Exploring PFEP Software for Supply Chain Efficiency
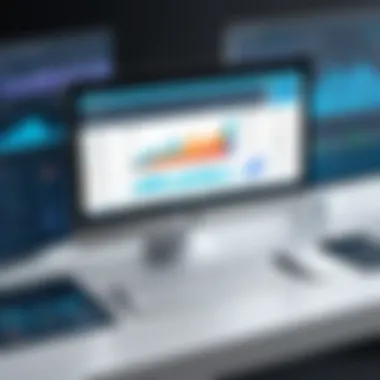
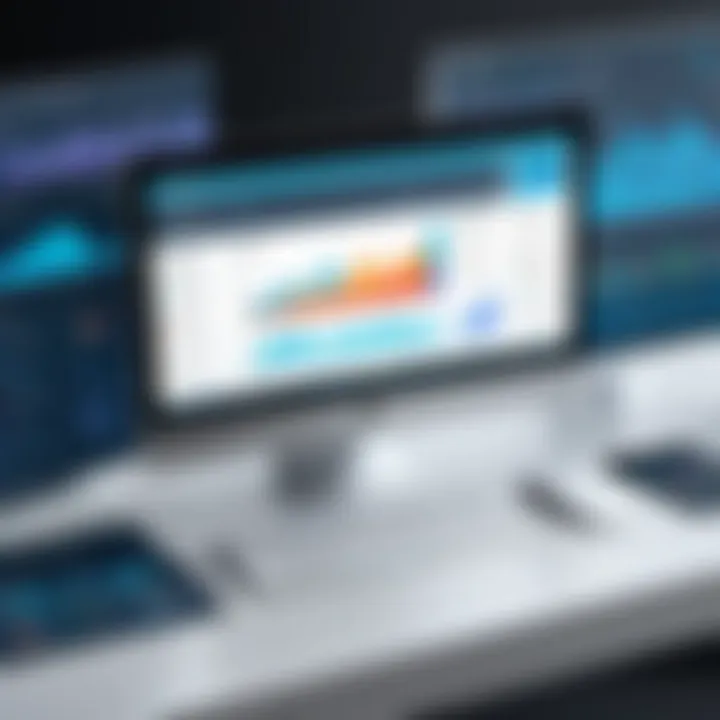
Intro
In the realm of modern supply chain management, proficiency in utilizing software tools is paramount. Businesses encounter numerous challenges in inventory management and operational efficiency. PFEP software emerges as a critical asset in addressing these issues. This section aims to guide decision-makers, IT professionals, and business owners through the essential aspects of PFEP software, highlighting its value and applications.
By comprehensively exploring its features, benefits, and pricing structures, stakeholders can make informed choices that enhance their operational strategies. This foundational understanding prepares organizations to effectively implement PFEP software and reap the advantages inherent in streamlined processes.
Key Features
Overview of Features
PFEP software is designed with powerful functionalities that aid in the seamless integration of supply chain processes. Key features include:
- Data Integration: PFEP software connects with existing systems to consolidate data across various platforms. This eliminates data silos, allowing for better analysis and decision-making.
- Real-Time Analytics: Users benefit from real-time insights into inventory levels and supply chain operations, enhancing responsiveness to market changes.
- Forecasting Tools: Advanced algorithms predict demand trends, enabling businesses to optimize their inventory levels and reduce wastage.
- Reporting Capabilities: Comprehensive reporting features allow stakeholders to track performance metrics and make data-driven decisions.
Unique Selling Points
The unique selling points of PFEP software distinguish it from other inventory management tools. These include:
- Customizable Solutions: The adaptability of PFEP software allows businesses to tailor functionalities to their specific needs.
- User-Friendly Interface: An intuitive design ensures ease of use for all team members, reducing the learning curve associated with new software.
- Scalability: As businesses grow, PFEP software can scale accordingly, accommodating increased complexity without sacrificing performance.
"Investing in PFEP software not only improves inventory management but also propels overall operational efficiency."
Pricing Structure
Understanding the pricing structure is essential for businesses evaluating PFEP software. Typically, prices vary based on features and user capacity.
Tiered Pricing Plans
- Basic Plan: Suitable for small businesses, it includes essential features like data integration and basic reporting.
- Standard Plan: Designed for medium enterprises, offering enhanced analytics and forecasting tools.
- Premium Plan: Provides full access to all features, including advanced reporting and customizable solutions.
Features by Plan
Each plan offers distinct features:
- Basic Plan: Limited data integrations and basic analytics.
- Standard Plan: Real-time analytics, better reporting, and some customization options.
- Premium Plan: All features of the Standard Plan plus comprehensive support and the most advanced customization.
This structured approach to pricing ensures organizations can select a plan that aligns with their operational demands and budget constraints.
Understanding PFEP Software
Understanding PFEP software is crucial for any organization aimed at enhancing their supply chain and inventory strategies. This software provides a structured approach to planning, forecasting, execution, and performance tracking. As businesses face increasing competition and pressure for efficiency, leveraging PFEP software becomes not just beneficial but necessary.
Investing time in understanding PFEP is important. It allows stakeholders to gain insights pertinent to their operational needs. PFEP software is generally designed to facilitate the management of inventory levels, optimize supply chain processes, and support data-driven decision making. For businesses with complex inventory systems, an informed use of PFEP can underscore profitability.
Definition and Purpose
PFEP, or Plan For Every Part, is a systematic methodology used for managing inventory in a more efficient manner. At its core, PFEP software enables companies to keep a comprehensive record of all parts involved in their manufacturing or supply chain process. The purpose is to assure accuracy and accessibility of information regarding inventory items, their locations, and their movement through the supply chain.
The main goal of PFEP software is to provide a unified platform to work with real-time data. This includes forecasting demand, tracking inventory levels, and ensuring that the right amount of items is available at the right time to meet customer needs. By utilizing it, organizations can minimize stockouts and excess inventory, thereby improving overall operational efficiency.
Historical Context
The concept of PFEP evolved alongside advancements in supply chain management practices. In the early 1990s, as businesses began adopting Just-In-Time (JIT) inventory practices, the need for a more structured approach to managing parts and supplies became evident. Early PFEP frameworks emphasized the need for detailed item tracking and justifiable inventory levels.
Over the years, the software has grown significantly. Initially limited to basic functionalities, modern PFEP solutions now incorporate advanced data analytics, integration capabilities, and automation features. This evolution has enabled companies to not just react to inventory demands, but also to anticipate and plan for them effectively.
Today, organizations that actively utilize PFEP software position themselves to tackle complex challenges in inventory management more successfully. This historical context shows how PFEP software serves as a pivotal tool in the contemporary supply chain landscape, promoting efficiency and optimization.
Key Features of PFEP Software
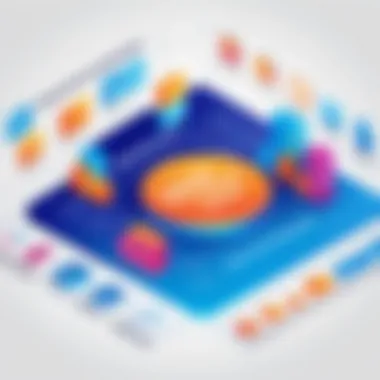
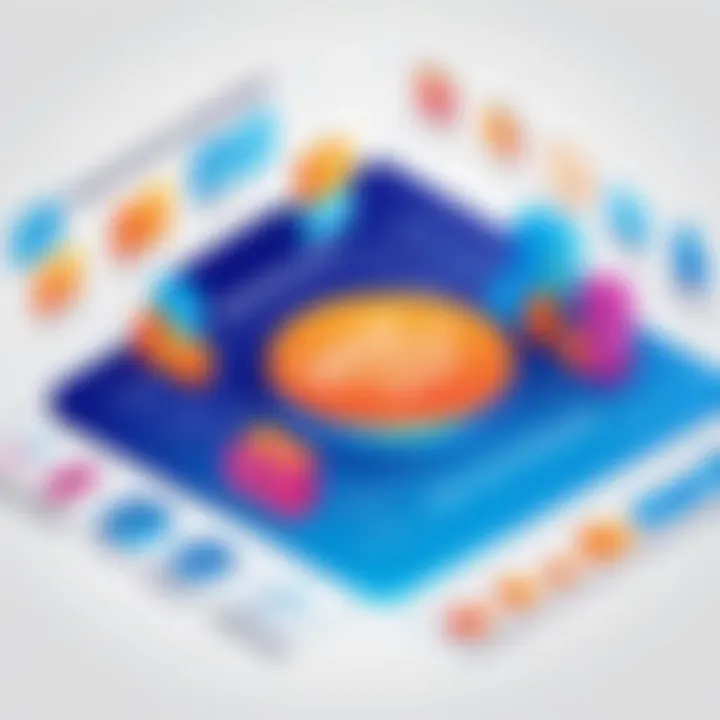
Understanding the key features of PFEP software is crucial for organizations looking to enhance their supply chain management and inventory practices. Each feature plays a significant role in operational effectiveness. These attributes not only streamline processes but also provide invaluable insights that can inform strategic decisions.
Data Collection and Management
Effective data collection and management form the backbone of PFEP software. These systems allow organizations to gather relevant data from various sources and consolidate that information into a central repository. By leveraging modern data architecture, PFEP software ensures that data is accurate, timely, and readily accessible. Furthermore, robust data management features support integration with existing databases, facilitating seamless data exchange across platforms.
An advanced system might utilize methods such as automated data extraction and real-time updates, thus minimizing manual input errors and ensuring data integrity. The road to obtaining reliable analytics is paved with reliable data collection processes.
Inventory Assessment Tools
Inventory assessment tools within PFEP software are designed to provide insights into stock levels, turnover rates, and product performance. These tools assist businesses in determining optimal inventory levels, thereby reducing holding costs and minimizing stockouts. A detailed analysis of historical data enables businesses to accurately forecast demand and adjust inventory policies accordingly.
In addition to basic tracking functionalities, many systems now offer predictive analytics that can signal when to reorder products. This proactive approach helps maintain an efficient flow of goods and supports better working capital management. Tools such as ABC analysis categorize inventory items based on usage, further refining the management process.
Reporting and Analytical Capabilities
Reporting and analytical capabilities are arguably among the most powerful features of PFEP software. Effective reporting tools provide users with insights into operational performance, inventory levels, and fulfillment metrics. The ability to generate customizable reports empowers decision-makers to focus on key performance indicators relevant to their specific goals.
Moreover, PFEP software often includes dashboards that visualize data trends over time, making it easier for stakeholders to interpret information without deep analytical expertise. By harnessing advanced analytical algorithms, organizations can uncover patterns in their data that inform strategic planning and execution.
"Data-driven decisions are the foundation of smart inventory management."
Integrating these analytical capabilities with real-time data feeds can enhance responsiveness to market changes, providing businesses with the agility needed in today’s ever-evolving landscape.
Understanding the key features of PFEP software, from data collection and management to robust analytics, is pivotal for any organization aiming to streamline its supply chain operations and enhance overall efficiency.
Benefits of Implementing PFEP Software
Implementing PFEP (Plan For Every Part) software can be transformational in supply chain and inventory management. The three primary benefits are enhancing operational efficiency, improving inventory accuracy, and cost reduction through optimization. These advantages lead to more streamlined processes and substantial savings for businesses.
Enhancing Operational Efficiency
Operational efficiency refers to how well an organization utilizes its resources to produce goods or deliver services. PFEP software provides tools that allow companies to plan every aspect of their parts handling. It automates various tasks like tracking inventory levels, ordering supplies, and scheduling deliveries. By employing PFEP software, businesses reduce manual paperwork and human error. Automation speeds up processes, leading to better decision-making and faster response times.
A detailed assessment of operations is essential. PFEP software gathers data from multiple sources, allowing decision-makers to identify bottlenecks. Companies can shift focus to improving processes that are underperforming. Consequently, organizations can allocate resources more effectively.
Improving Inventory Accuracy
Inventory accuracy is critical to maintaining a smooth supply chain. Companies rely on accurate inventory data to ensure they have the right products available at the right time. PFEP software enhances inventory accuracy through robust tracking methods. It monitors inventory levels in real-time, enabling businesses to adjust stock based on current demand.
Using PFEP software reduces discrepancies between actual stock and recorded inventory. Businesses can minimize overstock and stockouts. This level of accuracy leads to better customer satisfaction and loyalty, as customers receive their orders on time without delay.
Cost Reduction Through Optimization
Cost reduction is a significant concern for businesses aiming to increase profitability. PFEP software enables organizations to optimize their inventory management processes. By improving forecasting accuracy, businesses can make more informed purchasing decisions. This optimization leads to less capital tied up in excess inventory.
Moreover, PFEP software streamlines vendor management. Suppliers can be assessed based on performance, allowing businesses to select the most reliable partners. Better supplier relationships can result in reduced costs through negotiated discounts or terms.
"Effective management of inventory not only cuts costs but enhances overall competitiveness in the market."
Challenges in PFEP Software Implementation
Implementing PFEP software is fraught with challenges that can impede its success. Recognizing these challenges early is crucial for organizations aiming to achieve efficient inventory management and supply chain versatility. By understanding the hurdles, stakeholders can formulate strategies to navigate the complexities of software deployment. The consequences of ignoring these challenges can be severe, potentially leading to wasted resources and missed opportunities. Therefore, addressing key areas—such as data integration issues, change management concerns, and user training requirements—cannot be understated.
Data Integration Issues
Data integration stands as one of the foremost challenges in PFEP software implementation. It is vital for organizations to consolidate information from various sources, such as ERP systems, warehouse management systems, and inventory databases. When these systems lack compatibility, or when data is siloed, the coherence of information suffers. This inefficiency can lead to inaccurate forecasting and decision-making.
"Proper data integration ensures that all stakeholders can access real-time data, reducing errors and enhancing transparency."
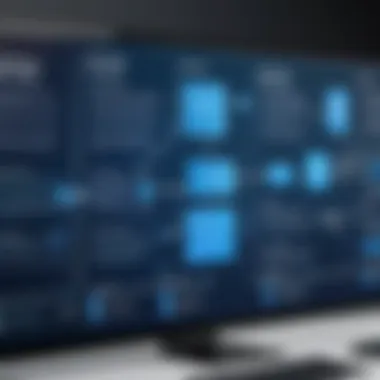
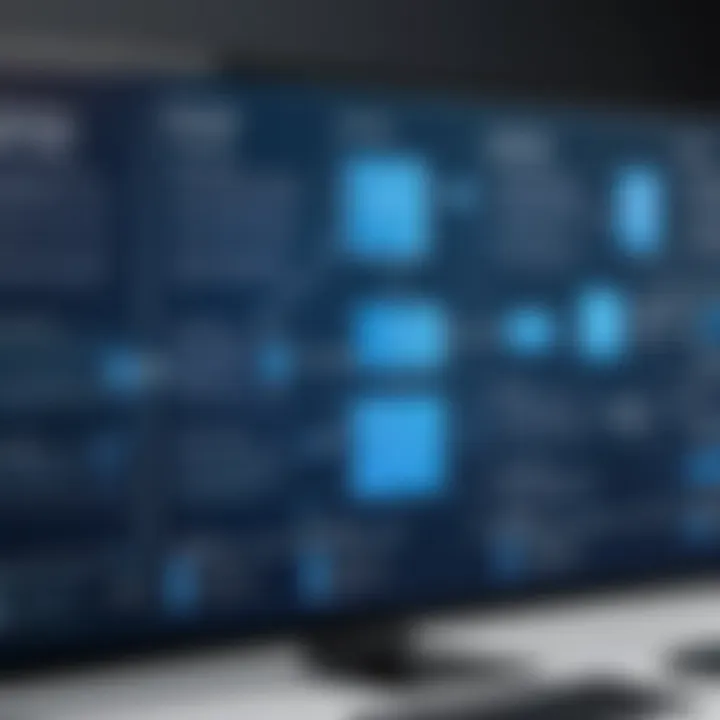
To effectively handle data integration:
- Assess existing data sources carefully.
- Ensure APIs and integration points are well-defined.
- Prioritize data quality to prevent garbage in, garbage out scenarios.
For example, if a logistics network uses disparate systems, manually reconciling data from these systems can become time-consuming and prone to errors. Adopting a cloud-based PFEP application can mitigate such issues, allowing for smoother data flows.
Change Management Concerns
Another significant hurdle is change management. Transitioning to a new PFEP software solution necessitates not only new tools but often a transformation in organizational culture. Employees may resist changes due to fears of job loss or the discomfort of adapting to unknown technologies. Managing this change thoughtfully is essential for easing the transition period.
Implementing effective change management includes:
- Communicating the benefits of PFEP software clearly to all stakeholders.
- Involving employees early in the process, allowing them to voice concerns.
- Providing a detailed roadmap for the transition.
By fostering a culture that embraces change, organizations can minimize frustration and foster acceptance among employees. Hence, effective change management will enhance the overall implementation success rate.
User Training Requirements
Lastly, user training is an indispensable component of a successful PFEP software implementation. No matter how effective the software may be, its potential can only be realized if users are competent in utilizing its features properly. Training should encompass various types of users, from IT professionals to operations staff, each with differing technical proficiencies.
To ensure effective user training:
- Assess the current skill levels of staff and customize training accordingly.
- Use a variety of training formats: workshops, online tutorials, and hands-on sessions.
- Measure training effectiveness through feedback and practical exercises.
Organizations can also consider appointing internal champions—employees who become proficient in the software and can assist their peers. Such initiatives not only enhance competency but also contribute to a supportive environment for users who may feel overwhelmed by the new system.
Evaluating PFEP Software Solutions
Evaluating PFEP software solutions is a crucial step for organizations aiming to enhance their supply chain and inventory processes. A well-chosen PFEP software can transform how data is managed, leading to improved efficiency and accuracy. Given the rise of digital transformation in the B2B sector, it is imperative to make informed decisions about which software fits an organization’s unique needs.
In this section, we will explore essential elements, benefits, and considerations involved in evaluating PFEP software solutions. The objectives here are to highlight why evaluation is important, outline criteria for selecting the right software, and provide insights into vendor comparisons.
Criteria for Selection
The selection process of PFEP software requires a structured approach. There are several criteria that decision-makers should consider:
- Functionality: Assess what features and functionalities are available. Does the software provide comprehensive data analysis, inventory management, and reporting tools?
- User Experience: A user-friendly interface is critical. If employees find the software complicated, it may lead to errors and decreased productivity.
- Integration Capabilities: Ensure the software can integrate well with existing systems, such as ERP and supply chain management software. Compatibility will reduce overall implementation time.
- Scalability: Choose software that can grow with your organization. As business needs evolve, the software should adapt accordingly.
- Cost: Consider both the initial investment and ongoing costs, including subscriptions, maintenance fees, and updates.
- Support and Training: Evaluate the level of customer support provided by the vendor. Is training available to ease the transition for users?
Using these criteria will guide organizations towards finding a PFEP software that aligns with their operational goals while maximizing return on investment.
Vendor Comparisons
When examining different PFEP software vendors, comparisons are essential to identify suitable options. Key aspects to focus on include:
- Reputation: Look for reviews and testimonials. Research companies through platforms like Reddit or dedicated software review sites to gain insights from current users.
- Offerings: Different vendors may offer distinct modules and features. Analyze which vendor aligns with your specific needs.
- Customer Support: Evaluate the quality and accessibility of each vendor's customer service. Quick responses and comprehensive support can save time.
- Trial Periods: Many vendors offer free trials. Utilize these opportunities to test software functionalities before committing to purchase.
"Selecting the right PFEP software is more than a procurement action; it is a strategic decision that can define the trajectory of an organization’s operational success."
By critically evaluating software solutions and comparing vendors based on essential criteria, organizations can position themselves to make informed choices that lead to significant operational improvements.
Best Practices for PFEP Software Adoption
Adopting PFEP software is a significant step for any organization looking to optimize its supply chain management and inventory control processes. Best practices for implementing this software ensure successful integration into existing operations. These practices fortify not only operational efficiency but also facilitate a smoother transition for all stakeholders involved. Organizations should approach adoption holistically, considering both technology and the people who will use it.
Establishing Clear Objectives
To maximize the value of PFEP software, it is crucial for organizations to define specific goals right at the outset. What do you want to achieve with the software? Are you looking to reduce inventory costs, improve turnover rates, or enhance data accuracy? Establishing clear objectives helps steer the implementation process. These objectives serve as benchmarks against which success can be measured.
- Define measurable outcomes like percentage reductions in stock discrepancies or improvements in order fulfillment times.
- Ensure that these goals align with the broader business strategy to justify the software investment.
- Communicate these objectives clearly to all team members to foster a collective understanding of the software’s purpose.
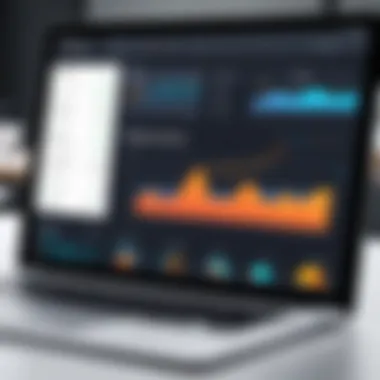
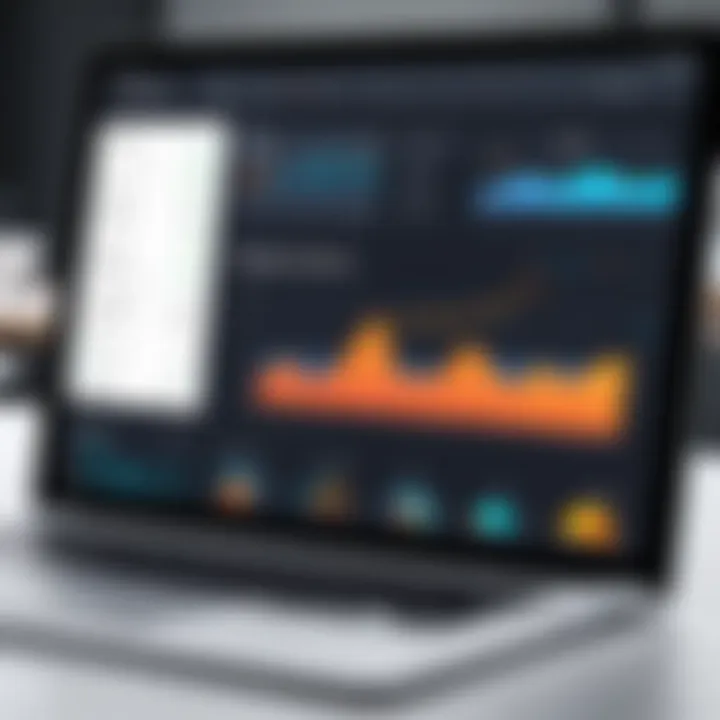
Setting clear objectives will guide the deployment process and make it easier to track progress.
Engaging Stakeholders Early
Engaging stakeholders is essential for fostering a shared vision and increasing buy-in for the PFEP software. Key stakeholders include supply chain professionals, inventory managers, IT personnel, and even top executives. Involving these individuals early in the adoption process can significantly mitigate resistance and enhance cooperation. Stakeholders can provide valuable insights on system requirements and potential challenges.
- Conduct workshops or meetings to gather input and address any concerns.
- Highlight how PFEP software benefits each department involved. This helps in establishing trust among users.
- Create a feedback loop, allowing stakeholders to express their experiences and participate in refining goals as the adoption progresses.
"Successful software adoption hinges on the early involvement of stakeholders. Their support can make or break the implementation process."
By fostering a collaborative atmosphere early on, organizations can ensure that all necessary perspectives are considered, resulting in a more effective implementation of PFEP software.
Real-World Applications of PFEP Software
The relevance of PFEP software in practical applications cannot be overstated. This software serves as a strategic tool, enhancing not only operational efficiency but also aiding organizations in meeting specific inventory management goals. By providing a structured approach to data management and analysis, businesses can adapt to various conditions and challenges in real-time.
Case Studies: Successful Implementations
Several case studies illuminate the effective use of PFEP software across industries. For instance, a leading automotive manufacturer adopted PFEP solutions to streamline their supply chain. They integrated various data sources, which facilitated real-time inventory tracking. As a result, they reported a significant reduction in excess stock and an increase in order fulfillment rate. This case underscores that successful implementation often rests on clear objectives and robust data integration.
Another example can be seen in the fast-moving consumer goods (FMCG) sector. Here, PFEP software played a crucial role in optimizing warehouse management. By utilizing detailed analytical features, the company not only reduced storage costs but also improved the accuracy of inventory distribution. This led to enhanced customer satisfaction as product availability improved considerably.
Industry-Specific Use Cases
PFEP software is versatile and can be tailored to the needs of different industries. In the pharmaceutical industry, for example, it helps organizations manage regulatory compliance while optimizing supply chains. Accurate data handling ensures pharmacies meet the necessary standards, leading to safer medication distribution.
In the electronics sector, companies utilize PFEP tools to manage complex inventory requirements. With rapid technological advancements, electronic goods have a short shelf life. PFEP software enables quick stock turnover, reducing waste.
Overall, the practical applications of PFEP software across various industries highlight its importance as a valuable asset for operational success. By understanding these use cases, organizations can leverage the software to achieve significant gains in efficiency and cost-effectiveness.
Future Trends in PFEP Software
Understanding the future trends in PFEP software is crucial for businesses aiming to maintain a competitive edge in inventory management and supply chain efficiency. As technology continues to evolve, companies need to adapt to changes that influence operational practices. Future trends may impact decision-making processes and the overall effectiveness of PFEP software solutions. By anticipating these trends, organizations can position themselves to leverage advancements in technology and evolving industry standards in a way that enhances productivity and strategic planning.
Technological Advancements
Technological advancements play a significant role in shaping PFEP software capabilities. Emerging technologies like artificial intelligence (AI) and machine learning (ML) are becoming integral parts of supply chain operations. These technologies provide the ability to analyze large datasets quickly, making it easier to forecast demand more accurately. Automation is also gaining traction, streamlining repetitive tasks which frees up resources for more strategic initiatives. Moreover, cloud computing facilitates real-time data sharing among stakeholders, enhancing collaboration and enabling agile responses to market changes.
Consider the following aspects of technological advancements in PFEP software:
- Enhanced Data Analytics: Advanced analytics tools can transform how businesses interpret inventory data, leading to more informed decision-making.
- Predictive Modeling: Utilizing AI for predictive analytics can help companies better prepare for fluctuations in supply and demand.
- Integrative Platforms: A move towards generalized platforms that integrate various functions, like inventory management and customer relationship management, is observable.
"Adapting to technological advancements in PFEP software not only leads to improved efficiency but also drives innovation within supply chains."
Shifts in Industry Standards
As the market landscape changes, so do industry standards concerning PFEP software. Key shifts focus on sustainability, transparency, and the integration of advanced software capabilities. Businesses are increasingly expected to demonstrate eco-friendly practices and ethical sourcing, which means that PFEP software must adapt to include functionalities that facilitate these requirements. Furthermore, regulatory compliance is tightening, necessitating that software solutions cater to real-time reporting and auditing expenses.
Here are several key shifts in industry standards to consider:
- Sustainability Practices: Companies are being held accountable for their environmental impact, leading to features in PFEP software that track sustainability metrics.
- Transparency in Supply Chains: A growing demand for transparency is driving software development towards providing detailed visibility into supply chain processes.
- Adaptive Compliance Features: With changing regulations, it's essential for PFEP software to incorporate features that help organizations remain compliant with local and international laws.
Finale
The conclusion is an essential component of this article, consolidating various insights on PFEP software and underpinning its significance in modern supply chain management. This section aims to summarize the key aspects discussed throughout the article while reinforcing the impact of PFEP software on decision-making and operational excellence.
Recap of Key Points
- Definition and Purpose: PFEP software serves to provide a structured approach to inventory management, focusing on precise data handling and optimization strategies.
- Key Features: It includes tools for data collection, inventory assessment, and advanced reporting features that support efficiency and decision-making.
- Benefits: Implementing PFEP software can result in enhanced operational efficiency, improved inventory accuracy, and reduced costs.
- Challenges: There are hurdles such as data integration issues, change management concerns, and user training needs that firms must navigate during implementation.
- Best Practices: Establishing clear objectives and involving stakeholders early in the process are vital for successful adoption of PFEP software.
- Future Trends: The software landscape is evolving, driven by technological advancements and shifts in industry standards, calling for continuous adaptation.
Final Thoughts on PFEP Software
PFEP software is not merely a tool but a pivotal enabler of efficient supply chain operations. As businesses strive to meet growing demands, leveraging PFEP software becomes critical. It streamlines processes that lead to higher accuracy and diminished waste.
Organizations willing to invest the resources needed to address implementation challenges will find the rewards substantial. The future is bright for those who embrace the capabilities of PFEP software. By understanding its benefits and intricacies, businesses can optimize operations, ultimately leading to sustainable growth.
"Without a structured approach to inventory management, businesses face increasing inefficiency and lost opportunities."