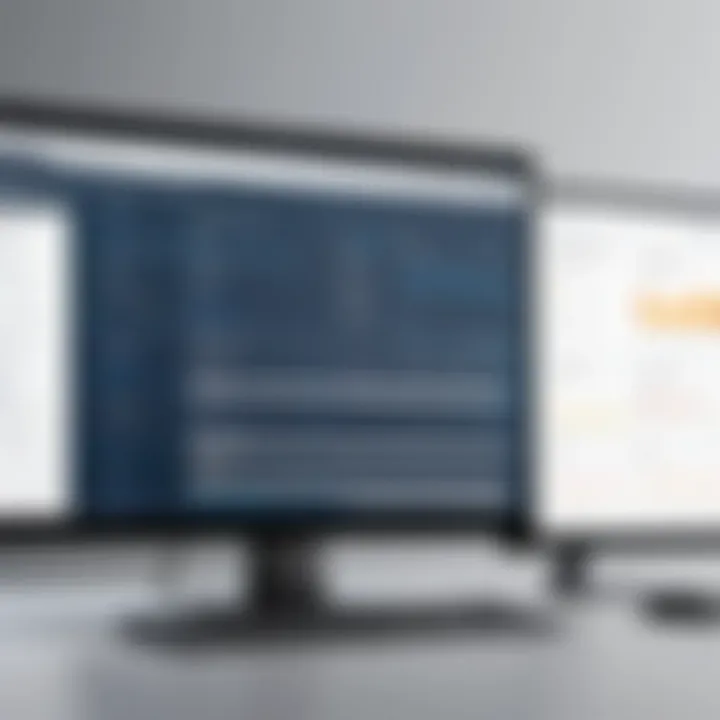
- Baseline Measurements: Before introducing work orders, establish baseline productivity metrics. This serves as a point of comparison once changes have been implemented.
- Task Completion Rate: Monitor how quickly tasks are finalized post-implementation of work orders. A decrease in completion times generally indicates an efficiency boost.
- Error Reduction: Work orders can lead to fewer errors or reworks due to their clear outlines, which can save time and resources.
- Employee Feedback: Regular surveys can also give insights into how employees perceive their workloads and clarity. Increased satisfaction often correlates with higher productivity levels.
Using these measurements, businesses can make data-driven decisions to optimize their work processes further. For organizations, understanding the correlation between work order systems and productivity is imperative for ongoing success.
By embracing efficient work orders, a business can redefine its operational efficiency, paving the way to heightened productivity and reduced delays.
Challenges in Work Order Management
Work order management is crucial for businesses that rely on structured workflows. However, it is not without its hurdles. Acknowledging these challenges is the first step toward enhancing efficiency in managing work orders. Addressing common issues not only brings about smoother operations but also uplifts the morale among team members, as they find themselves working in a more organized environment. This can ultimately lead to improved productivity and project outcomes.
Common Issues Faced
Every organization encounters particular issues that arise during work order management. Some predominant challenges include:
- Lack of Clarity: Oftentimes, work orders can become muddled and unclear. This ambiguity can lead to miscommunication about tasks, roles, and deadlines. Individuals might find themselves chasing vague instructions, leading to wasted time and frustrations.
- Inefficient Processes: Many businesses are stuck in their old ways, relying on manual processes to manage work orders. This can significantly slow down operations and cause bottlenecks. Paper trails and spreadsheets can quickly transform into a confusing labyrinth, making it difficult to track the status of work orders.
- Data Silos: In some cases, information gets trapped within departments. Without an integrated system, individuals cannot access vital information when they need it most. Such silos prevent the seamless flow of information that is critical in executing tasks efficiently.
- Inadequate Training: Employees often lack proper training on how to utilize work order systems effectively. New hires may not be familiar with established workflows, leading to mistakes that could have been avoided.
Ultimately, these challenges can snowball into larger issues, impacting the organizationโs overall performance and customer satisfaction.
Overcoming Resistance to Change
Change is often met with resistance, and work order management is no exception. Organizations tend to cling to familiar methods, even when those methods are inefficient. Overcoming this resistance is vital for improving work order management.
- Communicate the Benefits: Transparency is key. Itโs essential to convey how improved work order management tools can streamline processes and enhance productivity. Use real-life examples and data to showcase the improvements that can occur.
- Involve Employees in the Process: Engaging team members in the transition process fosters a sense of ownership. When they feel their opinions are valued, they are more likely to adopt new workflows and systems.
- Offer Comprehensive Training: Investing in proper training is non-negotiable. When individuals are confident in their skills, they are less likely to resist adapting to new procedures. Consider ongoing workshops and sessions to keep skills fresh.
- Be Incremental with Changes: Instead of implementing an overhaul all at once, consider taking small steps. Pilot projects can show tangible results, which can help grinnd more acceptance among skeptical individuals.
- Celebrate Milestones: Acknowledging small successes during the adaptation period can help boost morale. Celebrating achievements, no matter how minor, can create a positive atmosphere that encourages continued progress.
"Change is difficult at first, messy in the middle, and gorgeous at the end."
In summary, navigating challenges in work order management requires a focused approach. Embracing change, while addressing the common obstacles, can lead to a marked improvement in organizational productivity and efficiency.
The Future of Work Orders in Business
The ever-evolving landscape of business management undeniably shapes the future of work orders. As organizations clamor to remain agile in a dynamic market, understanding the trajectory of work order systems becomes essential. In this section, we will explore significant elements influencing this future, the benefits of embracing technological advancements, and key considerations businesses must keep in mind as they adapt to these changes.
Trends in Work Order Software
Several key trends are emerging in work order software that organizations must watch closely. One noteworthy trend is the increasing adoption of cloud-based solutions. These systems allow for seamless access to work order data from anywhere, fostering better collaboration among teams. Moreover, with cloud technology, updates and maintenance become less of a hassle, enabling companies to focus more on strategic initiatives rather than getting bogged down by software issues.
Another trend making its rounds is artificial intelligence integration. AI functionalities are helping to streamline task allocation, forecast resource needs, and even predict maintenance issues before they escalate. With businesses continually striving for operational efficiency, implementing AI can lead to significant productivity gains.
Additionally, mobile access to work order management is becoming the norm. Field technicians can receive real-time updates, enabling faster response times. This shift not only enhances productivity but also leads to improved customer satisfaction, as services can be delivered promptly and accurately.
- Cloud-Based Solutions: Greater flexibility and accessibility.
- AI Integration: Enhanced predictive capabilities and automation.
- Mobile Access: Real-time updates for field operations.
"Embracing technological innovation in work order management can profoundly impact operational efficacy and adaptability for businesses."
Integrations with Other Business Systems
Integrating work order systems with other business solutions is a crucial factor in enhancing overall organizational efficiency. Companies are increasingly recognizing that a siloed approach to operations is no longer tenable. By integrating work order systems with ERP, CRM, and inventory management software, organizations streamline their processes and minimize data inconsistencies.
For instance, an ERP integration allows for better resource planning, ensuring that materials and labor are aligned with the demands of ongoing projects. Similarly, linking with CRM systems ensures that customer-related tasks are prioritized and managed effectively, directly impacting customer experience.
When considering integrations, it's critical to assess not just the technology but also the human aspect. Employees must be trained not just in using the tools but in understanding how their interconnectedness can augment their workflows. It fosters a culture of collaboration and communication which is pivotal for success.
- ERP Integration: Aligns resource planning with project demands.
- CRM Integration: Enhances customer management and task prioritization.
- Employee Training: Ensures a smooth transition to integrated systems.
Closure
In the realm of business, the summation of diverse processes often culminates in a particular focus on how work orders shape organizational efficacy. This guide, with its expansive examination of business work orders, underscores their pivotal role, not merely as a framework for task delegation but as a catalyst for driving operational success.
The importance of work orders becomes distinctly apparent when considering several core elements. First, clarity of purpose is essential. Work orders serve as blueprints, outlining tasks with precision. This clarity minimizes confusion, streamlines activities, and ultimately fosters a cohesive work environment where all stakeholders understand their roles and responsibilities.
Second, effective communication is paramount in ensuring smooth execution. Work orders codify interactions among team members, reducing miscommunication and increasing accountability. Establishing a well-documented trail of instructions can be the difference between chaos and order, especially in complex projects involving multiple parties.
Moreover, the potential for data-driven insights is a game changer. Since work orders collect and record performance data, businesses can analyze trends over time. This analysis helps in not only identifying bottlenecks but also in refining processes for future projects. Making informed decisions becomes easier when you have relevant data at your fingertips.
Finally, work orders enhance efficiency and productivity in a measurable way. By instituting clear protocols for task management, organizations often see a reduction in downtime and resource wastage. Work orders bring structure that translates directly into improved performance metrics.
"Efficiency is doing better what is already being done."
โ Peter Drucker, Management Consultant
As the business landscape continue to evolve, adopting robust work order systems not only manifests operational enhancements but also equips organizations with the agility to adapt to changes swiftly. Closing our discussion with a reflection on work orders, itโs evident that they are not just operational tools; they signify a disciplined approach to steering the organization toward its goals. Through thoughtful implementation and continual improvement, the full benefits of work orders can be realized, from enhanced productivity to improved employee morale.
In summary, revisiting the role of work orders reinforces their significance as both a foundational and a strategic element in modern business practices.